How to optimize the health of intermittent and complex industrial equipment: IoT HUB Triggering
February 21, 2024 | Machine Health Solutions
Vibration monitoring for standard industrial rotating equipment is anything but new. The first accelerometer that was commercialized was created in 1924, with the piezoelectric accelerometer coming to the market shortly after, bringing a new level of accuracy to the developing field of vibration monitoring.
Today, MEMS accelerometers are the standard in monitoring standard rotating equipment like fans, pumps, and motors. However, the quality of data transmitted by these sensors varies dramatically company to company, meaning possible use cases may not be accessible when using certain vibration sensors. Even with the ability to monitor these common assets, a problem still existed – monitoring intermittent equipment, like robots, cranes, and conveyors, equipment increasingly being used in manufacturing and industrial environments. The difficulty comes down to the nature of real time monitoring.
Real time monitoring captures a continuous stream of data (again, varying company to company how often this data collection occurs). This mean collection can occur during times of operations when collection isn’t needed, or the time interval could completely miss critical moments where collection is needed. These mission critical assets can cause serious downtime – and incurred costs- for manufacturers without a reliable way to monitor their machine health.
Enter the IoT HUB.
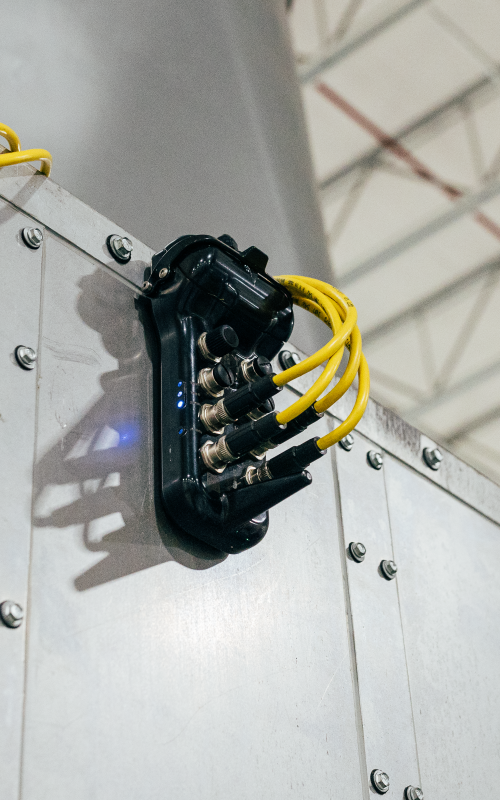
The IoT HUB completely revolutionizes the way manufacturers can monitor intermittent equipment. The HUB uses a special triggering technology, allowing for precise collection during the most important times during operation. By connecting to your PLC, the HUB knows exactly when to fire and when to sit dormant. This results in an easy-to-understand trend line that can highlight developing machine failures long before they happen.
Often the best way to get a full picture of an asset’s health is by incorporating multiple sensor types. However, this can be a challenge for many manufacturers without having all these data in a single pane of glass environment that allows for root cause analysis all in one place.
The IoT HUB includes seven ports, able to take in various types of inputs – vibration, temperature, oil humidity, MCSA, and more. The IoT HUB can even take in legacy sensors using the analog and IEPE adapters. Even better, these various input types can be streamed side by side, giving a true picture of the health of the asset.
Real World Case Studies
Case study 1 – Automotive Skillet Lifters
One automotive facility was experiencing issues with their skillet lifters upper and lower flanges. Skillet lifters are similar to vertical drop lifts that operate intermittently when adding or removing carriages (might need more explanation on what a carriage is). Skillet lifter flanges are prone to bearing failures, where they will effectively seize in the rolling elements, forcing downtime and ad hoc fixes. Traditional continuous monitoring makes it difficult to catch the precise moments of movement where fault indicators might appear, making this the perfect application for triggered HUB monitoring.
In this case, sensors were placed on the motor – main and standby, triggered by PLC logic, and then on the skillet lifters that add or remove the carriage itself. In addition, sensors were placed throughout the conveyance systems on the direct driven planetary gearbox. Throughout this system, there were numerous Skillet Lifters.
Following deployment, it was noticed through data that, when looking at the upper and lower flanges, one was vibrating three times higher than the other flanges. Using this data, it was discovered that a bearing was beginning to fail. Within two weeks, the issue was corrected by the facility’s maintenance team through planned maintenance, avoiding costly downtime.
Case Study 2 – Cranes
After installing triggered IoT HUBs on the bridge components, the data showed repetitious knocking on the south bridge motor that was not observed on the north bridge motor. KCF personnel worked with the customer to investigate this issue with the customer while on site and observed slop in the mounting brackets for the south bridge drive. The customer team implemented a temporary fix, which reduced the slop significantly, and plan to install a completely re-machined motor mounting in their outage in January.
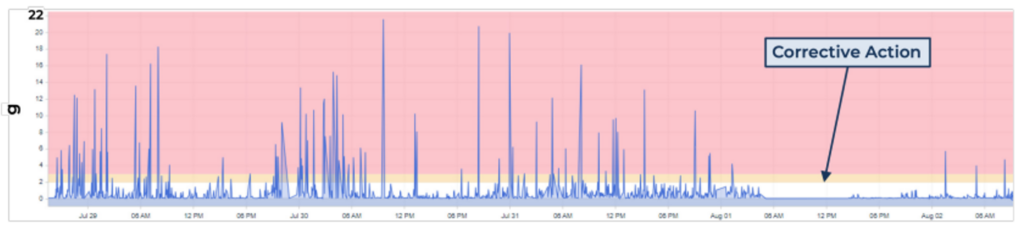
Sources: Sound and Vibration, January 2007 “The History of the Accelerometer: 1920’s-1996 – Prologue and Epilogue, 2006) By Patrick L. Walter
THE SMARTsensing PRODUCT CATALOG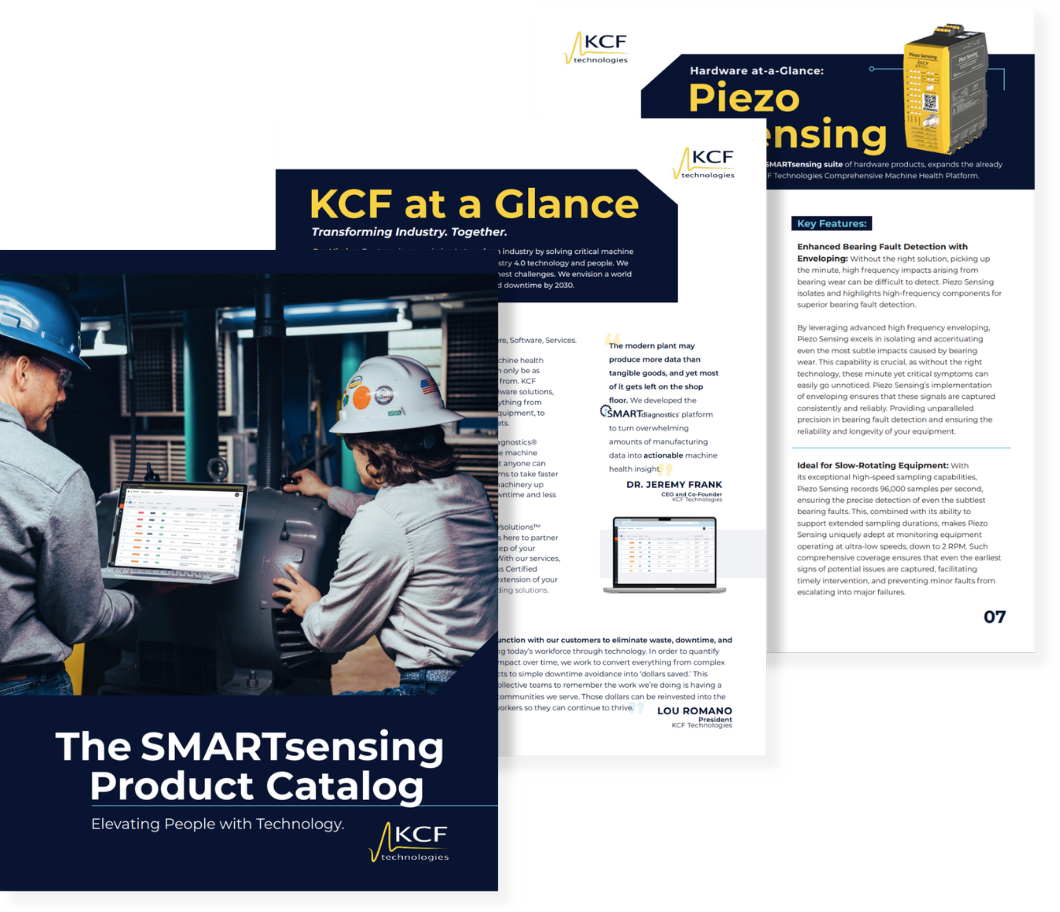
Your machine health optimization program can only be as
good as the data it’s built from. KCF provides ruggedized hardware solutions, designed to monitor everything from the most basic rotating equipment, to complex intermittent assets.
You can learn more about our Hardware Solutions in the SMARTsensing Product Catalog.