The 8 Steps to Running a Successful Predictive Maintenance Pilot
November 20, 2023 | Predictive Maintenance
Predictive maintenance (PdM) promises to revolutionize the way businesses approach equipment reliability and maintenance by predicting and preventing failures before they happen. While the benefits are undeniable, many companies struggle to get their PdM pilots off the ground. With an alarming number of pilots stalling out early, it’s crucial to understand and address the challenges head-on.
1. Set a Clear Success Criteria
Every pilot must start with a clear and well-defined objective. Without a specific criterion for success, it can be hard to judge if a pilot is proving value or not. Before jumping into a pilot, consider what it is you hope to achieve.
Is it getting to the root cause of a specific machine health challenge?
Is it reducing downtime by a specific percentage?
Or maybe saving a set amount on maintenance costs?
By setting precise goals, you can tailor your approach, measure progress, and have a benchmark for success.
2. Get Stakeholder Buy-in
One of the main contributors for pilot failure is lack of stakeholder buy-in. This includes not only upper management but also the front-line employees who will be using the system. At the front-line, there are a variety of factors that can lead to a lack of buy-in. Some may see this as a job replacer. Others may not believe in the technology’s effectiveness. Additionally, it’s important that the solution integrates seamlessly with the teams already existing daily workflows to create a smooth transition and minimal disruptions to daily activities.
Within upper management, there’s the desire to see fast return on investment.
At both levels, it’s important to share wins and successes frequently to keep teams engaged and seeing the positive effects of switching to a predictive machine health strategy. Initiate open dialogues, address concerns, and highlight the benefits PdM will bring. Regular communication and feedback sessions can help ease transitions and generate enthusiasm.
3. Selecting the Right Assets
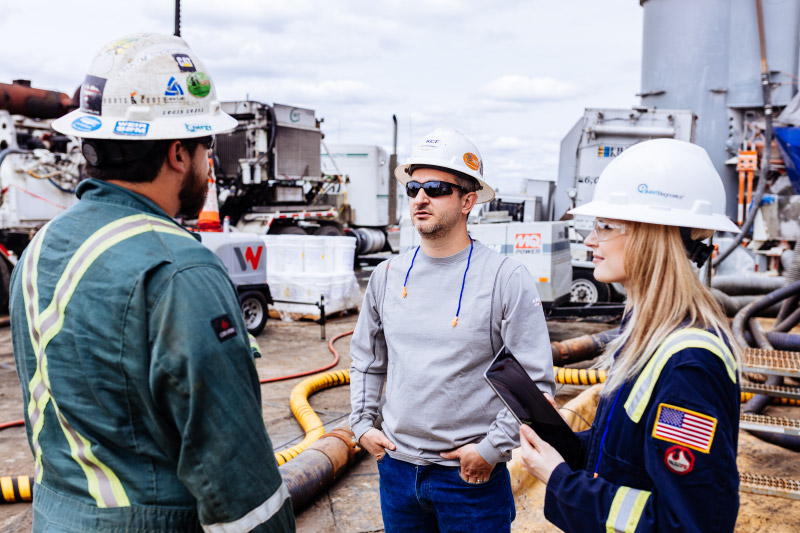
While a comprehensive machine health platform can support almost all asset types, not all equipment is suitable for a PdM pilot. Start with assets that:
- Are standard rotating equipment; such as fans, pumps, or motors
- Have a history of failures or other machine health issues
- Are critical to your operations.
Even if you are experiencing machine health challenges with more complex equipment, starting with equipment such as pumps and motors will be more advantageous for early wins. Demonstrate the fundamentals of the technology and then move on to solve the more complex issues with the full machine health platform. Once the pilot has been proven—by strategically choosing assets—you can showcase quick wins, which will promote adoption across the board.
4. Choosing the Right Predictive Maintenance Partner
With many predictive maintenance solutions in the market, it can be hard to determine who can live up to the hype. When choosing a vendor, it’s important to consider how they will support your team throughout the pilot. While some sites may be staffed with enough people to run a pilot almost completely internally, many others suffer from labor shortages. By partnering with a provider who acts as an extension of your team, you have the support you need to run a smooth pilot while maintaining normal operations.
5. Realistic Expectations
While predictive maintenance is transformative, it’s not magic. It’s essential to set realistic expectations. There will be a learning curve, and not every prediction will be spot-on, especially during system calibration. Communicate this to stakeholders to ensure they understand that refinement is part of the process and continuous improvement is the name of the game.
6. Continuous Feedback & Iteration
Once your pilot is up and running, actively seek feedback from all users. This not only helps in refining the process but also promotes a feeling of ownership among users, which can boost adoption rates.
7. Scalability Considerations
When the pilot proves successful, you’ll want to scale. Planning for scalability from the outset ensures that the transition from pilot to full-scale implementation is smooth. It’s important to think into the far future when choosing a vendor – what are your long-term goals? From the outset, choosing a provider with a system designed for scale is crucial – consider ease of install and overall usability.
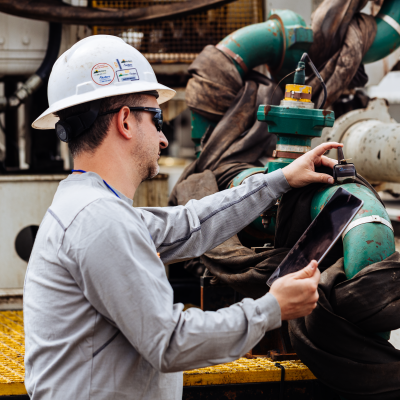
Choosing a vendor that can provide a wide-array of sensor types, such as vibration sensors, ultrasonic sensors, or tachometers, ensures wide asset coverage. Additionally, there are advanced capabilities only some providers can enable – such as real-time Motor Current Signature Analysis or monitoring of intermittent assets.
Software should be easy to use and act as a single pane of glass that your team can view all crucial machine health data from. If multiple types of users – from maintenance to reliability to operations – can understand the data, value can be seen first-hand. Translating complex data into easy-to-understand visuals is crucial for accessibility.
Finally, consider how the system will fit in with current infrastructure, long term. New technology can mean another screen to remember to look at. A scalable system should be able to seamlessly integrate into existing infrastructure, such as CMMS software, creating a single pane of glass and holistic view of your machine health. From the outset, choosing a provider with a system designed for scale is crucial—consider ease of install and overall usability.
8. Celebrate and Evangelize Successes
Celebrate and showcase every success, no matter how small. This keeps morale high and reinforces the value of the PdM initiative. Many pilots stall or fail simply due to lack of visibility. When the time comes to convert, upper stakeholders choose not to move forward due to a lack of value. Regularly updating stakeholders on progress and achieved benefits can create a ripple effect of enthusiasm.
Risk Free Guarantee.
Convert from Pilot to Partner or get your money back.
OPTIMIZE YOUR MACHINE HEALTH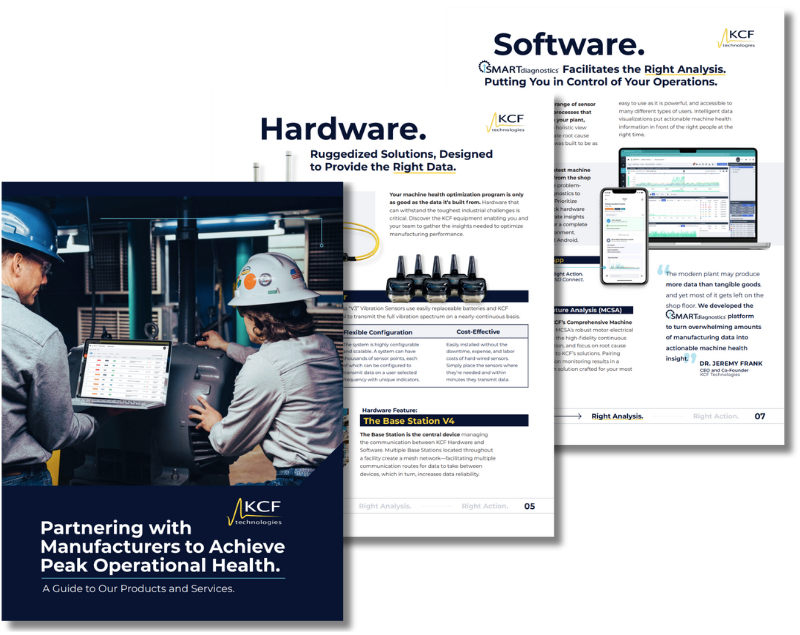
Predictive maintenance has the power to drive significant operational improvements and cost savings. However, the journey to a successful pilot can be riddled with challenges—but these challenges can be overcome. By proactively addressing these challenges, businesses can ensure that their predictive maintenance pilots don’t just take off but also soar to new heights of success.
You can learn more about our approach to predictive maintenance in the Full Machine Health Guide.