What is Overall Equipment Effectiveness?
Overall Equipment Effectiveness (OEE) is a key performance indicator that lets manufacturers easily assess their operational efficiency. OEE measures the percentage of time a given machine is operating at its peak. Successful manufacturing leaders monitor OEE closely to identify performance issues at the asset level, since the reduced performance of just one machine can lead to plant-wide problems.
Best-in-class manufacturers (roughly the top 25%) enjoy OEE of >80%. The average manufacturer (representing half of all manufacturers) has OEE of approximately 66%.
How to Calculate Overall Equipment Effectiveness
There are three asset metrics that must be known to accurately calculate OEE:
- Availability (A)
- Performance (P)
- Quality (Q)
As an example, if your machine is running 87% of the time (A), is running at 82% of its potential speed (P), and produces a usable product 98% of the time (Q), your calculation would look like this:
0.87 x 0.82 x 0.98 = 0.699
In this example, your asset has an OEE of approximately 70%.
To determine the values for A, P, and Q, first choose a window of planned production time, expressed in hours. The longer the window of time, the more accurately your OEE figure will represent the average performance of the asset.
The formula for calculating OEE is A x P x Q = OEE.
How to Calculate Availability for OEE
Availability is your asset’s total uptime during planned production times. Availability can be calculated by subtracting both planned and unplanned downtime from your total planned production time to determine your actual uptime, and then dividing that number by your planned production time.
To determine actual uptime, planned downtime is subtracted from planned production time (along with unplanned downtime) because while it can’t be totally avoided, in many cases it can be significantly reduced.
(Planned Production Time – Planned Downtime – Unplanned Downtime) ÷ Planned Production Time = Availability (A)
How to Calculate Performance for OEE
Your production performance rate is a measure of your machine’s actual throughput compared to its maximum possible throughput. As an example, imagine your asset has an ideal cycle time of five seconds per unit, and should theoretically be able to produce 720 units per hour. If that asset only produces 680 units in an hour due to slow cycles, jams, or small stops, then its production performance rate for that hour is 94%.
Actual Throughput ÷ Maximum Possible Throughput = Performance (P)
How to Calculate Quality for OEE
Quality measures the number of produced units that are up to spec versus the number of lost units, e.g. scrap or rework. Quality is determined by dividing the number of usable units by the total number of produced units within your chosen time frame.
(Total Units Produced – Lost Units) ÷ Total Units Produced = Quality (Q)
What Causes Poor Overall Equipment Effectiveness?
It’s clear that equipment failure is a big driver of OEE loss, and often manufacturers who are struggling with poor OEE may not know why their equipment has failed. A lack of visibility into the health of their assets and limited time, resources, and knowledge around optimizing machine health can be large contributors to below-average OEE.
On average, roughly 80% of OEE losses are driven by unplanned downtime, and 40% of unplanned downtime costs is related to equipment failure.
The top 25% of manufacturers report that only 0.5% of downtime reasons are unknown, while the bottom 25% report that over 15% of their downtime is due to unknown reasons. This represents a knowledge gap of over 30X.
Strategies for Improving Overall Equipment Effectiveness
The confluence of powerful new technologies—big data, advanced analytics, cloud computing, and IoT—represent an opportunity to rapidly improve operational efficiency. Manufacturers have access to greater levels of automation and better decision-making intelligence than ever before. With these tools, manufacturers can gain:
Comprehensive visibility into what is happening in your plant(s)
- Machine behavior
- Factors that cause OEE loss, including process changes, operator behavior, maintenance errors, and premature equipment wear
- Fault detection, diagnostics, prognostics (forecasting), and advanced alarming
Tools to practically and efficiently improve operations
- Fix the right things at the right time
- Adjust production more quickly and with less waste
- Become more efficient using digital workflows
- Make the right investments at the right time
Comprehensive machine and plant health data is key to developing an OEE improvement strategy. For example, if you focus on significantly improving Performance only to learn that your gains come at the expense of Quality, your OEE may end up lower than when you started your improvement efforts. Additionally, OEE is far from the only measure of success for the typical manufacturer, and short-term OEE gains could lead to other long-term issues like decrease in mean time between failure or decreased worker safety.
Knowing where the real opportunities are to improve asset and plant performance requires a 360-degree view of your operations enabled by smart machine health monitoring technology.
Moving Beyond Overall Equipment Effectiveness to Machine Health Optimization
OEE is an important KPI, but it’s just one measure of your plant’s overall health. An optimization-focused approach to operational efficiency has to consider factors beyond Availability, Performance, and Quality.
80% of failure-related downtime is driven by maintenance and operations actions, meaning machine health represents the largest short- and long-term opportunity to improve overall operational KPIs based on total business impact, practical need, and addressability. Because machine health is so intertwined with other operational factors, it is fundamental to enabling improvement in production flexibility, product quality, rate, and safety.
OEE can help you achieve your best manufacturing performance under your current conditions. Machine health optimization can show you how to improve your plant conditions to unlock your highest performance potential.
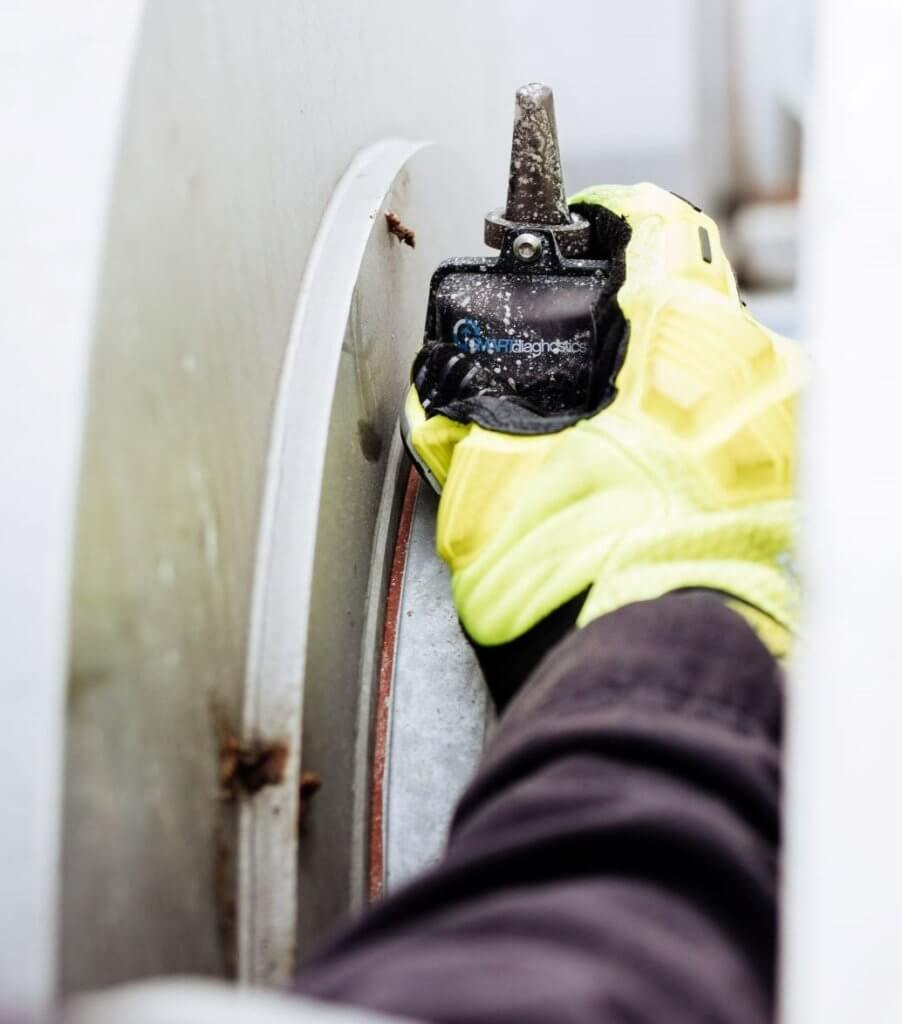
Contact Us
The journey to true machine health starts with a conversation. Contact us today to learn more about eliminating the root cause of your asset failures.