Maximizing Efficiency
Maintaining Equipment Health at Reworld Waste Management
In the world of waste management, efficiency and reliability are paramount. To ensure seamless operations, the company relies on a range of equipment at their facilities. Let’s delve into some real-world scenarios at Reworld that showcase the importance of equipment health monitoring and the actions taken to prevent failures. These real-world examples showcase how Condition Based Monitoring (CBM) and proactive intervention can avert potential disasters, reduce downtime, and ensure the seamless functioning of waste management facilities.
Where KCF is deployed
Reworld Locations IN Partnership with KCF Technologies:
ALABAMA – Huntsville | CALIFORNIA – Stanislaus | CONNECTICUT -Bristol, SECONN | FLORIDA – Hillsborough, Lake, Lee, Pasco, Palm Beach 1, Palm Beach 2, Pinellas | HAWAII – H-POWER | INDIANA – Indianapolis | MARYLAND – Montgomery | MASSACHUSETTS – Haverhill, SEMASS | NEW JERSEY – Camden, Union, Essex | NEW YORK – Babylon, Hempstead, Huntington, MacArthur, Niagara Falls, Onondaga | OREGON – Marion | OKLAHOMA – Tulsa | PENNSYLVANIA – Delaware Valley, Plymouth, Harrisburg, Lancaster, York, Fairless Hills (Metals Recycling), Myerstown (Environmental Solutions), ECOvanta (Environmental Solutions) | VIRGINIA – Alexandria/Arlington, Fairfax
Resulted In:
$13,140,534
Customer Savings
2,100+
Downtime Hours Saved
1,653+
Sensors Deployed
Case Studies
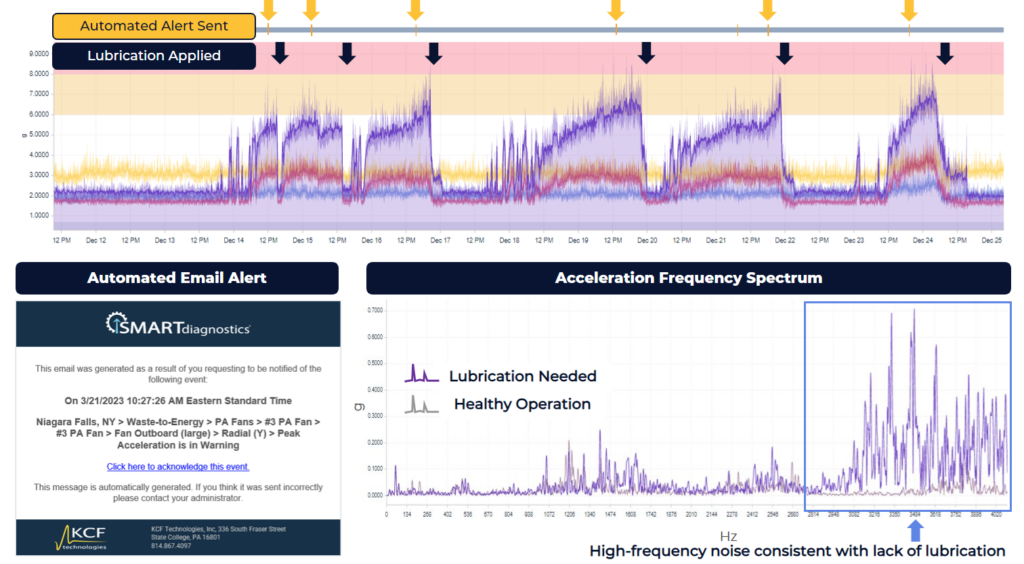
When the Boiler Draft System Gave a Hint
Boiler Draft System – Lubrication Troubles
Fault Type: Lubrication
Indication:
High-frequency noise, resolved with grease application.
Automated notifications set for vibration threshold breaches.
Action Taken: CBM Lubrication program initiated for continued operation.
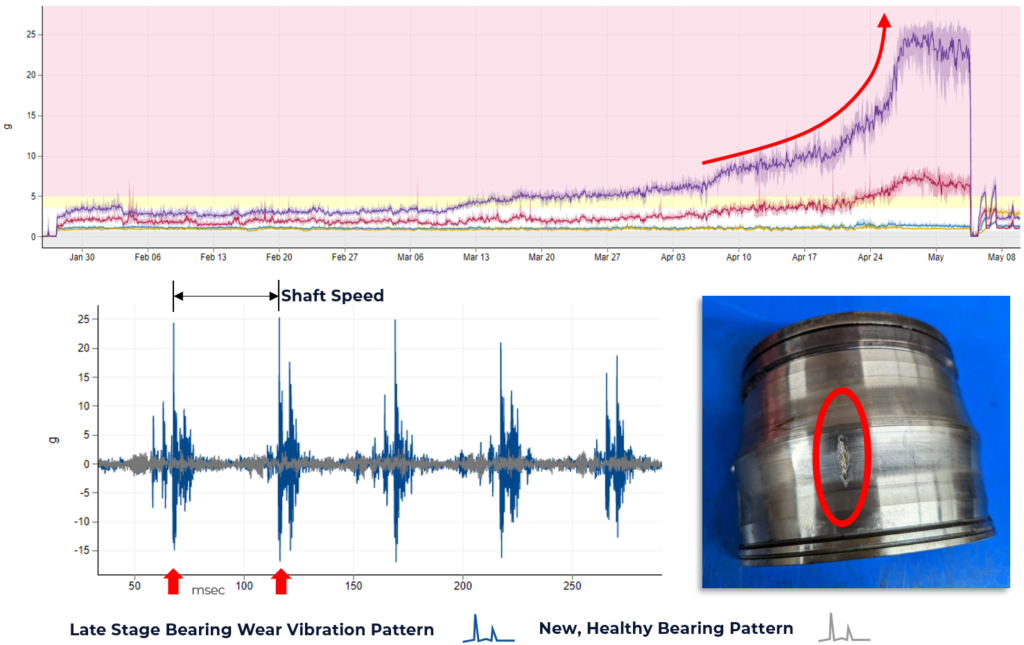
A Showdown with a Bearing Problem
Boiler Draft System – Averting Bearing Disaster
Fault Type: Stage 4 Bearing Fault
Indication:
Acceleration uptrend over two weeks.
Bearing fault frequencies evident in the time-waveform.
Action Taken: Bearing replacement, preventing major downtime.
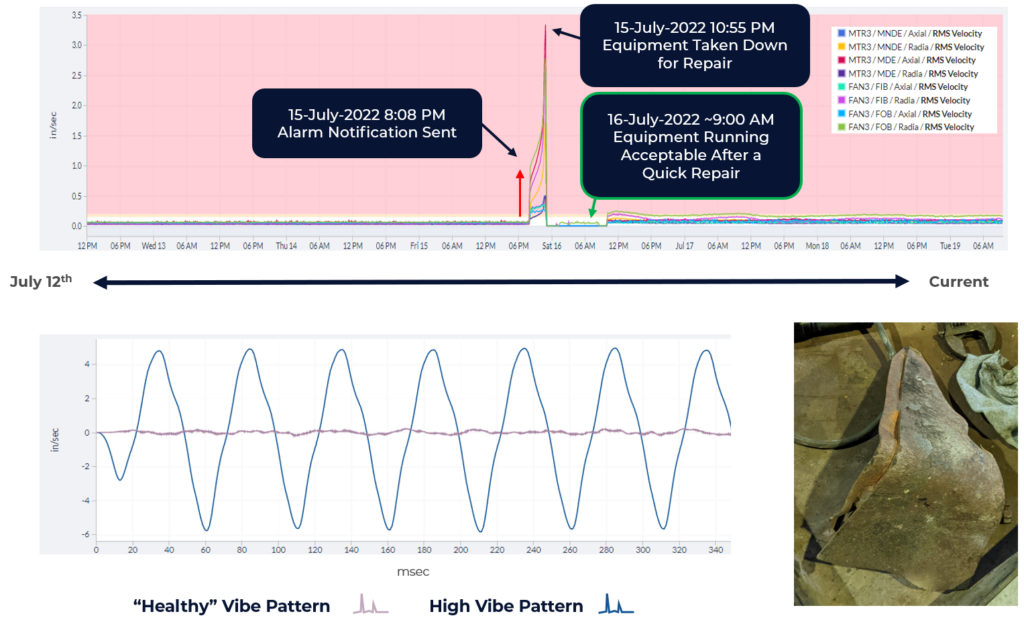
Finding the Right Balance with Air Fans
Primary Air Fans – Balancing Act
Fault Type: Severe Imbalance
Indication:
Spike in RMS Velocity vibration at multiple points.
Elevated running speed frequency in the time-waveform.
Action Taken: Immediate action plan, bearings replaced, rebalanced, and monitored.
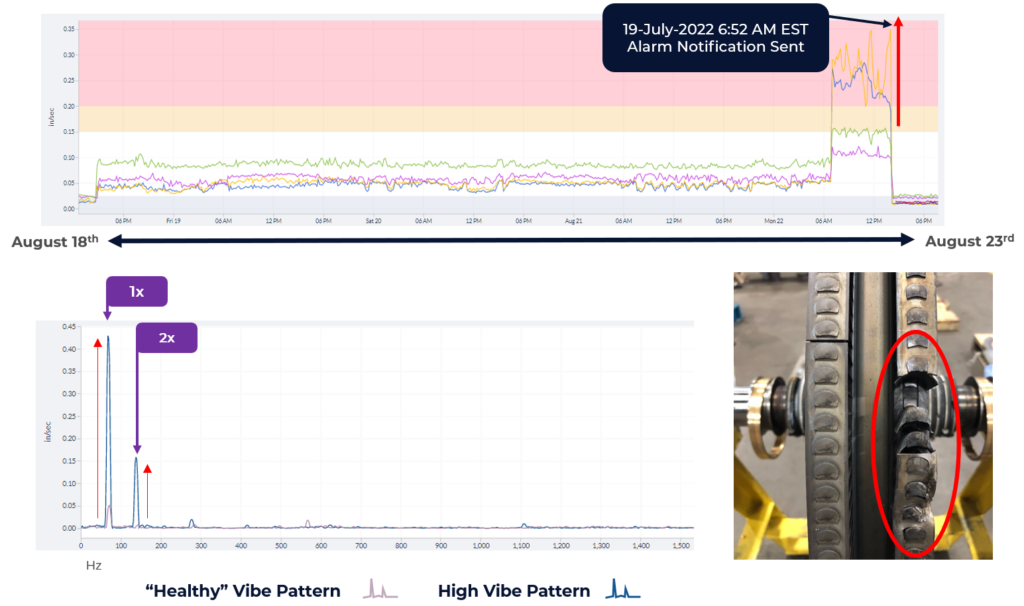
Tackling Issues with Water Pumps
Boiler Feed Water Pumps – Precision Matters
Fault Type: Imbalance (Damaged Vanes)
Indication:
RMS Velocity vibration increase.
Elevated running speed frequency and 2x harmonic.
Action Taken: Redundant system activated, turbine rebuilt, isolated damage.
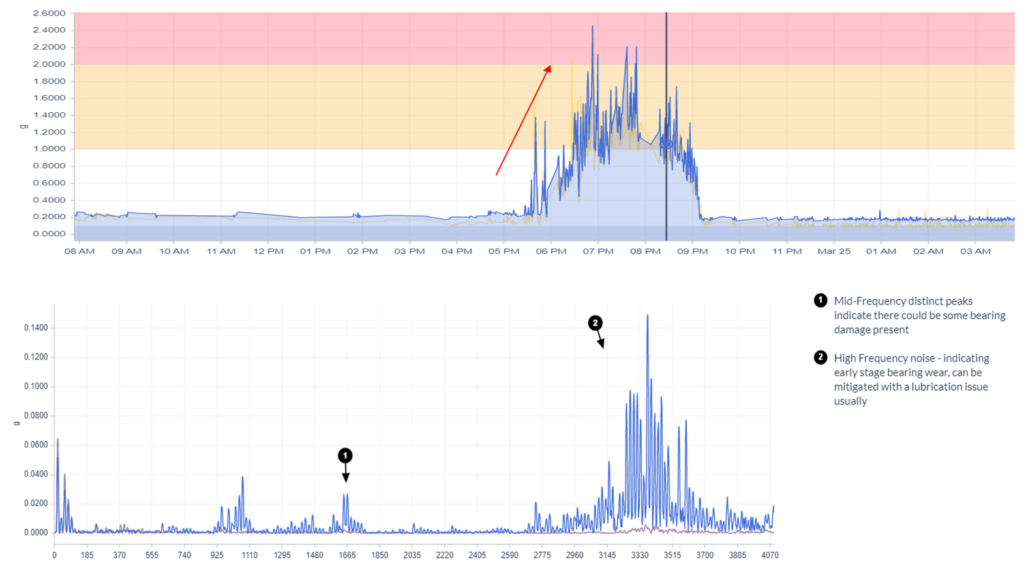
Navigating Issues with Fan Bearings
Induced Draft Fans – Lubrication Struggles
Fault Type: Bearing Fault – Lubrication Issue
Indication:
Alert emails triggered by predetermined thresholds.
Abnormal bearing wear patterns.
Action Taken: Bearing oil replenished to address lubrication issue.
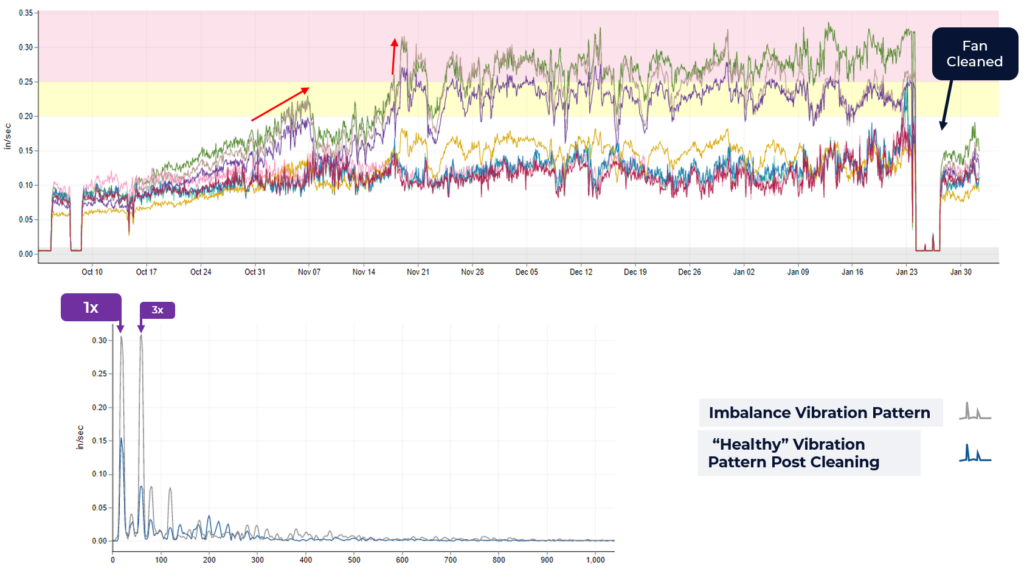
Calming Down an Unbalanced Fan
Boiler Draft System – Imbalance Woes
Fault Type: Fan Imbalance (Buildup)
Indication:
Gradual rise in overall vibration.
Elevated 1x & harmonics, axial direction.
Action Taken: Fan cleaned during planned outage.
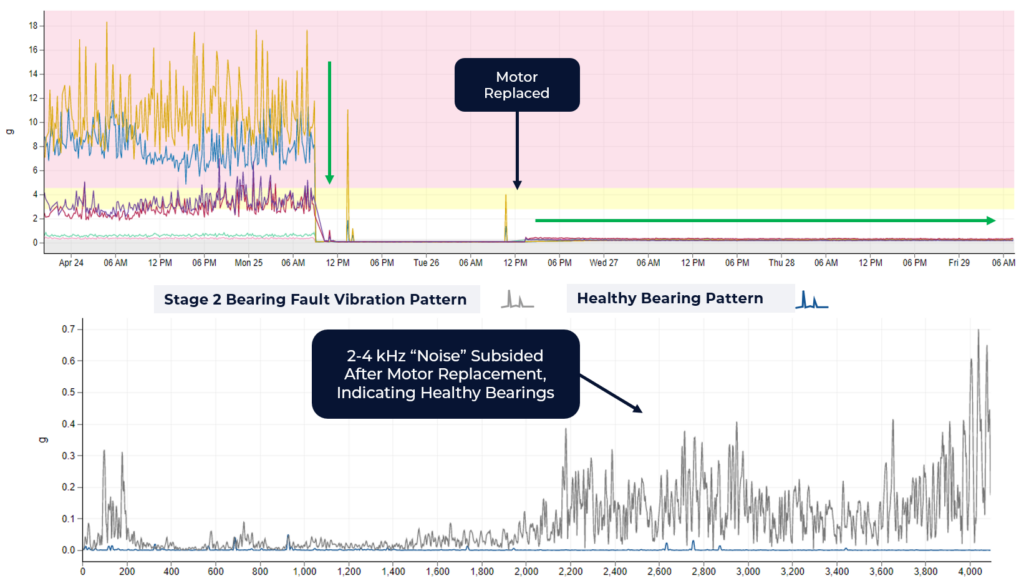
Mastering Cooling Towers’ Challenges
Cooling Towers – Addressing Bearing Degradation
Fault Type: Stage 2 Bearing Fault
Indication:
Outlying vibration compared to similar motor.
Raised noise floor between 2-4 kHz.
Action Taken: Motor replacement, new vibration standard.
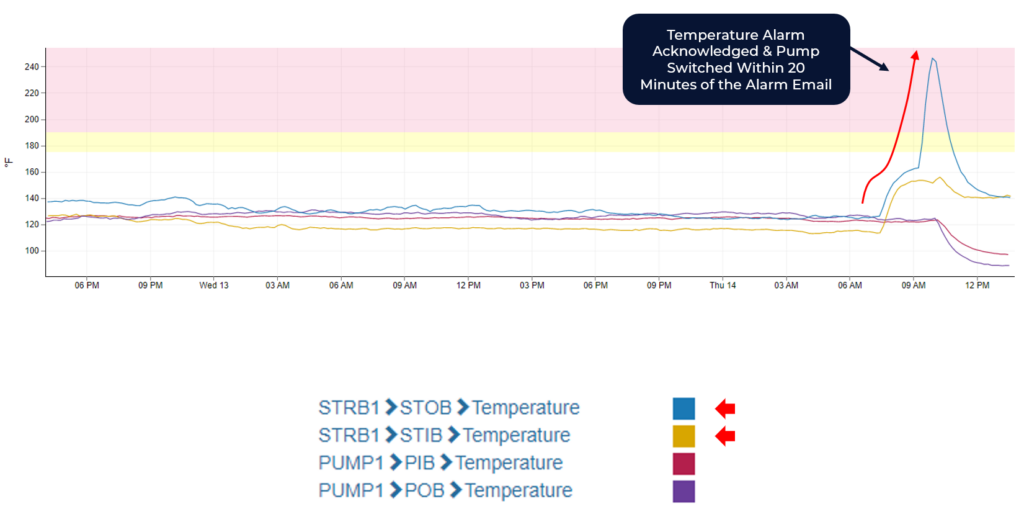
The Adventure of the Pump’s Lubrication
Boiler Feedwater System – Lubrication Snag
Fault Type: Lack of Lubrication (Lube Oil Pump Failure)
Indication:
Sudden temperature increase at turbine bearing.
Action Taken: Pump switch to avoid downtime, lube oil pump repaired.
Reworlds’s Journey Towards Zero Fan Failures
Reworld has embarked on an impressive mission to achieve zero fan failures within its operations. This ambitious goal has led to the implementation of wireless vibration monitoring across all of its waste-to-energy facilities, totaling 39 sites. In this reflection paper, we will explore Reworld’s proactive approach, the benefits of wireless vibration monitoring, and the potential impact of this initiative on the company’s operations and environmental sustainability efforts.
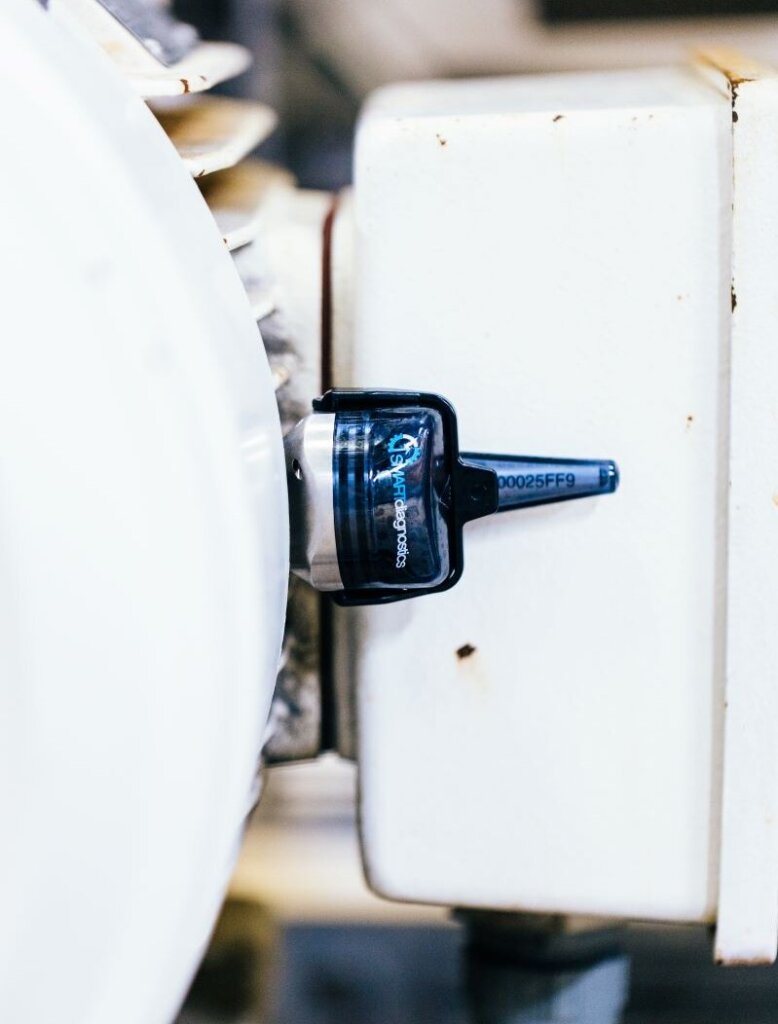
PROACTIVE APPROACH
Reworld’s decision to invest in wireless vibration monitoring represents a proactive step towards addressing fan failures. By embracing cutting-edge technology and applying it to their operations, Reworld has demonstrated a commitment to optimizing performance, reducing downtime, and enhancing operational efficiency. This proactive mindset aligns with the principles of continuous improvement and positions Reworld as a leader in the WtE industry.
WIRELESS VIBRATION MONITORING
The deployment of wireless vibration monitoring on Reworld’s assets holds immense potential for the company’s reliability and maintenance practices. By continuously monitoring the vibration levels of fans, Reworld gains real-time insights into the condition and performance of these critical components. Early detection of anomalies or deviations from normal operating conditions allows for proactive maintenance interventions, preventing potential failures and costly downtime.
Moreover, wireless vibration monitoring enables Reworld to collect and analyze large volumes of data across its entire fleet of waste-to-energy facilities. By leveraging data-driven insights, Reworld can identify patterns, trends, and correlations, enabling predictive maintenance strategies and optimized asset management. This proactive maintenance approach helps extend the lifespan of fans, reduce maintenance costs, and minimize the environmental impact associated with unplanned downtime.
IMPLICATIONS AND ENVIRONMENTAL SUSTAINABILITY
Achieving zero fan failures through wireless vibration monitoring aligns with Reworld’s broader environmental sustainability efforts. By minimizing downtime, Reworld ensures a consistent and reliable operation of its waste-to-energy plants, maximizing the energy recovery from waste materials. This translates into reduced reliance on traditional fossil fuel sources, decreased greenhouse gas emissions, and a more sustainable energy generation process.
Additionally, the implementation of wireless vibration monitoring reflects Reworld’s commitment to continuous improvement and operational excellence. By leveraging technology and data analytics, Reworld can optimize the efficiency and effectiveness of its waste-to-energy facilities, ultimately contributing to a cleaner environment and a more sustainable future.
Reworld’s adoption of wireless vibration monitoring as a means to achieve zero fan failures is a testament to their commitment to innovation, reliability, and environmental sustainability. This proactive approach, implemented across all of their waste-to-energy facilities, allows Reworld to gain real-time insights into the health and performance of critical assets. By leveraging these insights and embracing data-driven decision-making, Reworld can optimize its maintenance practices, extend the lifespan of its fans, and minimize downtime.
Furthermore, Reworld’s initiative aligns with their broader environmental sustainability goals. By maximizing energy recovery from waste and reducing reliance on fossil fuels, Reworld’s wireless vibration monitoring contributes to a cleaner and more sustainable energy generation process.
As Reworld continues to refine and expand its monitoring capabilities, the company sets an example for the waste management and energy industries, demonstrating the potential of technological advancements in achieving operational excellence and environmental stewardship.
Advanced Solutions
Asset Class Monitoring Strategies
CLICK on tables below to enlarge image and view full data.
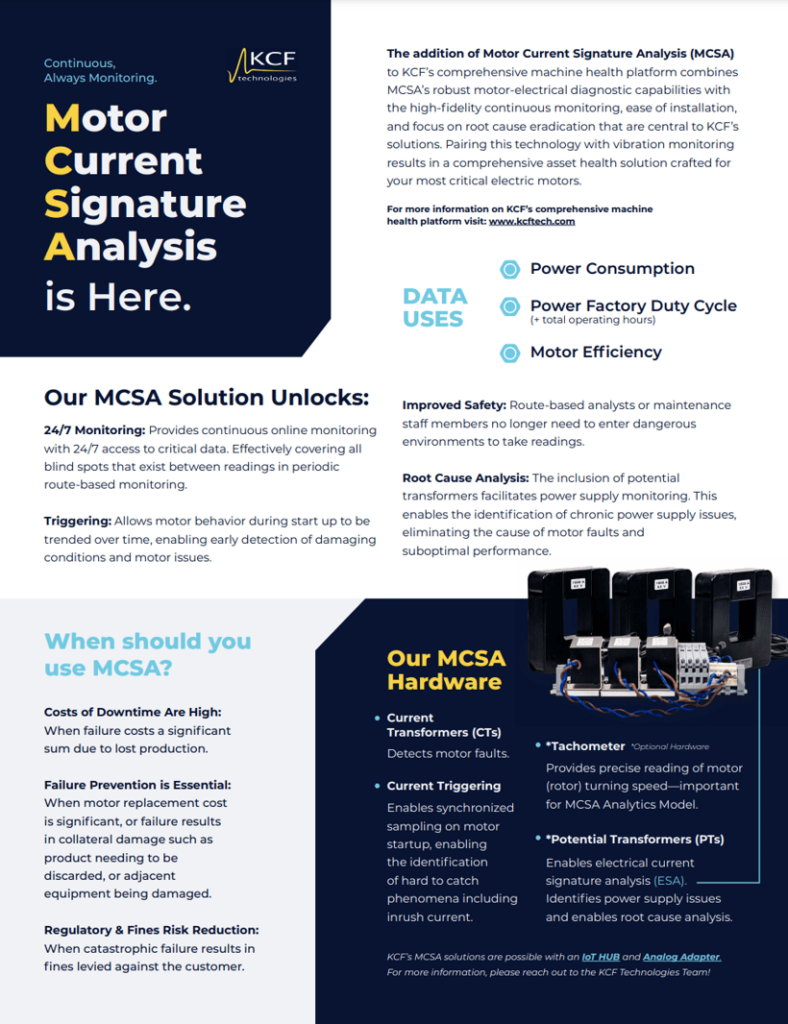
MOTOR CURRENT SIGNATURE ANALYSIS (MCSA)
The addition of Motor Current Signature Analysis (MCSA) to KCF’s comprehensive machine health platform combines MCSA’s robust motor-electrical diagnostic capabilities with the high-fidelity continuous monitoring, ease of installation, and focus on root cause eradication that is central to KCF’s solutions—pairing this technology with vibration monitoring results in a comprehensive asset health solution crafted for your most critical electric motors.
Rookie of the Year
This award goes to a customer or individual who recognizes the opportunity to go fast and scale quickly while bringing a large amount of value to their organization.
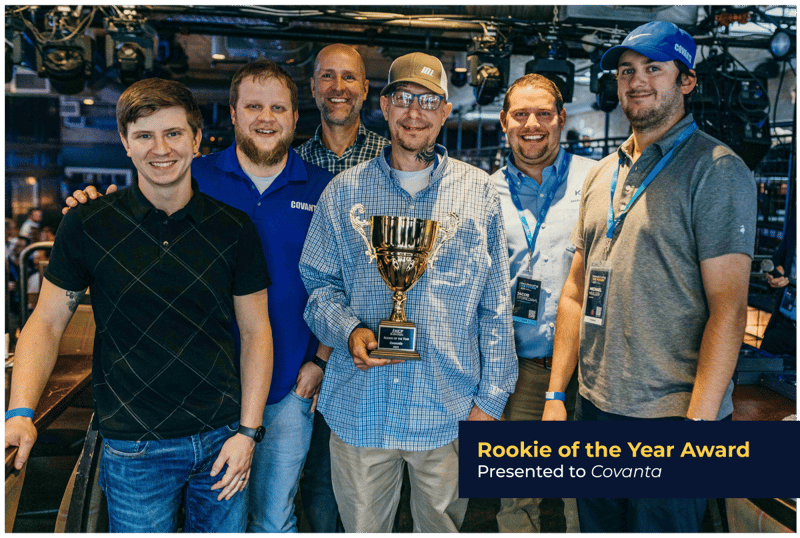
With the reorganization of the company and the focus on reliability and availability within our facilities, KCF Technologies was able to detect and mediate over 40 instances that otherwise had a high probability of causing expensive downtime. With the use of their system, we now have the ability to plan out and properly schedule downtime to save us on lost revenue. Whether evaluating downtime hours avoided or dollars saved, our team and KCF’s joint efforts have made a strong impact in 2022. In 2023, as we expand KCF’s technology to 15 new Reworld locations, we look forward to growing our downtime avoidance.
Eric Way
MAINTENANCE MECHANIC AT REWORLD
KCF Full Guide
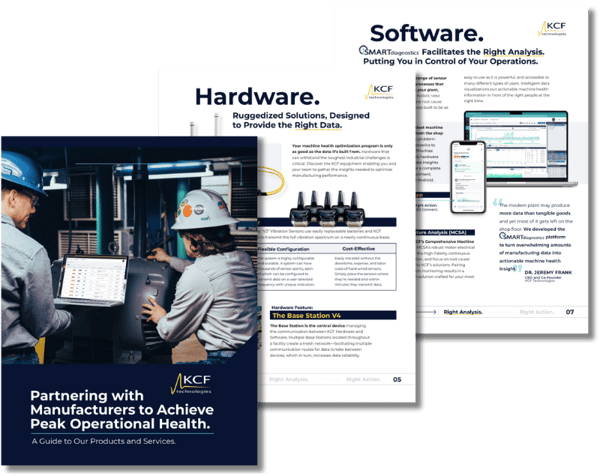
Learn more about gaining a competitive edge with the most advanced, comprehensive machine health optimization platform.