Introduction
Natural gas compressor stations are essential to the oil and gas industry. Companies build these stations along natural gas pipelines to compress the gas, allowing it to flow downstream to its final destination, which could be a processing facility, a storage tank, or retail and utility companies.
Natural gas is kept under high pressure as it flows through pipelines. To maintain this pressure, the gas needs to be periodically compressed along the pipeline. This is done at compressor stations, where the gas is compressed using turbines, motors, or engines.
Across North America, there are hundreds of these stations, located approximately 50 to 70 miles apart, providing the necessary “boost” to transport gas effectively from one point to another. These stations operate around the clock, 365 days a year.
One of the most problematic issues present at compressor stations is piping resonance. Piping resonance is a common and costly problem that occurs when the mechanical natural frequency of a piping system matches the frequency of a pulsation or mechanical source (the compressing unit). This can cause large vibrations in the piping. Continuous piping resonance can lead to cracks, leaks and valve failures. First and foremost, this poses a grave safety risk. In addition, the compressor unit and some times the entire station needs to be shut down to address the leaks which causes significant downtime.
Piping resonance can be primarily mitigated in the following ways:
- Structural Design Changes: this can include adjusting current supports/clamps, strategically adding new ones, and reconfiguring the piping layout. These changes allow us to alter the stiffness of the piping thereby shifting it’s natural frequency away from the dominating frequency.
- Optimizing Compressor Operating conditions: determining the operational sweet spots that do not coincide with the natural frequency of the pipe.
The age-old attempted solution involves route-based vibration monitoring. With this approach, key resonance windows and possible failure modes will go undetected between readings. Furthermore, time and weather limitations do not allow for measurement repeatability,
The solution is simple:
– a Comprehensive Predictive Maintenance Platform
- Resonance conditions detected in real time
- Remote monitoring with no restrictions on obtaining readings
- Correlate vibration data with operational parameters
Case Study Example 1
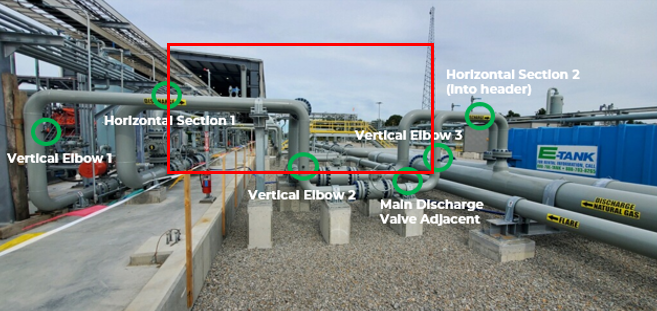

*The modifications targeted the section highlighted in the red box above by eliminating the vertical elbows and horizontal 90 section
In the example to the left, KCF had identified a section of discharge piping connected to the header that was experiencing excessive vibration. KCF worked with the customer’s engineering team to discover an improved design whereby the vertical elbows and sharp 90-degree junctions were eliminated, correcting excessive vibration levels.
Results
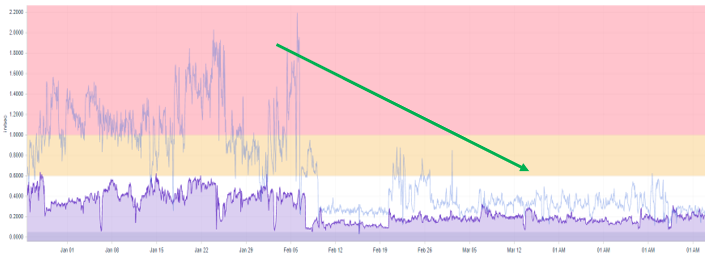
Case Study Example 2
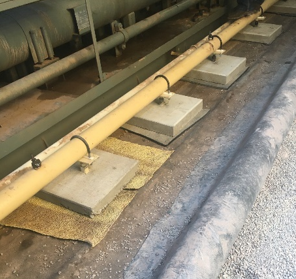
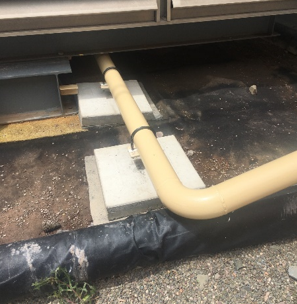
In the example to the left, KCF had identified specific piping sections adjacent to the compressor that needed additional support blocks. The addition of these concrete blocks resulted in a 70% reduction in vibration.
Results
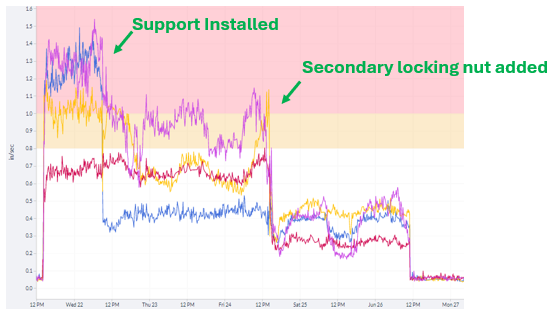
Case Study Example 3
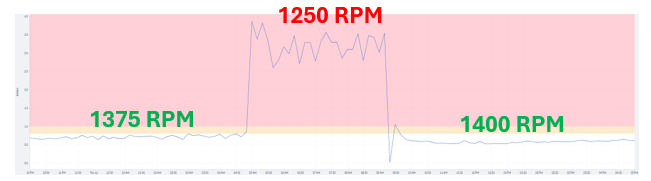
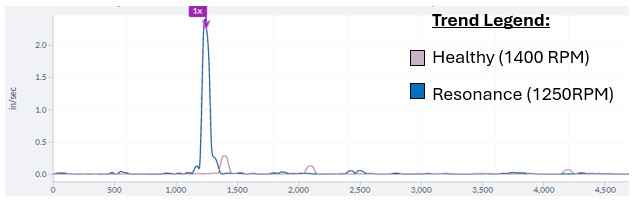
In the example to the left, KCF looked at the operating conditions and identified the compressor RPM range that leads to excessive resonance and elevated vibration. the customer to operate the compressors in a more optimal way and avoid these ranges when possible.
KCF Full Guide
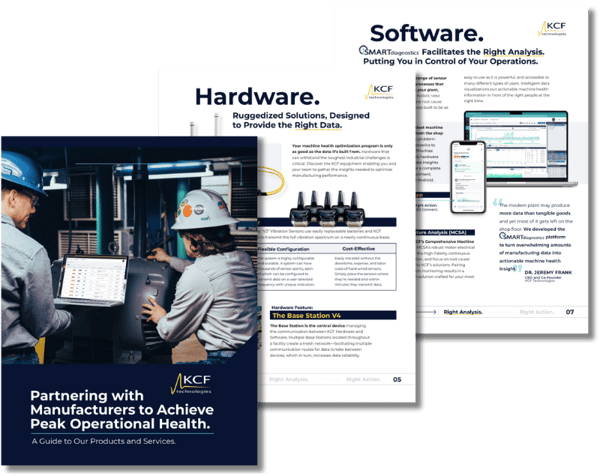
Learn more about gaining a competitive edge with the most advanced, comprehensive machine health optimization platform.