4 Surprising Benefits of Predictive Maintenance in Manufacturing and Industry
November 30, 2023 | Predictive Maintenance
Predictive maintenance (PdM) is revolutionizing manufacturing and industry and is best known and sought out for benefits like reducing unplanned downtime. However, there are many less obvious benefits that come along with transitioning to a predictive maintenance program. While there are even more benefits, and more uncovered daily, here are just four of the surprising advantages of predictive maintenance that are transforming operations in unexpected ways.
Increased Safety: A Hidden Gem of Predictive Maintenance
Safety is paramount in a manufacturing or industrial setting. However, the most common time for injuries to occur in the workforce is during times of unexpected maintenance. Additionally, those that are using route-based maintenance routinely put themselves in dangerous areas necessary to take readings. Both scenarios can be eliminated with a properly implemented PdM program. Predictive maintenance elevates safety standards by proactively identifying potential equipment failures before they occur. This foresight prevents accidents and ensures a safer working environment, contributing to employee well-being and compliance with safety regulations.
Reduction in Energy Consumption: Eco-Friendly Operations
One often-overlooked benefit of PdM is its role in reducing energy consumption. Without prospering monitoring techniques, equipment can be using significantly more energy than needed.
A KCF Technologies customer saw savings of $1M in just one year from the insights they received by continuously monitoring their energy consumption.
By optimizing equipment performance and preventing over-exertion or underutilization of machinery, predictive maintenance ensures energy-efficient operations. This not only cuts down costs but also supports eco-friendly practices, aligning with the growing emphasis on sustainability in industry.
Understanding Process Anomalies and Changes
Process changes can create strange anomalies in vibration data. In fact, over 50% of machine failures are directly caused by improper operating conditions. Without having streaming data of operating parameters, it can be difficult to correlate where spikes in vibration or other health indicators are coming from. Predictive maintenance offers a deep dive into the intricacies of industrial processes. By pairing nearly continuous machine health data with process data, clear correlations can be made. By monitoring equipment performance and analyzing data trends, PdM helps in understanding process anomalies and changes, allowing for timely adjustments. This insight is crucial for developing new standard operating practices that prioritize machine health without sacrificing throughput.
Identifying Improper Maintenance: A Step Towards Optimization
The uncomfortable truth is nearly 30% of machine failures are due to improper maintenance. While this is almost never malicious, anytime human intervention is introduced, it opens room for human error. Simple errors like over or under lubricating or improper alignment can cause major issues down the road. With real-time data, the health of the equipment after maintenance can be seen almost instantly. By simply studying did the trend line go up or down, it can be easy to identify when maintenance has helped or if it has hurt – in some cases actually introducing new problems. PdM helps in identifying instances of improper maintenance, ensuring that all interventions are effective and contribute positively to equipment health. This aspect of PdM is crucial for maintaining a high standard of equipment care and prolonging the life of machinery.
OPTIMIZE YOUR MACHINE HEALTH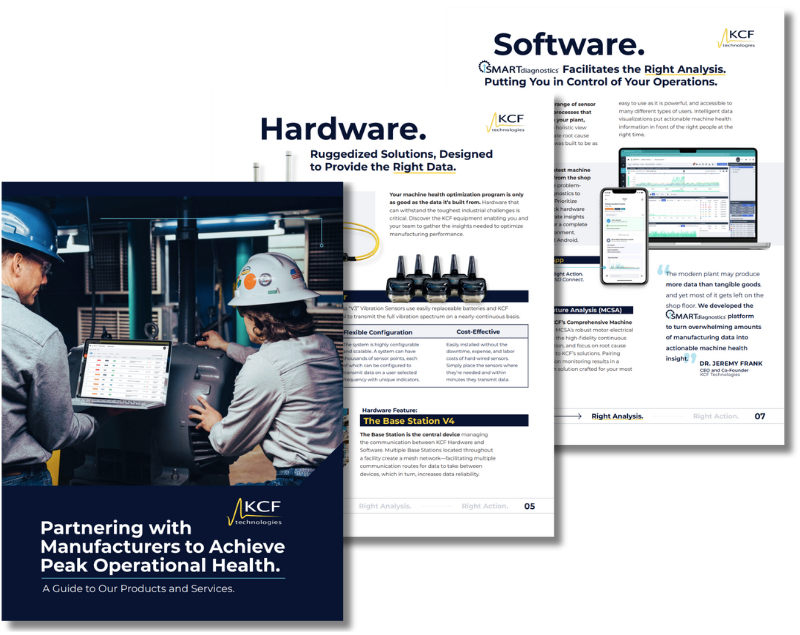
Predictive maintenance goes beyond the obvious, offering a range of benefits that enhance safety, efficiency, and operational intelligence. By embracing these advantages, businesses can not only improve their bottom line but also foster a safer, more sustainable, and smarter industrial environment.
You can learn more about our approach to predictive maintenance in the Full Machine Health Guide.