Detener la vulnerabilidad con plataformas de perforación
22 de febrero de 2023 | Comunicados de prensa
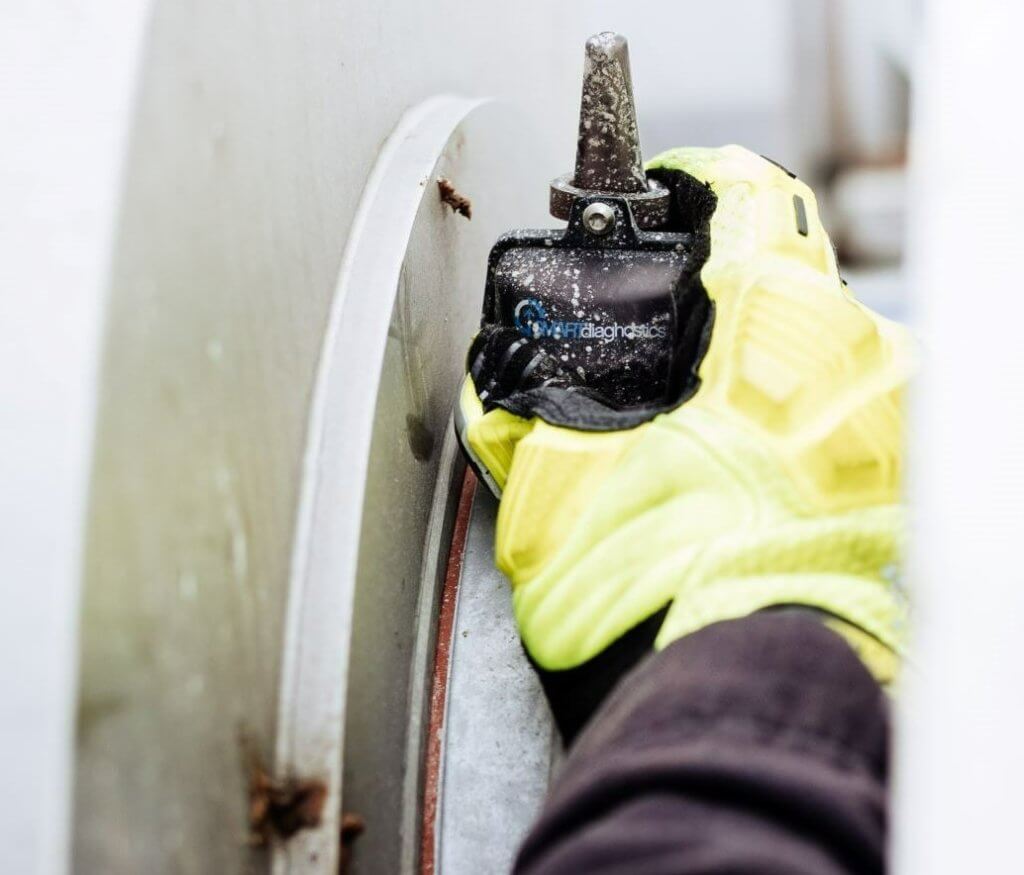
Perforar es difícil, pero no debería serlo perforar la salud de la máquina, en los componentes más vulnerables de un equipo de perforación.
Los top drives y las bombas de lodo son dos de los componentes más críticos de un equipo de perforación y los que más pueden beneficiarse de la supervisión continua y el mantenimiento predictivo. El motor y la caja de engranajes de los top drives permiten un control más preciso del proceso de perforación, lo que ayuda a aumentar el tiempo de perforación en fondo y a reducir los tiempos de inactividad. Para las operaciones de perforación de fondo, es fundamental contar con un sistema de supervisión continua.
Cuando falla un top drive, ya no se puede perforar y la operación se detiene. Si el fallo es lo suficientemente grave y dura lo suficiente, el riesgo de que la sarta de perforación se atasque en el agujero aumenta exponencialmente. El resultado es un tiempo de inactividad significativo y costes añadidos para toda la operación de perforación.
El coste del tiempo de inactividad cuando falla un top drive puede variar en función de varios factores, como la gravedad del fallo, la parte del pozo en la que se produce el fallo y el tamaño y la complejidad del equipo de perforación. Por lo general, cuanto mayor sea el tiempo de inactividad, mayor será el coste.
Principales componentes críticos de una perforadora
Top Drive
Bombas de lodo
Malacates
Generadores
Costes derivados de la exposición a riesgos de seguridad y de la interrupción de las operaciones de perforación:
- Reparación o sustitución del top drive y de cualquier otro equipo que pueda haber resultado dañado.
- Recuperación y reensamblaje de la sarta de perforación.
- Cualquier mano de obra y equipo adicionales necesarios para reanudar la operación de perforación.
- Cualquier limpieza o remediación medioambiental que pueda ser necesaria como resultado de la avería.
- Costes indirectos, como retrasos en los programas de producción y pérdida de contratos.
- Peligros para la seguridad, como la liberación de fluidos de perforación o el colapso de la sarta de perforación.
El control convencional del top drive consiste en realizar inspecciones y tareas de mantenimiento rutinarias o preventivas para evitar estos fallos. Sin embargo, esto plantea problemas cuando se produce un fallo grave de forma imprevista. Los consumibles de los top drives y las piezas de repuesto asociadas rara vez se almacenan en la plataforma como reserva, si es que se almacenan, en un emplazamiento en alta mar.
Onshore vs Offshore
Perforar en alta mar es más caro que hacerlo en tierra. Los costes de explotación son más elevados debido al entorno hostil y remoto, los materiales, los equipos, las piezas de repuesto y el mantenimiento. Las perforaciones en alta mar también plantean retos logísticos, estrictos requisitos medioambientales y de seguridad, y una infraestructura compleja. Estos factores contribuyen a que la perforación en alta mar sea de dos a tres veces más cara que la perforación en tierra.
La perforación en alta mar puede tener un mayor potencial de rentabilidad debido a las mayores reservas y al mayor tiempo de producción de los pozos. De ahí la importancia de la supervisión continua.
Motor de tracción Top Drive
El problema
El motor de tracción proporciona el par necesario para mover el top drive a lo largo de la barra de perforación. Los motores de tracción son cruciales para las operaciones de perforación debido a las exigencias de alto rendimiento y al elevado coste de NPT por hora. Los motores de tracción pueden sufrir fallos eléctricos y mecánicos. Un ejemplo son los fallos en los cojinetes. Cuando la salud de los cojinetes se deteriora, se reduce o se pierde por completo el rendimiento de la perforación y no se pueden realizar las operaciones necesarias, como hacer conexiones o sujetar y soltar la tubería. También pueden darse condiciones de trabajo inseguras para los operarios en la plataforma.
Puntos ciegos en la conducción
- Los fallos eléctricos y mecánicos tienden a pasar desapercibidos hasta que se produce una avería debido a la naturaleza de las operaciones de las plataformas de perforación. El Top Drive permanece en funcionamiento continuo y en posición elevada.
- Debido a la complejidad de la máquina y a las operaciones continuas, no es posible realizar inspecciones minuciosas frecuentes de los componentes internos.
- Los protocolos de mantenimiento preventivo y basado en el tiempo no permiten una supervisión continua de los componentes críticos de la plataforma.
A la antigua usanza
Históricamente, los consumibles de los equipos de perforación se han utilizado hasta el fallo. Esta metodología maximiza la vida útil del equipo, pero a costa de un riesgo adicional de incurrir en horas NPT e imponer riesgos de seguridad a la tripulación de la plataforma.
El nuevo camino
La monitorización continua del estado de las vibraciones puede ayudar a optimizar el despliegue de mecánicos y electricistas, las rutinas de mantenimiento, la preparación para la sustitución y la mitigación de posibles incidentes de seguridad. La monitorización continua abre oportunidades potenciales para que los estudios amplíen la vida útil de Top Drive y optimicen las operaciones sobre el terreno.
Solución de supervisión
- HARDWARE: Cinco sensores de vibración inalámbricos de KCF Technologies.
- SOFTWARE: Establecimiento de umbrales para la detección automática de anomalías, la elaboración de informes sobre cuadros de mando, la comprobación de la calidad del mantenimiento realizado y la comprensión de la causa raíz de los problemas.
- DATOS EN TIEMPO REAL: Los datos en tiempo real permiten un mantenimiento preciso y recomendaciones de activos más rápidas, dando menos tiempo necesario para analizar y más tiempo para tomar acciones predictivas. Se recomienda el uso de un registrador electrónico de perforaciones (EDR), aunque no es obligatorio. (RPM y par generados por el accionamiento superior)
Retorno de la inversión y potencial de ahorro del sector
Perforación en tierra
Coste del tiempo de inactividad de Top Drive:
5.000 $/hora Coste del tiempo de inactividad
>12 horas de inactividad
Potencial de ahorro: ~60.000 dólares
85.000 $ de sustitución por motor
>145.000 $ de ahorro total
Impacto del potencial de ahorro en la rentabilidad
8x - 19x* ROI
*Suponiendo un evento previsto al año
Perforación en alta mar
Coste del tiempo de inactividad de Top Drive:
15.000 $/hora Coste del tiempo de inactividad
>12 horas de inactividad + piezas de repuesto
Potencial de ahorro: ~60.000 dólares
85.000 $ Sustitución/Motor + Entrega
>265.000 $ en total Ahorro Piezas
Impacto del potencial de ahorro en la rentabilidad
24x - 35x* ROI
*Suponiendo un evento previsto al año
PARA MÁS INFORMACIÓN, DIRÍJASE A
Sean Buda
VP, Marketing
937.570.4893
TECNOLOGÍAS KCF
KCF Technologies existe para impulsar la sostenibilidad, la seguridad y la competitividad de nuestros socios y sus comunidades mediante la resolución de los problemas de salud de las máquinas del mundo. Nuestro equipo capacita a la industria para erradicar el tiempo de inactividad, los residuos y las lesiones con la Plataforma Integral de Salud de la Máquina de KCF. Combinamos los datos de monitorización del estado con la información del taller y las prácticas de mantenimiento para obtener una imagen completa del entorno de la fábrica. Los fallos se eliminan de los procesos mediante la solución de optimización del estado de las máquinas patentada por KCF, compuesta por hardware, software y servicios. Nuestro impacto en la industria ha evitado más de 3.500 millones de dólares en paradas no planificadas desde 2018.