The Challenge
The wastewater industry is more than just a service; it’s the backbone of healthy communities, ensuring that waste management is not only reliable but also efficient. When equipment malfunctions or is not operating at its best, the impact reverberates throughout the community, affecting something as essential as clean water. This reality underscores the importance of continuous real-time monitoring in this sector.
On December 13th, a significant spike in peak acceleration and velocity readings at Altoona Water Authority, a public wastewater facility in Altoona, PA, caught the attention of SMARTdiagnostics. Thanks to the rapid response from SENTRYsolutions, plant operators were prompted to inspect the dryer motor and potentially grease the inboard bearing.
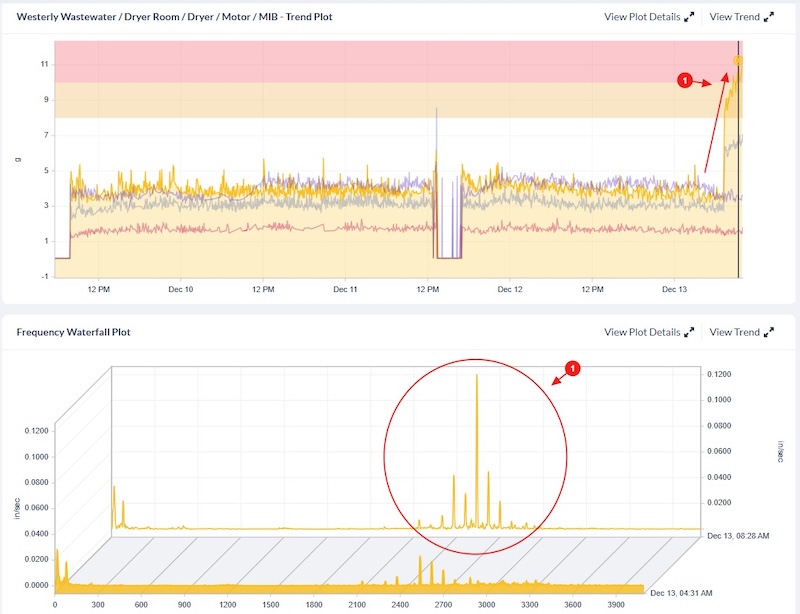
At this time, a KCF analyst sought to determine when the asset had last been greased. While Motor In-Board (MIB) readings were still increasing, the Motor Out-Board (MOB) trends showed a drop in the trend lines. The plant confirmed that before the greasing on the 13th, the last greasing had occurred six months ago, performed according to OEM recommendations.
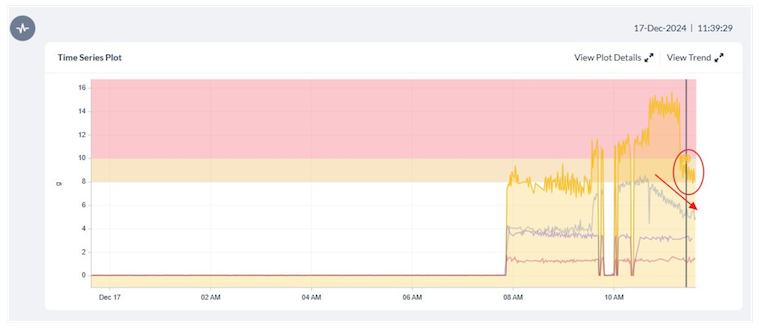
To get to the bottom of the issue, KCF proposed a test to monitor the motor’s performance. On December 16th, the motor was run unloaded for an hour, revealing a concerning amount of excess grease in the motor bearings. Conversations with site mechanics revealed the root cause: staff had been mistakenly removing the case vent plug instead of the grease drain plug during maintenance. This simple oversight led to significant over-greasing of the inboard bearing, jeopardizing the health of the equipment.
After talking to the mechanics, we found out they were removing the wrong plug on the motor when greasing. They removed the case vent plug on the bottom of the motor, not the grease drain on the bearing housing.
Altoona Water Authority Employee
The Resolution
After the team removed the excess grease, the levels gradually returned to normal. Without the proactive real-time monitoring capabilities of SMARTdiagnostics, it’s likely that the issue would have gone unnoticed until a complete bearing failure occurred—resulting in the need for a new motor. With an estimated lead time of 8–10 weeks for a replacement, this proactive intervention saved the plant $14,904 in the first 30 days of $199 pilot. Beyond just financial savings, the prevention of such failures also avoided any plant downtime, as well as up to two weeks of dryer cleanout, keeping employees out of confined spaces and assuring a safer work environment.
Thanks to vigilant real-time monitoring and immediate action, the plant not only protected its operations and its people, and saved significant costs, but also ensured that essential services continued to flow to the community. This incident serves as a powerful reminder of how crucial it is to remain diligent in the wastewater industry, safeguarding both equipment and community well-being.
Additional Motor Faults Covered
Bearing Fault | Electrical Short | Phase Loss | Rotating Looseness | Rotar Bar | Soft Foot | Stator Bar
KCF Full Guide
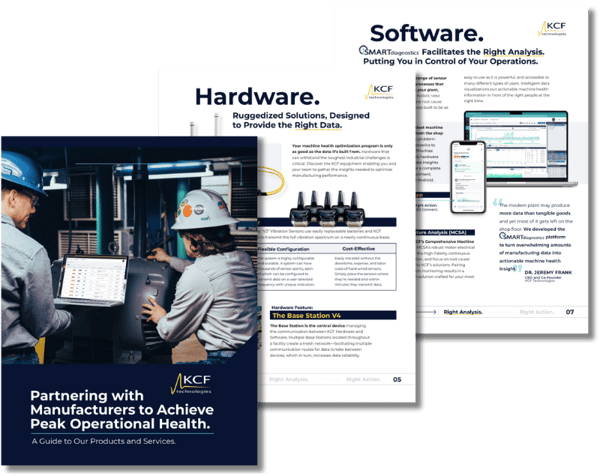
Learn more about gaining a competitive edge with the most advanced, comprehensive machine health optimization platform.