Stamping Press Crown
The cost of automotive downtime related to the stamping press crown can vary depending on several factors, including the size of the operation, the specific application, and the severity of the downtime. However, generally, it is accepted that downtime in the automotive industry can be very costly.
The costs associated with downtime related to the stamping press crown may include:
– Lost Production
– Scrap and Rework
– Equipment Repair Or Replacement Costs
– Overtime and Additional Labor Costs
These costs can add up quickly, making it critical to take preventive measures to avoid downtime related to stamping press crown failure. Regular maintenance and inspections, in addition to predictive maintenance tools such as continuous vibration monitoring, can help minimize the risk of downtime and associated costs.
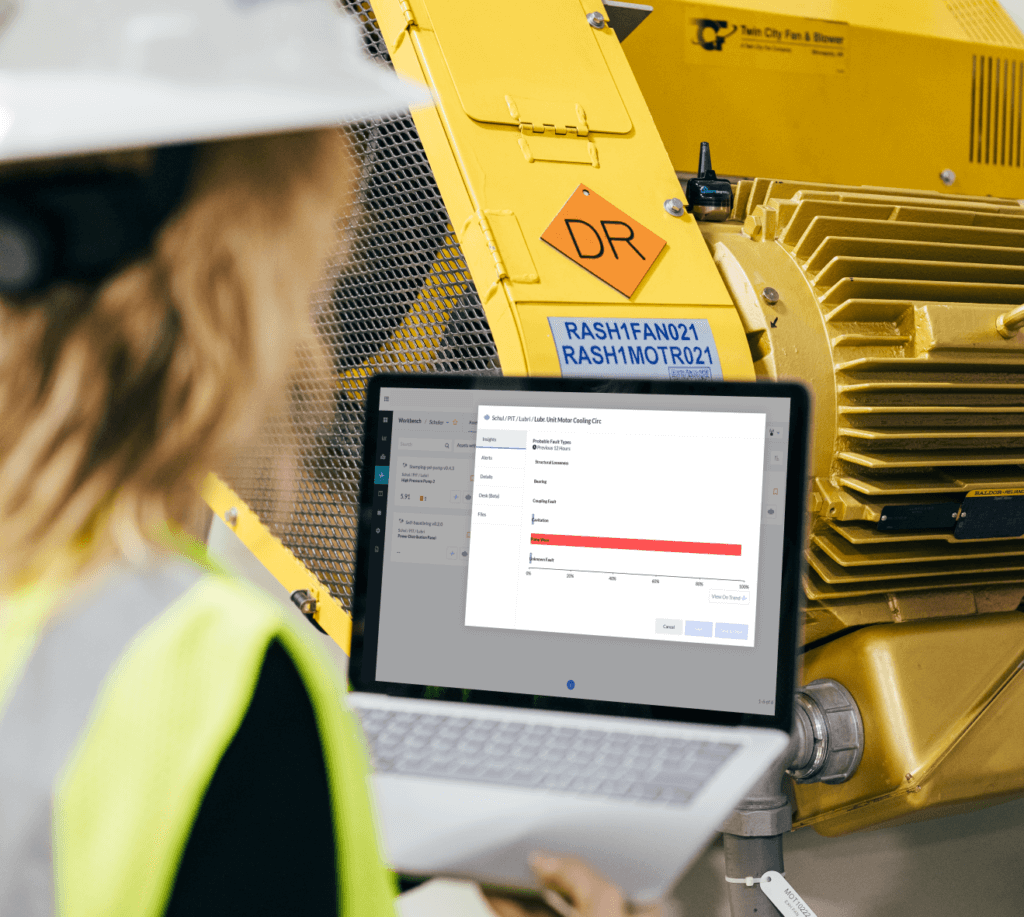
Asset Blind Spots
Challenge 1:
Due to the enclosed and remote nature of the crown, developing faults will not easily be visually or audibly noticed.
Challenge 2:
Most sites currently have no monitoring in place or at best have a monthly or quarterly route. This monitoring schedule not only results in large blind spots but also only captures a narrow range of potential operating conditions across all dies.
Challenge 3:
Without a continuous monitoring solution in place, accurately and reliably gauging and trending the health status of the press crown is not feasible.
Failure of the Stamping Press Crown can cause significant production downtime and can be expensive to repair. There are several common failure modes that occur in stamping press crowns in automotive applications that can be avoided, prevented, or handled before catastrophic failure.
Here are a few of the major failure modes that KCF’s Full Machine Health Platform and remote monitoring system can detect:
Wear and Deformation: The crown wears over time due to continuous contact with metal sheets. This wear can cause deformation of the crown, leading to poor stamping quality and reduced production efficiency.
Misalignment: Misalignment of the crown can occur due to improper installation or use. This can cause uneven wear and deformation, as well as reduced production efficiency.
To prevent these failure modes, KCF Technologies’ 24/7 monitoring software, SMARTdiagnostics, provides real-time data for earlier detection. One key element of KCF Technologies’ machine health platform is continuous vibration monitoring. Vibration monitoring can be a useful tool for detecting and preventing the failure modes of stamping press crowns mentioned earlier.
3 Ways In Which Vibration Monitoring Can Help
Detection of Wear and Deformation
Changes in vibration patterns can also indicate wear and other issues with the crown. By monitoring vibration patterns, maintenance personnel can detect these changes and take corrective action, such as adjusting the press settings or replacing the crown.
Wear and Tear/Defects of the Machine
Vibration monitoring can be used to detect improper maintenance. Maintenance personnel can see the impact of work performed both pre and post completion, ensuring work is completed correctly every time work is done.
Alignment Monitoring
Vibration monitoring can also be used to monitor the alignment of the press components, including the crown. Misalignment can cause uneven wear and deformation, which can lead to reduced production efficiency and increased maintenance costs. By monitoring the vibration patterns, maintenance personnel can detect misalignment early and take corrective action.
Vibration monitoring can provide early detection of the failure modes of stamping press crowns, which can help prevent catastrophic failures and reduce downtime and maintenance costs.
Through partnerships with four of the top five automotive manufacturers, KCF Technologies has identified a press crown failure can cost approximately $800,000/hour. By using KCF Technologies’ predictive machine health platform, SMARTdiagnostics, manufacturers have saved as much as $3M on just a single catastrophic press crown failure.
Optimize Your Machine Health
Reduce unplanned downtime by getting to the root cause of machine failures. Learn how KCF’s machine health optimization platform will help you achieve peak plant performance. Download the KCF Guide to learn more about optimizing your machine health.