Stopping the Vulnerability with Drilling Rigs
February 22, 2023 | Press Releases
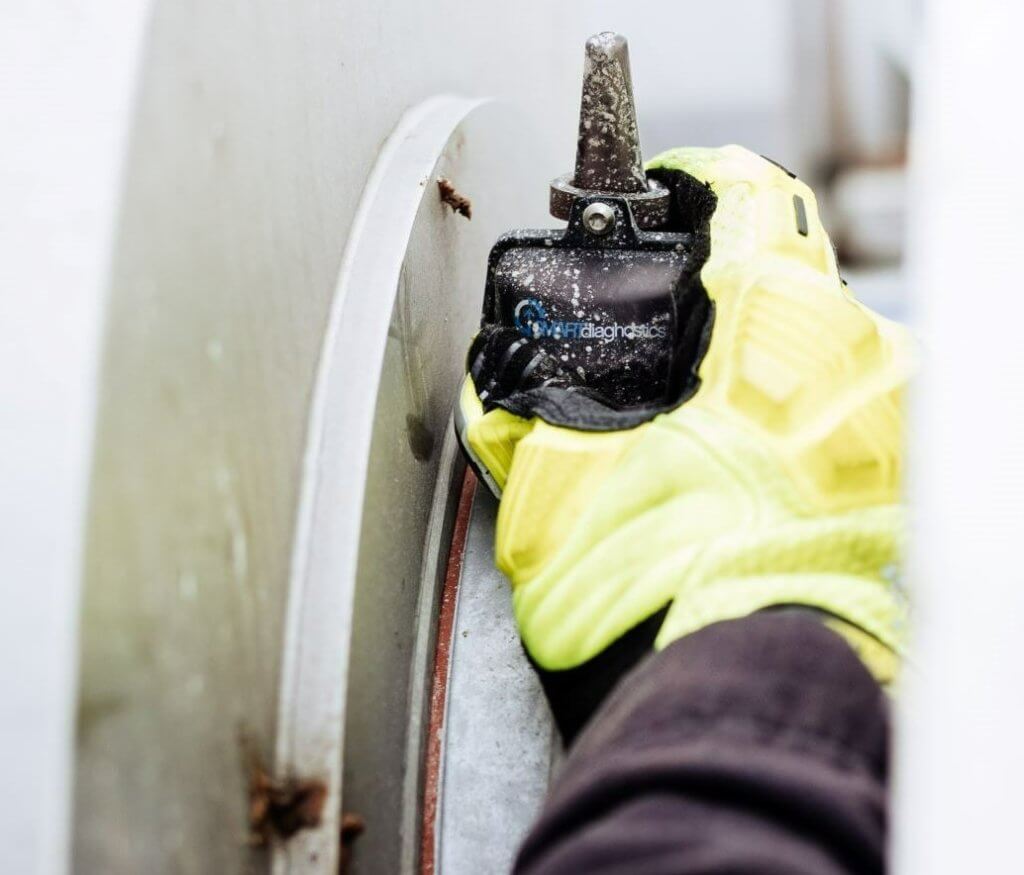
Drilling is tough – drilling into machine health, on the most vulnerable components of a drilling rig, shouldn’t be.
Top drives and mud pumps are two of the most critical components on a drilling rig and can benefit most from continuous monitoring and predictive maintenance. The top drive motor and gearbox allows for more precise control of the drilling process, helping to increase on bottom drilling time and reduce downtime. For upstream drilling operations, having a continuous monitoring system is critical.
When a top drive fails, drilling can no longer occur and the operation comes to a halt. If the failure is severe enough and lasts long enough, the risk of the drill string getting stuck in the hole increases exponentially. This results in significant downtime and adds costs for the entire drilling operation.
The cost of downtime when a top drive fails can vary depending on several factors, including the severity of the failure, the part of the well the failure occurs, and the size and complexity of the drilling rig. Generally, the longer the downtime, the greater the cost.
Top Critical Components on a Drilling Rig
Top Drive
Mud Pumps
Drawworks
Generators
Costs incurred from safety exposures and halted drilling operation:
- Repairs or replacement of the top drive and any other equipment that may have been damaged.
- Retrieving and reassembling the drill string.
- Any additional labor and equipment required to resume the drilling operation.
- Any environmental cleanup or remediation that may be required as a result of the failure.
- Indirect costs such as delays in production schedules and lost contracts.
- Safety hazards, such as the release of drilling fluids or the collapse of the drill string.
Conventional monitoring of the top drive is to have regular routine or preventive maintenance and inspections to prevent such failures. However, this creates challenges when a severe failure occurs unexpectantly. Top drives’ consumables and associated spare parts are rarely stocked at the rig as a backup, if at all, on an offshore location.
Onshore vs Offshore
Drilling offshore is more expensive than drilling onshore. Higher operating costs from harsh and remote environments, materials, equipment, spare parts, and maintenance all contribute to higher expenses. Offshore drilling also adds logistic challenges, strict safety and environmental requirements, and complex infrastructure. These factors contribute to offshore drilling being two to three times more expensive than onshore drilling.
Offshore drilling can have higher profitability potential due to the larger reserves and longer production time of the wells. Thus making the importance of continuous monitoring that much greater.
Top Drive Traction Motor
The Problem
The traction motor provides the torque needed to move the top drive along the drill string. Traction motors are crucial to drilling operations due to the high-performance demands and high cost of NPT per hour. There can be electrical and mechanical faults on traction motors. One example is bearing failures. When bearing health deteriorates, it leads to reduced or complete loss of drilling performance and the inability to perform necessary operations – making connections, gripping/ releasing pipe. There’s also the potential for unsafe working conditions for operators on the rig floor.
Top Drive Blind Spots
- Electrical and mechanical faults tend to go unaddressed until a failure occurs due to the nature of drilling rig operations. The Top Drive remains in continuous operation and in an elevated position.
- Frequent thorough inspection of component internals is not possible due to complexity of the machine and continuous operations.
- Time-based and preventive maintenance protocols do not allow for continuous monitoring of critical rig components.
The Old Way
Historically drilling equipment consumables have been run to failure. This methodology maximizes the life span of the equipment, but at the cost of additional risk to incurring NPT hours and imposing safety hazards on the rig crew.
The New Way
Continuous vibration health monitoring can help optimize mechanic and electrician deployment, maintenance routines, preparedness for replacement, and mitigating potential safety incidents. Continuous monitoring opens potential opportunities for studies to extend Top Drive life and optimize field operations.
Monitoring Solution
- HARDWARE: Five KCF Technologies wireless vibration sensors.
- SOFTWARE: Thresholds set for automated anomaly detection, dashboard reporting, quality checking maintenance performed, and understanding root cause of issues.
- REAL-TIME DATA: Real time data allows for accurate maintenance and asset recommendations faster, giving less time needed analyzing and more time taking predictive actions. Electronic Drilling Recorder (EDR) is recommended but not required. (Top drive RPM & Torque generated)
ROI and Industry Savings Potential
Onshore Drilling
Cost of Top Drive Downtime:
$5,000/hour Downtime Cost
>12 hrs Downtime
Savings Potential: ~$60,000
$85,000 Replacement per Motor
>$145,000 in total Savings
Impact of Savings Potential on ROI
8x – 19x* ROI
*Assuming one predicted event per year
Offshore Drilling
Cost of Top Drive Downtime:
$15,000/hour Downtime Cost
>12 hrs Downtime + Replacement Parts
Savings Potential: ~$60,000
$85,000 Replacement/Motor + Delivery
>$265,000 in total Savings Parts
Impact of Savings Potential on ROI
24x – 35x* ROI
*Assuming one predicted event per year
FOR FURTHER INFORMATION, PLEASE CONTACT
Sean Buda
VP, Marketing
937.570.4893
KCF TECHNOLOGIES
KCF Technologies exists to drive sustainability, safety, and competitiveness for our partners and their communities by solving the world’s machine health problems. Our team empowers industry to eradicate downtime, waste, and injuries with KCF’s Comprehensive Machine Health Platform. We combine condition monitoring data with shop floor insights and maintenance practices to paint a complete picture of the factory environment. Failure is engineered out of the processes using KCF’s proprietary machine health optimization solution — made up of hardware, software, and services. Our impact on industry has prevented over $3.5B in unplanned downtime since 2018.