What is Predictive Maintenance?
Predictive maintenance uses data collected about your industrial assets combined with predictive analytics to estimate when a machine will fail so that measures can be taken to avoid downtime.
Using a variety of hardware and software solutions—including vibration monitoring—early faults can be detected to alert maintenance leads before a catastrophic failure occurs. All data collected for predictive maintenance purposes must be preprocessed and analyzed in order to be useful.
When a predictive maintenance program is properly implemented, manufacturers can take significant steps toward optimizing their plant resources and increasing OEE.
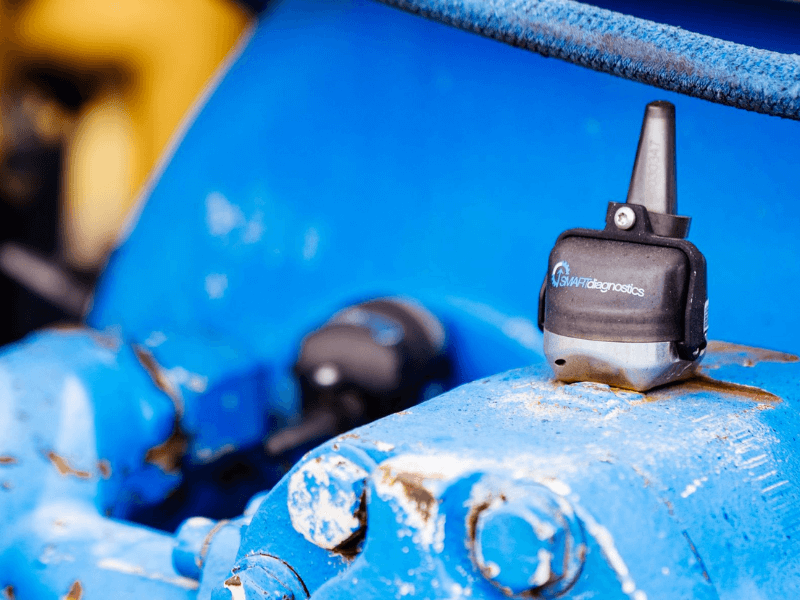
Predictive Maintenance vs. Preventive Maintenance
Unlike predictive maintenance, preventive maintenance doesn’t rely on collected data about the real-time condition of the asset. Instead, machines are maintained and inspected at regular intervals. This approach depends on the ability of the inspector to identify machine health issues—often, small problems don’t become evident until they are large problems.
The goal of preventive maintenance is to prevent machine failure and avoid reactive maintenance. Actual results vary based on how closely the maintenance team is able to stick to the schedule and how good they are at identifying problems before machine failure is imminent.
Predictive Maintenance vs. Condition Monitoring
The definition of condition monitoring has evolved since this practice was first widely implemented. Initially, condition monitoring alerts meant that a failure was already occurring and needed to be addressed immediately. Today, it means observing the overall condition of your assets via route-based or continuous monitoring, helping you prioritize and optimize your limited maintenance resources.
As technology and techniques advanced, predictive maintenance programs were able to make use of condition monitoring to help forecast machine failure and reallocate maintenance resources to that asset. Condition monitoring is just one necessary component of a larger predictive maintenance program.
Pitfalls of Predictive Maintenance
One of the biggest barriers to predictive maintenance is the time and effort required to design and implement the program. Lots of manufacturers have tried investing in condition monitoring technology and attempting to interpret the data themselves, only to end up with annoying over-alarming issues that they have to solve and a lack of actionable information.
Maintenance personnel and operators also have to be trained on using the equipment and interpreting data, which can take significant time and resources. Without training, however, data may be collected incorrectly or misinterpreted, leading already time-strapped teams to perform unnecessary maintenance tasks while more critical issues get overlooked.
How the Industrial Internet of Things (IIoT) Enables Predictive Maintenance
A predictive maintenance program is only as good as the data fuelling it. Condition monitoring technology has evolved significantly in recent years, meaning that monitoring hardware is cheaper, easier to use, and more accurate. Real-time monitoring is made possible with wireless sensors and sensor nodes that can monitor vibration, pressure, oil quality, ultrasonic frequencies, and more on both intermittent and continuously operating assets.
The information that this hardware collects isn’t actionable in its raw form; an analysis platform for predictive maintenance is also needed to clean and contextualize condition monitoring data, provide connectivity, and guide users in the right direction for optimal maintenance resource allocation.
With integrated IIoT technology, manufacturing leaders can now take advantage of user-friendly end-to-end predictive maintenance solutions that can be customized to their plant’s specific applications.
Moving Beyond Predictive Maintenance to Machine Health Optimization
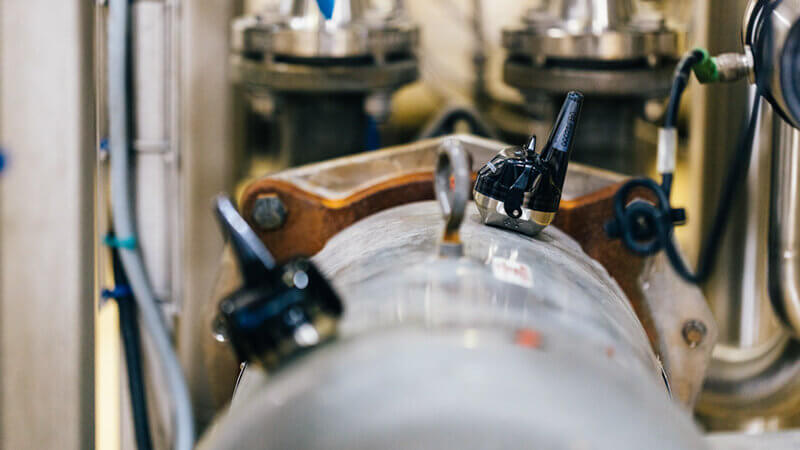
A successful predictive maintenance program can help manufacturers avoid costly unplanned downtime by assessing and projecting asset health. This will contribute to the overall optimization of your plant, but fails to address the root of machine health issues.
An optimization-focused approach to machine health goes beyond basic diagnostics and alarming. Predictive maintenance will tell you when a machine is likely to need repair; machine health optimization will diagnose the damaging conditions and eliminate them. With the right asset intelligence and analytics at your disposal, you can solve asset problems permanently.
A successful predictive maintenance program can help manufacturers avoid costly unplanned downtime by assessing and projecting asset health. This will contribute to the overall optimization of your plant, but fails to address the root of machine health issues.
Contact Us
The journey to true machine health starts with a conversation. Contact us today to learn more about eliminating the root cause of your asset failures.