Using Machine Health Insights to Drive OEE Improvements
February 21, 2022 | Predictive Maintenance
In the manufacturing world, where insights, data, and people converge, one metric sets the standard for accurately measuring the productivity of equipment.
That measurement is OEE or Overall Equipment Effectiveness.
THE MEASURING STICK
- 100% OEE reflects perfect production
- 85% OEE is a world-class, long term goal
- 60% OEE leaves room for improvement
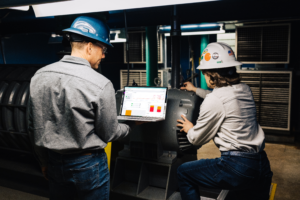
Several factors affect OEE performance, but in simple terms, it is fair to say that healthier Machines produce healthier results! If Machine life is extended, Availability, Performance, and Quality will all increase. And inversely, energy costs, repair costs, safety incidents, and waste will decrease.
Predictive maintenance goes far beyond putting sensors on a machine, although that’s an important first step. A systematic approach that identifies the right opportunity for increased performance is where true value is delivered. Data can then be provided by a range of sensors to quickly impact Maintenance and OEE performance.
Driving OEE improvement through machine health, starts with the right data enabling the right analysis to recommend the right actions on the front line. This is the secret sauce.
AVAILABILITY
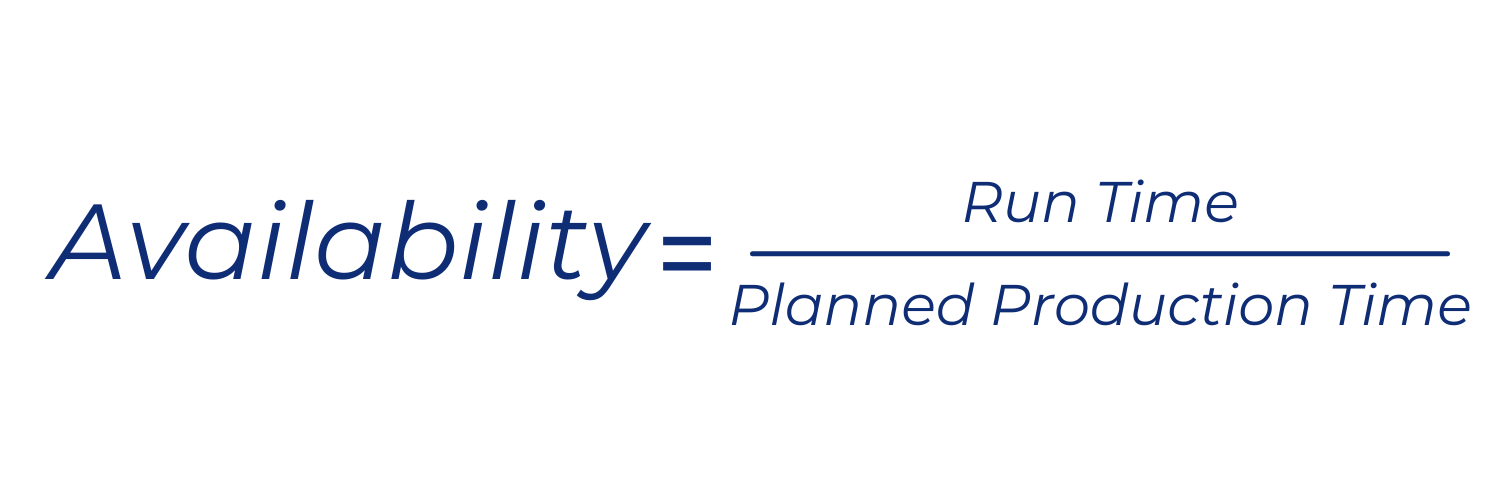
Availability Loss occurs when production stops unexpectedly because of operational error or mechanical failure. Identifying those potential failures through sensors, predictive alarming, Artificial Intelligence/Machine Learning gives the predictive analysis needed to have quick wins that ultimately drive availability.
Quick wins come from sensors that identify failures before they happen. This immediately reduces unplanned downtime. Intelligent data visualizations, customizable by job function, area, or component type, put actionable machine health information in front of the right people at the right time so that availability improves from day one.
KCF’s SMARTdiagnostics is a Machine Health Platform that brings powerful insights and actions to plants of all sizes, whether you have a handful of monitoring points or thousands of sensors deployed.
PERFORMANCE
Performance loss speaks to the need for understanding the physics, root cause analysis, and optimization of Machine Health
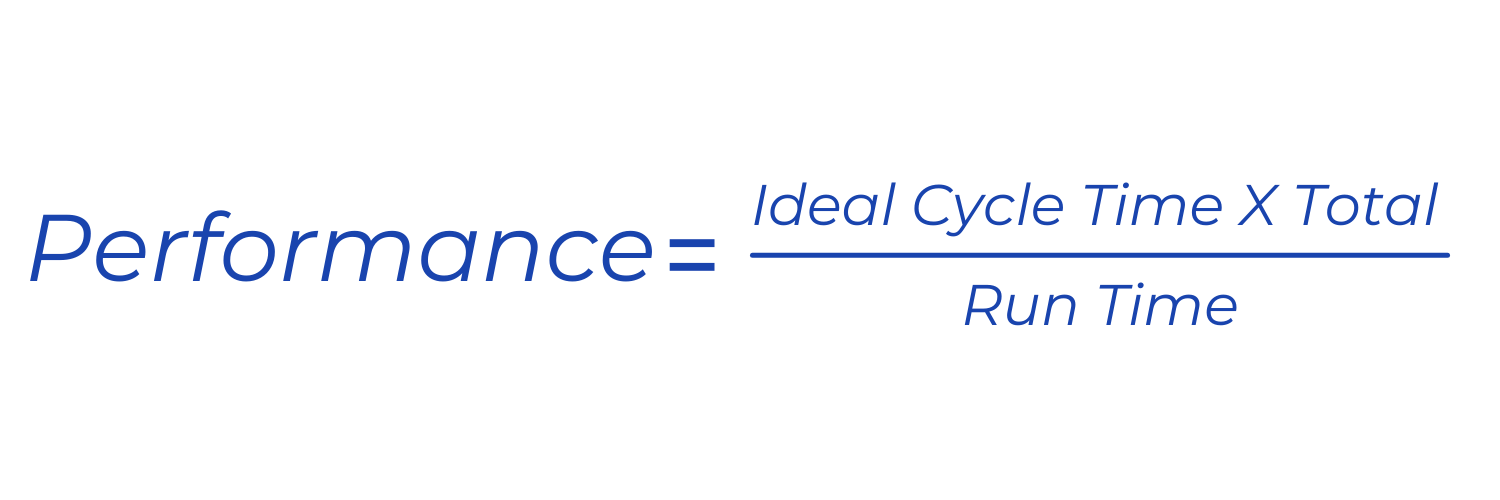
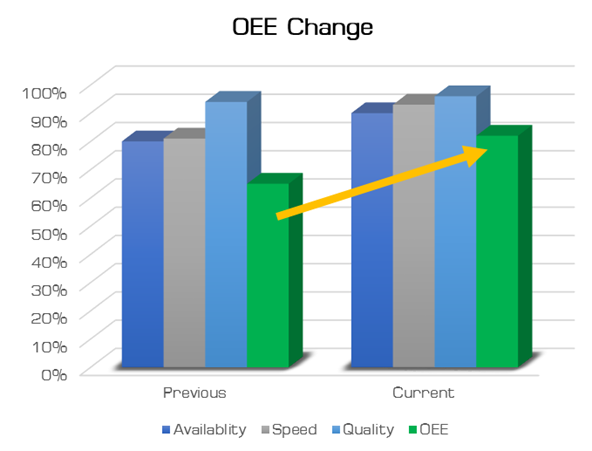
Root cause analysis—determining why an asset fails—is what sets the SMARTdiagnostics machine health optimization platform apart from the rest. Understanding a machine’s Behavior in context can greatly increase the speedy realization of what parameters directly contribute to speed loss, helping to remove the Root Cause of the degradation.
PLC data integrated with machine health data enables automated setpoint adjustments for optimal performance under any operating conditions. In addition, planned maintenance efficiency and efficacy are increased with predictive, prescriptive, and prioritized maintenance guidance.
QUALITY
Quality loss is minimized when machines operate and are operated, correctly. Through custom dashboards, leaders can set and monitor KPIs for plants, divisions, production lines, and shifts, driving continuous improvement across all operations. Dashboards with quality data drive quicker action to address elements that affect quality.
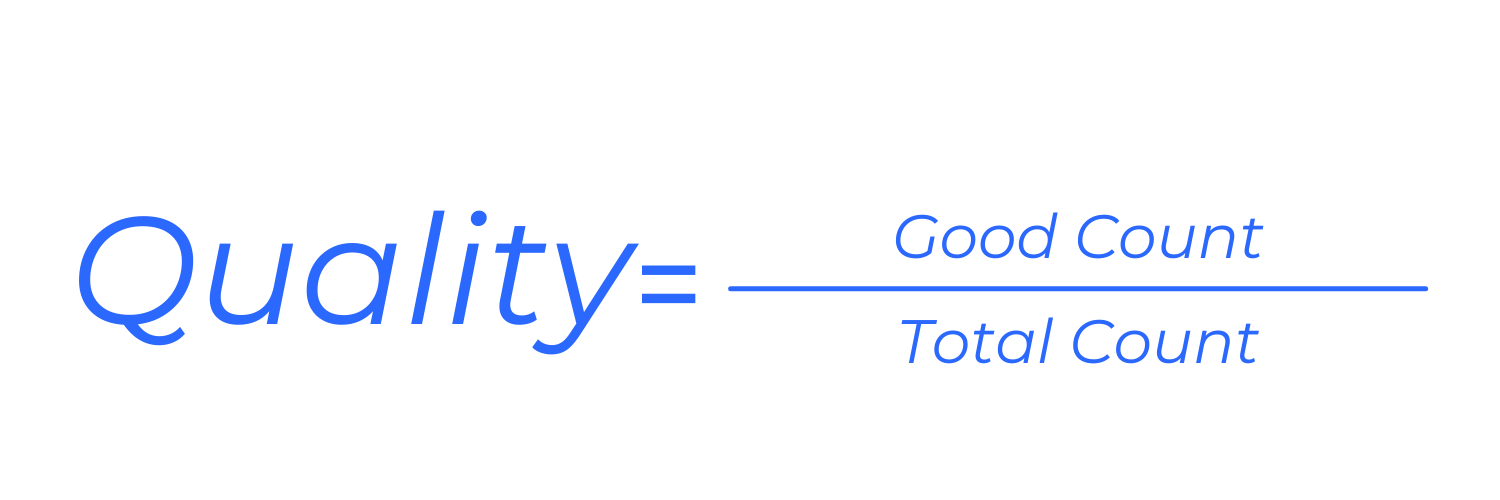
As Availability and Performance detractors are addressed, Quality naturally becomes the center of focus, and with time and labor resources free to focus on quality, new Quality production records become more achievable than ever.
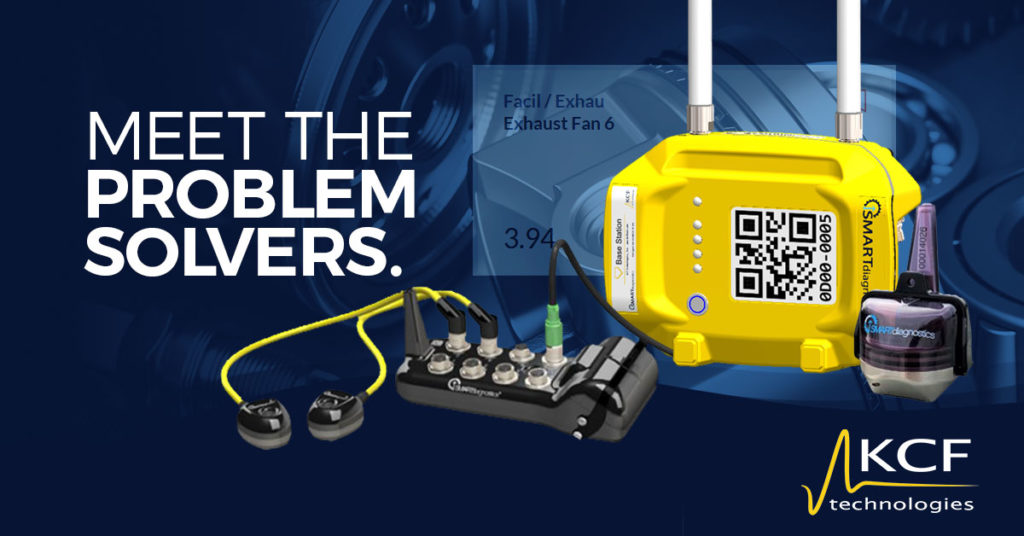