Watch to learn how predictive maintenance is transforming the glass manufacturing industry.
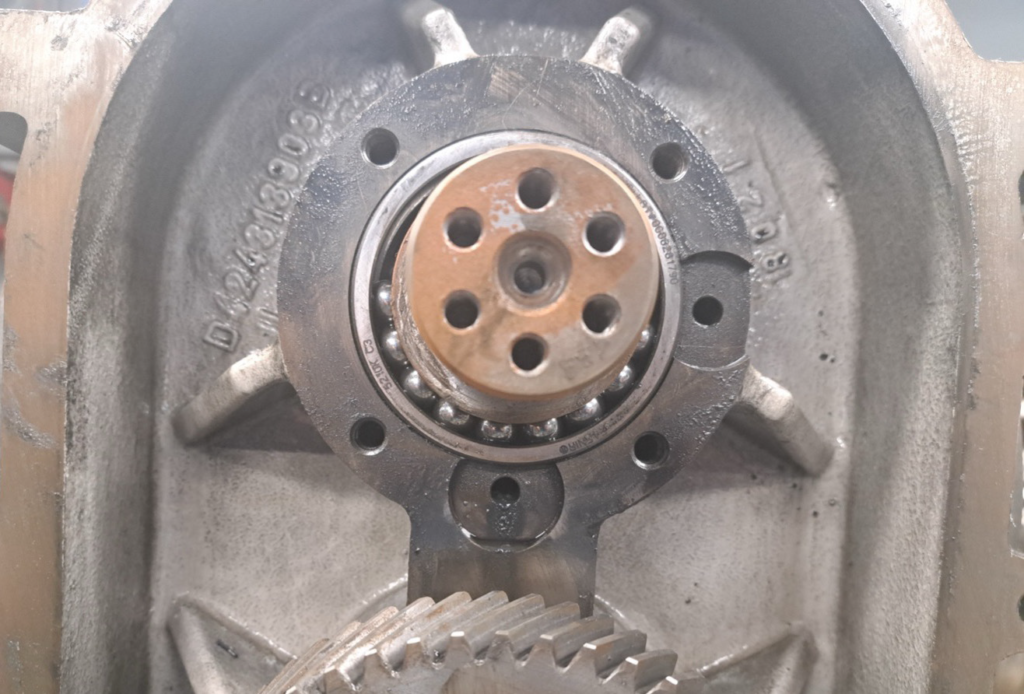
Vacuum Pumps
Vacuum pumps are critical in many manufacturing processes. KCF's comprehensive machine health monitoring empowers you with the data and insights needed to minimizing unplanned downtime.