Use machine health offering from RigCLOUD® and KCF Technologies (“KCF”) to proactively predict equipment maintenance on drilling rigs, minimize equipment damage and avoid downtime.
OBJECTIVE
Trial Overview
4 rigs in South & West Texas
96 sensors
12 mud pumps
5 months
Sensors were installed to monitor mud pump vibrations. Artificial Intelligence (AI) and certified subject matter experts from the Rigline 24/7 center in Houston remotely analyzed the data to identify potential issues. Recommended actions were communicated to the rig manager. Feedback was incorporated back into the system for continuous improvement.
Results
Nabors avoided $320,000 in equipment costs, and downtime, during the pilot.
Highlights: Mitigating Power End Failures
KCF sensors detected abnormal power end vibrations from a mud pump. Upon inspection, the external oiler was not discharging oil over the power end or crossheads. Proactive adjustments were made, avoiding a potential failure with an estimated cost of $160,000 plus downtime.
KCF sensors detected high vibrations on a mud pump, upon inspection, the lube oil level was low. The crew promptly added oil, improving lubrication and lowering the vibrations. The proactive maintenance avoided a potential power end failure, resulting in a cost avoidance of $160,000.
THE SMARTsensing PRODUCT CATALOG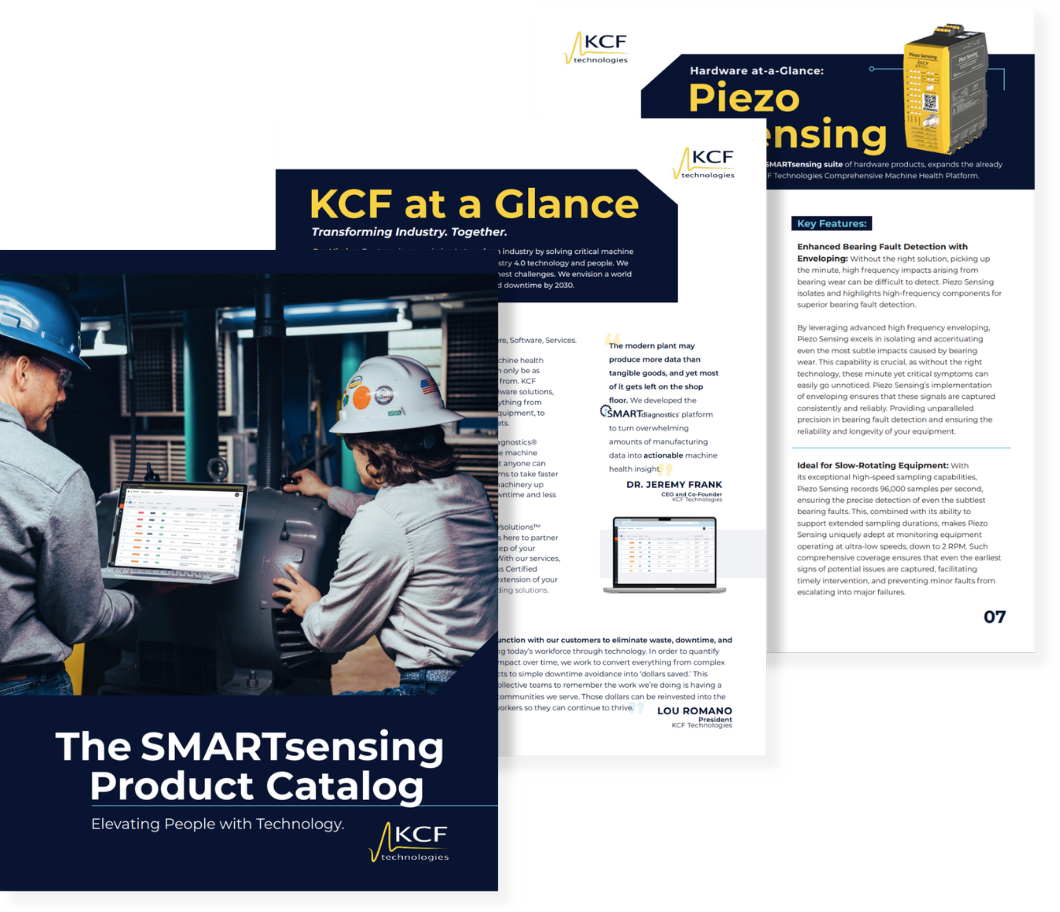
Your machine health optimization program can only be as
good as the data it’s built from. KCF provides ruggedized hardware solutions, designed to monitor everything from the most basic rotating equipment, to complex intermittent assets.
You can learn more about our Hardware Solutions in the SMARTsensing Product Catalog.