El viaje hacia la madurez del mantenimiento predictivo
Ya no se puede discutir sobre las ventajas del mantenimiento predictivo basado en la condición frente al mantenimiento preventivo basado en el tiempo.
La mayoría de los fabricantes que han invertido en fiabilidad introduciendo la tecnología de supervisión del estado de las máquinas han obtenido rápidamente un retorno de la inversión y, como resultado, han experimentado un aumento significativo de la productividad. Otros fabricantes que siguen ciñéndose a programas de mantenimiento preestablecidos y realizan una supervisión basada en rutas siguen luchando por gestionar su gasto global en mantenimiento y aumentar la eficacia operativa de los equipos (OEE).
Los datos lo respaldan.
Según un informe de la Alianza de Fabricantes de 2022:
Muchos fabricantes se estancan cuando alcanzan un nivel básico de implantación del mantenimiento predictivo. La mayoría de los modelos de madurez del mantenimiento muestran el mantenimiento predictivo (o prescriptivo) como el destino. A un alto nivel, esto es correcto, pero deja fuera la mitad del viaje. Quedan muchas etapas de madurez por alcanzar una vez que se adopta un enfoque de mantenimiento predictivo o basado en la condición.
Esta guía arrojará luz sobre esa segunda mitad del viaje, guiándole a través de los cuatro pilares de la madurez del mantenimiento predictivo y ayudándole a acelerar las ganancias de ingresos que permite el Mantenimiento Predictivo (PdM).
La primera mitad del viaje
Esta es la guía avanzada de la madurez del mantenimiento predictivo, así que suponemos que ya sabe por qué tantos fabricantes inteligentes están motivados para adoptar un enfoque del mantenimiento basado en la condición. Aun así, es útil revisar la primera mitad del viaje para comprender mejor la segunda.
Los fabricantes que aún no han iniciado su andadura en el mantenimiento predictivo siguen practicando el mantenimiento reactivo. Este enfoque -hacer funcionar las máquinas hasta que fallen antes de arreglarlas- es una estrategia excelente si se está esperando a cambiar una bombilla. De lo contrario, se traduce en un elevado número de horas de inactividad no planificadas, márgenes cada vez menores y equipos de mantenimiento estresados.
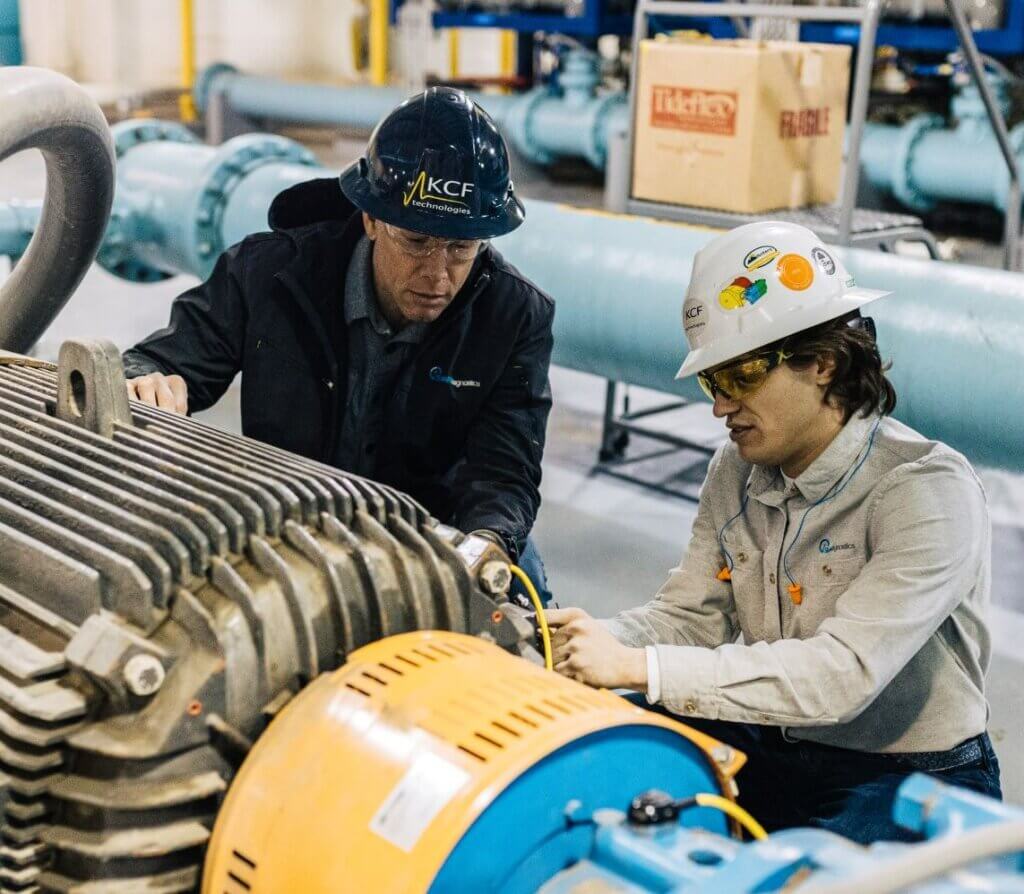
Practicar el mantenimiento reactivo significa tomar la decisión consciente de asignar la mayor parte de sus recursos de mantenimiento (y, por tanto, un alto porcentaje de sus gastos totales de explotación) a reaccionar ante los problemas. A menudo se confunde reaccionar ante los problemas de salud de las máquinas con resolverlos.
A menudo se confunde la prevención de los problemas de salud de las máquinas, que es el objetivo del mantenimiento preventivo, con la resolución de los problemas de salud de las máquinas. El mantenimiento preventivo tiende a basarse en el tiempo o en el uso, lo que significa que los equipos de mantenimiento realizan tareas programadas con regularidad para mantener los activos en condiciones óptimas de funcionamiento. Este enfoque sólo tiene éxito una parte del tiempo y tiende a ser un despilfarro. Las máquinas no se averían a intervalos regulares, y el mantenimiento preventivo innecesario no resuelve los problemas crónicos de salud de los activos.
En esta primera mitad del viaje hacia la madurez del mantenimiento, el paso más significativo es pasar del mantenimiento basado en el tiempo al mantenimiento basado en la condición. Con la adición de hardware de monitorización continua, los equipos de mantenimiento de fabricación pueden realizar tareas de fiabilidad vinculadas al estado real de un activo, lo que elimina el despilfarro de PM y reduce el tiempo de inactividad no planificado. La monitorización del estado permite el mantenimiento predictivo, ayudando a los fabricantes a comprender la correlación entre el momento de las acciones de mantenimiento y el rendimiento de la máquina.
Este es el camino básico hacia la madurez del mantenimiento. Si aún no ha llegado a este punto, no está solo: muchos fabricantes siguen trabajando con una combinación de estrategias de mantenimiento preventivo y de ejecución hasta el fallo. Por supuesto, muchos fabricantes también siguen luchando por seguir siendo competitivos y mejorar su cuenta de resultados. Según nuestra experiencia, ambas cosas suelen estar relacionadas.
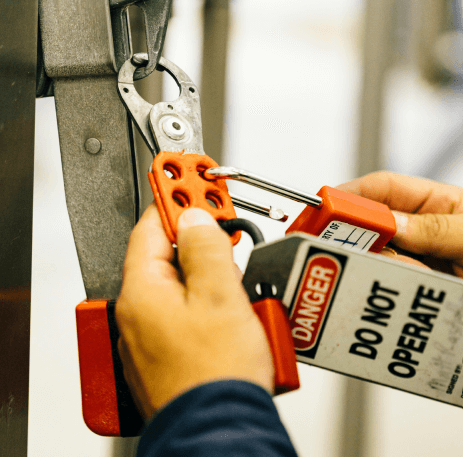
Desbloquear la segunda mitad del viaje
con la tecnología de Industria 4.0
El resto del viaje hacia la madurez del mantenimiento -elverdadero objetivo de esta guía- viene después de la adopción inicial de la tecnología de mantenimiento basado en la condición. La tecnología conectada es la clave de la mejora continua de la fiabilidad y constituye uno de los cuatro pilares de la verdadera madurez del mantenimiento predictivo.
Con la tecnología y la experiencia adecuadas que impulsen sus esfuerzos de fiabilidad, los fabricantes pueden lograr una mejor inteligencia en la toma de decisiones y modelos de negocio más eficientes, lo que conduce a una mayor flexibilidad operativa, menos gastos generales y una mayor productividad. La tecnología moderna de salud de las máquinas no se limita a observar sus activos, sino que revela el comportamiento de las máquinas en diferentes condiciones de funcionamiento y permite un análisis preciso de las causas raíz para que pueda resolver de forma permanente los problemas de salud de sus activos.
Los cuatro pilares de la madurez del mantenimiento predictivo
Existen cuatro pilares -o áreas clave de crecimiento- para los fabricantes que deseen avanzar en su estrategia de mantenimiento predictivo.
1. Instrumentación
2. Integración
3. Generación de ideas
4. Optimización
Avanzar en cada área clave no es un proceso estrictamente lineal, pero deben dominarse los fundamentos de cada una antes de pasar al siguiente pilar. Por ejemplo, los fabricantes tienen que instrumentar sus activos con el hardware de monitorización de estado adecuado antes de abordar la integración, y necesitan sistemas integrados para empezar a trabajar en la generación de información.
Profundicemos en cada uno de los cuatro pilares.
1. Instrumentación
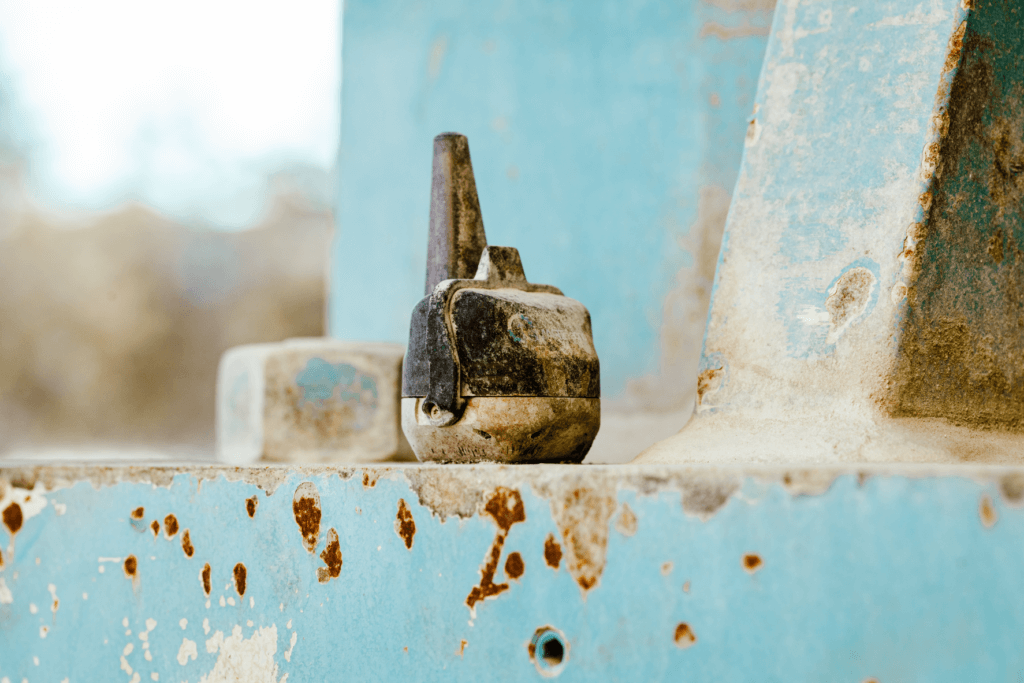
Empezar con una cantidad limitada de hardware a modo de prueba piloto -porejemplo, instrumentando sólo una clase de activos para su monitorización remota- es un enfoque que muchos fabricantes adoptan al adoptar el mantenimiento basado en la condición, y es una buena forma de probar el retorno de la inversión antes de una implantación más amplia. Por esta razón (entre otras), la escalabilidad es una consideración importante a la hora de elegir un proveedor de hardware de monitorización del estado de las máquinas.
Muchos vendedores promocionan la flexibilidad del hardware como una ventaja de sus productos, pero la "flexibilidad" suele ser "falta de soporte" disfrazada. Por supuesto, la flexibilidad para supervisar una serie de máquinas, incluidas las que funcionan de forma intermitente, es importante. Sin embargo, siempre hay una forma óptima de instrumentar un activo determinado para detectar los problemas exclusivos de ese activo. La flexibilidad conlleva a veces falta de estandarización. Si tiene dos activos idénticos en dos plantas distintas que se instrumentan de forma diferente, los datos que recopile no le ayudarán a identificar problemas comunes ni a aplicar las mejores prácticas en toda la organización.
Busque la escalabilidad combinada con la ingeniería interna y la experiencia en el estado de las máquinas de su proveedor para garantizar un despliegue estandarizado, junto con ayuda para interpretar los datos iniciales que recopile y obtener los primeros beneficios. Debería poder eliminar las catástrofes con un despliegue inicial basado en la física que cubra los activos rotodinámicos más comunes, utilizando algoritmos preestablecidos para detectar señales de fallo clave. A partir de aquí, establecerá Indicadores Clave de Rendimiento (KPI) de la máquina y líneas de base operativas para determinar los umbrales de alarma adecuados.
A medida que los fabricantes avanzan en la madurez de la instrumentación, se pueden introducir tipos de sensores adicionales, incluidos sensores que pueden supervisar con precisión la maquinaria que funciona de forma intermitente. Los activos con ciclos repetidos de carga y descarga son muy susceptibles de sufrir daños por vibraciones, pero la monitorización tradicional de vibraciones no puede detectar con fiabilidad los fallos de estas máquinas.
La fiabilidad de la red también es un factor crítico en la madurez de la instrumentación. Depender por completo de las señales WiFi o de telefonía móvil significa perder inevitablemente puntos de datos que podrían indicar un fallo inminente. Una estrategia de instrumentación sofisticada incluye una red de malla fiable que proporcione cobertura permanente incluso a las zonas más remotas de las plantas, con una infraestructura de copia de seguridad de los datos que garantice que no se pierda ni un detalle si falla la red.
El pilar de la instrumentación incluye el software que respalda el despliegue de hardware. Los datos sólo son útiles si pueden enrutarse, interpretarse y visualizarse de forma que su equipo pueda actuar, sacando a la luz inmediatamente las anomalías del proceso y los fallos inminentes. La escalabilidad también es importante en este caso: debe poder beneficiarse de datos procesables desde el primer día, pero también debe tener la capacidad de desplegar cuadros de mando personalizados avanzados, alertas basadas en funciones e integraciones.
2. Integración
Toda planta de fabricación moderna depende de una serie de plataformas de software para que sus operaciones funcionen sin problemas. Cada una de ellas desempeña un papel importante, pero la desconexión entre plataformas puede hacer que se pierdan conocimientos y se malgasten recursos.
El software de monitorización del estado de las máquinas es especialmente susceptible de perder eficacia operativa por falta de integración. Las acciones de mantenimiento suelen organizarse, priorizarse y registrarse a través de la GMAO, mientras que el software de estado de las máquinas funciona en un silo separado. Es posible que la información sobre los procedimientos operativos estándar (SOP) y los puntos de ajuste del operario no esté conectada a ninguno de los dos sistemas; a menudo, sólo se consideran conocimientos institucionales y pueden variar drásticamente de una línea a otra o de un operario a otro.
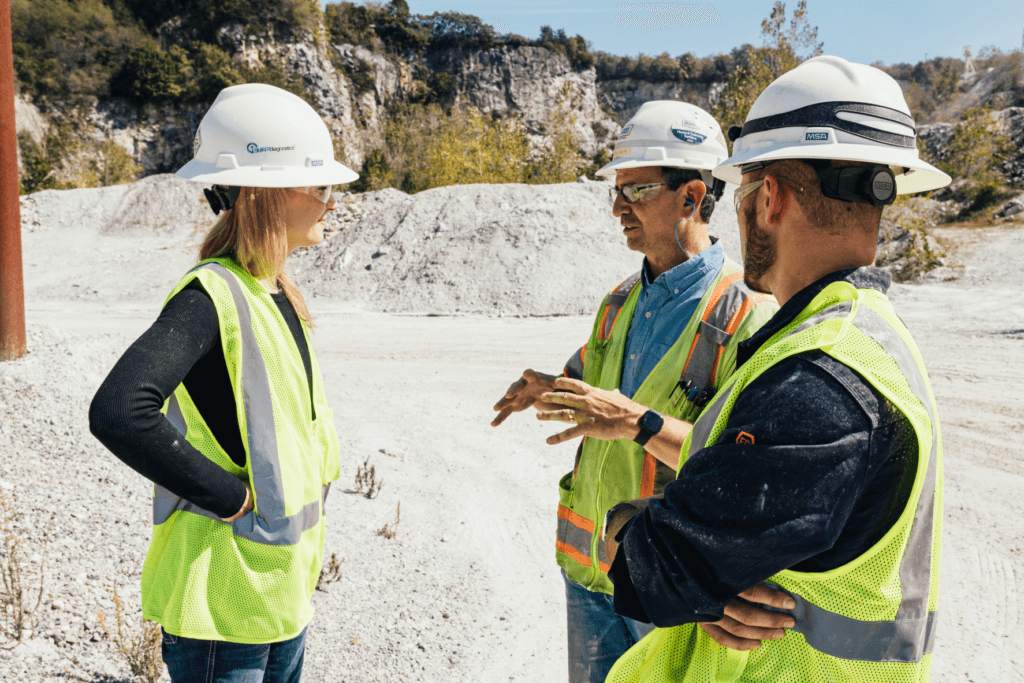
La madurez de la integración incluye la creación de conectividad entre su software de supervisión del estado de la máquina, un motor de diagnóstico para permitir el mantenimiento prescriptivo, su GMAO para flujos de trabajo de mantenimiento de bucle cerrado y otras plataformas de datos críticos (por ejemplo, su ERP para flujos de trabajo de piezas de repuesto).
Si estas plataformas permanecen aisladas, los fabricantes pueden perderse algunas de las ventajas más valiosas que ofrecen las estrategias avanzadas de mantenimiento predictivo, como la priorización y validación del mantenimiento. Más de la mitad de las actividades de mantenimiento preventivo tienen un efecto neutro o incluso negativo en la salud de la máquina, pero es imposible saber qué mitad sin un medio para registrar y medir el efecto de las actividades de mantenimiento en el contexto de sus datos de salud de la máquina. Una plataforma de monitorización de activos desconectada de su GMAO no puede hacer aflorar fácilmente este tipo de información crítica, ni puede proporcionar análisis de criticidad o priorización.
Los grandes fabricantes (o las organizaciones más pequeñas altamente especializadas) a menudo tendrán requisitos personalizados de integración y/o seguridad de datos para su arquitectura de datos empresariales. Su proveedor debe ser capaz de gestionar estos requisitos con un equipo interno de TI e ingeniería capaz de garantizar que todos los sistemas estén conectados estratégicamente y extraigan los datos correctos (y solo los datos correctos) para obtener información procesable sobre el estado de las máquinas.
Para obtener ganancias rápidas en esta área de madurez del mantenimiento predictivo, busque una solución que ofrezca integraciones estándar de procesos y GMAO frente a una que requiera una configuración personalizada y práctica cada vez que integre un nuevo sistema.
3. Generación de ideas
Los líderes del sector manufacturero saben que la promesa de la Industria 4.0 no es una fábrica inteligente totalmente automatizada que requiera una mínima intervención humana. Las personas siempre han sido, y seguirán siendo, nuestro recurso de fabricación más valioso. Los fabricantes sofisticados invierten en generar conocimientos para que su personal esté siempre capacitado para tomar las medidas más informadas, eficientes y centradas en los resultados en la planta de producción.
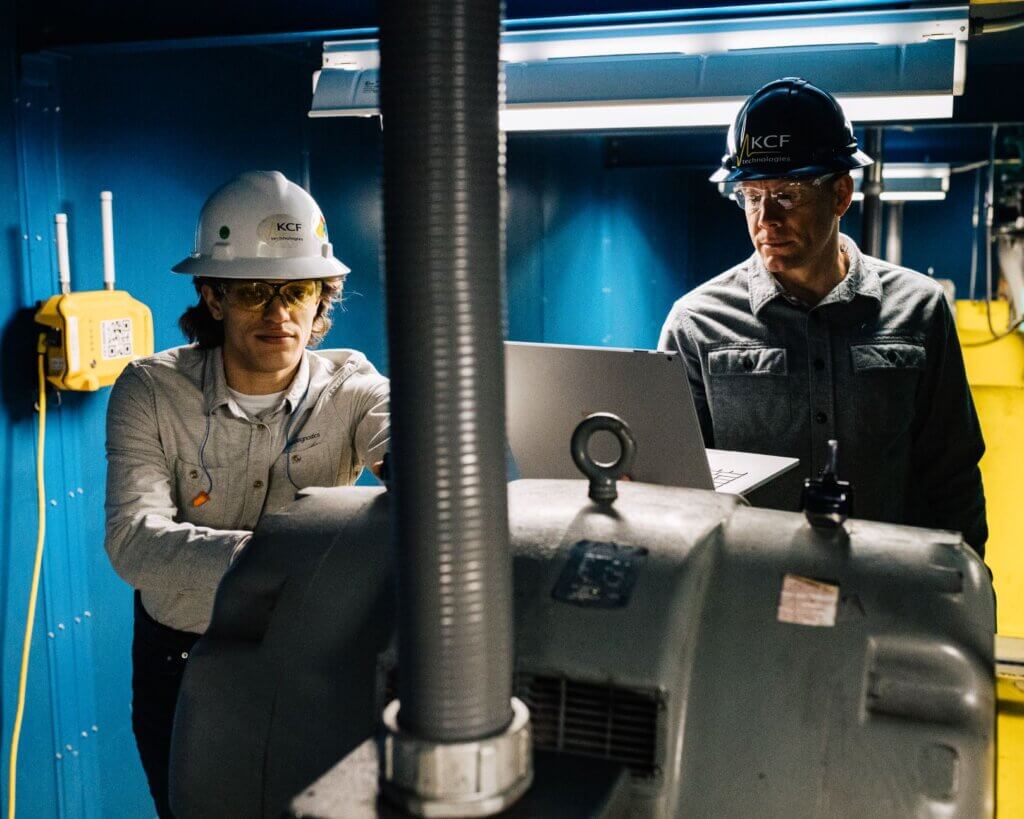
La generación de conocimientos de "nivel básico" en su viaje hacia la madurez del mantenimiento predictivo comienza con la alarma automatizada (adaptada a las líneas de base de sus máquinas).
Los avances en la generación de información sólo se consiguen cuando se ha alcanzado un nivel de madurez en la instrumentación que permite identificar anomalías y tomar medidas al respecto. Si su equipo de monitorización remota proporciona datos sin procesar que solo puede leer un analista de vibraciones certificado, la generación de información sufre un grave retraso, lo que le cuesta productividad e ingresos finales.
Alcanzar la madurez en el ámbito de la generación de información comienza con la elección de una plataforma que sea capaz de hacer llegar la información adecuada a las personas adecuadas con un mínimo de fricción en el camino. Las visualizaciones fáciles de entender (por ejemplo, los cuadros de mando de activos que dejan claro cuáles de sus máquinas necesitan atención de mantenimiento y el orden de prioridad recomendado para cada una) son clave.
La generación de información no debe ser una caja negra. Aunque los algoritmos predefinidos para las clases de activos comunes son imprescindibles, la clasificación extremadamente precisa de los problemas sólo puede lograrse incorporando los comentarios de los expertos en la materia y del taller. Las condiciones reales de funcionamiento de su planta, día a día y hora a hora, son un factor crítico para crear información automatizada y hacerla llegar a las personas que pueden marcar la diferencia.
Demostrando que las personas son el activo más importante en cualquier entorno de fabricación, incluso con la entrega de información totalmente automatizada, la intervención humana es necesaria en cada paso para tomar información sobre el estado de la máquina y convertirla en una mayor eficiencia operativa. Los operarios, los directivos y los profesionales de la fiabilidad tienen que trabajar juntos para mejorar las condiciones operativas basándose en las recomendaciones proporcionadas por una sofisticada plataforma de estado de las máquinas. El cambio cultural es clave, pero puede resultar difícil: el socio adecuado para la optimización del estado de las máquinas puede ayudarle con una gestión del cambio adaptada a su entorno específico.
4. Optimización
El último pilar de la madurez del mantenimiento predictivo representa un área de potencial de crecimiento casi infinito. Los fabricantes que inviertan en la instrumentación, la integración y la tecnología de generación de conocimiento adecuadas encontrarán continuamente nuevas formas de optimizar sus operaciones.
En la primera fase de la madurez del mantenimiento predictivo, los equipos de fabricación pasan de apagar fuegos constantemente a ser capaces de predecir y evitar fallos inminentes. En esta segunda fase, los fabricantes pueden aprender a eliminar por completo los fallos de sus procesos.
Con los datos correctos recopilados por el hardware adecuado, es posible comprender plenamente las condiciones de la planta, incluidas las variables introducidas por diferentes operarios, diferentes productos y diferentes procesos. A continuación, los fabricantes pueden aprovechar el aprendizaje automático y la IA para determinar la mejor forma de hacer funcionar una máquina. Esto parece una optimización continua sobre la marcha, basada en las condiciones actuales, para maximizar la productividad y eliminar por completo los tiempos de inactividad no planificados.
Más allá de eso, una plataforma inteligente de optimización del estado de la máquina puede ayudar a los equipos de fiabilidad a reducir los tiempos de inactividad planificados recopilando información sobre acciones de mantenimiento anteriores y ayudando a los equipos a determinar cuáles de ellas son útiles y cuándo. Los sólidos datos históricos sobre el estado de las máquinas pueden indicar cuánto tiempo puede funcionar una máquina antes de necesitar realmente un mantenimiento planificado, lo que ayuda a programar el tiempo de inactividad en torno a los momentos críticos de producción.
Un entorno de producción con cero residuos, cero incidentes de seguridad, cero tiempos de inactividad imprevistos y tiempos de inactividad planificados mínimamente perturbadores está al alcance de todo fabricante dispuesto a emprender el viaje.
Continúe su viaje hacia el mantenimiento predictivo
Lograr una estrategia avanzada de mantenimiento predictivo requiere una serie de componentes críticos que deben estar estrechamente integrados. La integración personalizada, la limpieza de datos y la interoperabilidad pueden llevar años. El primer paso hacia el éxito debe ser la elección de una solución completa, que reduzca drásticamente el tiempo de obtención de valor.
Las herramientas para impulsar el cambio operativo no son más que un medio para alcanzar un fin. Es necesario un cambio en las prácticas de los trabajadores, y hay que prepararse para ello. Si su equipo de mantenimiento sigue engrasando en exceso los rodamientos a pesar de que el software de estado de la máquina señala el activo y recomienda que el mantenimiento preventivo ha sido ineficaz, el rodamiento seguirá fallando prematuramente.
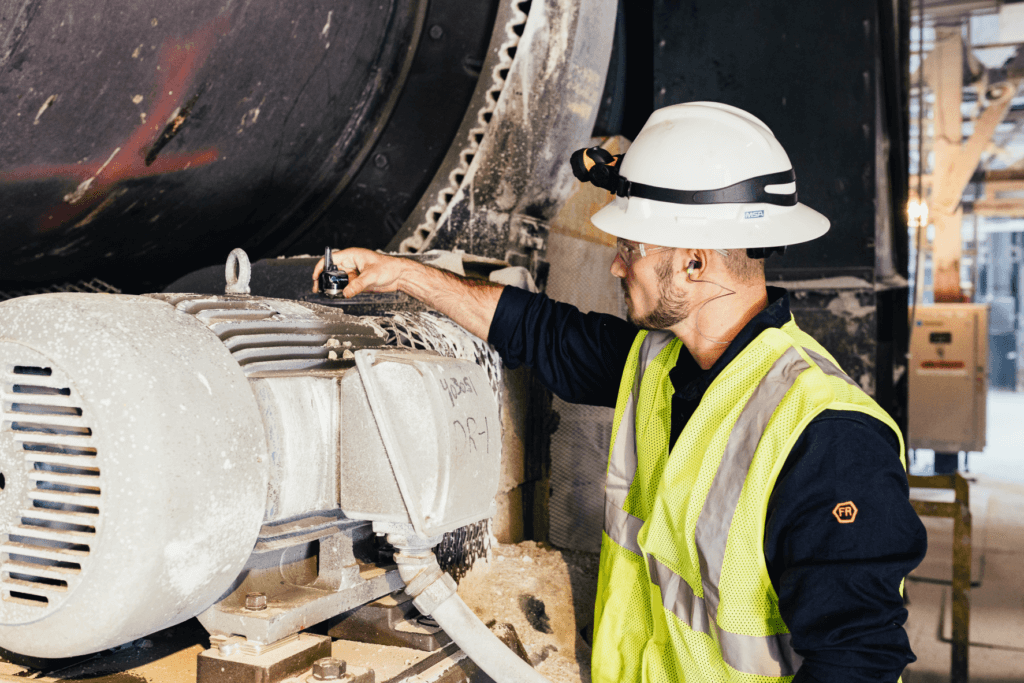
El valor prometido por la madurez del mantenimiento predictivo sólo se alcanzará cuando los líderes, directivos, profesionales del mantenimiento y operarios cambien la forma en que hacen su trabajo día a día. Con demasiada frecuencia, el entusiasmo inicial por una nueva solución o método se ve sustituido por la complacencia y, en última instancia, por una vuelta a las prácticas heredadas.
La adopción práctica de su estrategia madura de mantenimiento predictivo necesita el apoyo de un socio orientado al crecimiento que ofrezca servicios de educación y formación. También debe ofrecer conocimientos específicos del sector, ayudándole a instrumentar correctamente su maquinaria y a proporcionar análisis de datos avanzados.
Cuanto más avance en la madurez del mantenimiento predictivo, más retorno de la inversión podrá obtener y más se diferenciará de sus competidores.
Ofertas de KCF
para los cuatro pilares de la madurez del mantenimiento
KCF existe para elevar a las personas y resolver los problemas de la Industria 4.0. Imaginamos un mundo en el que nuestros clientes no tengan lesiones, residuos ni fallos de activos. Conectamos eficazmente tecnologías de vanguardia con soluciones reales que mejoran las instalaciones industriales y las comunidades a las que sirven para un futuro sostenible.
NUESTRA MISIÓN
Instrumentación
OFERTAS KCF: Transmisión de datos fiable mediante el protocolo DARTwireless; Mayor duración de la batería para facilitar el uso y la instalación; Cobertura completa de todos los activos, ya sean equipos giratorios comunes o activos complicados e intermitentes.
Integración
OFERTAS KCF: Integraciones estándar con datos de procesos de planta y datos de GMAO.
Generación de ideas
OFERTAS KCF: Analítica basada en 289.364 horas de salud de la máquina; Construido sobre una base de conocimiento de vibración de clase mundial, pionero por el co-fundador Gary Koopman, fundador del Centro de Acústica y Vibración; Equipo dedicado de ingenieros y analistas de vibración para validar las llamadas y actuar como una extensión de su equipo.
Optimización
OFERTAS KCF: Integraciones para una visibilidad total; datos de alta frecuencia para un análisis avanzado de las causas raíz; herramientas de software para realizar un seguimiento de la eficacia del mantenimiento e informar sobre los puntos de ajuste ideales de la máquina y las prácticas de mantenimiento; equipo de ingenieros de SENTRY para apoyar y guiar a su equipo en su viaje de PdM.
Las operaciones más inteligentes empiezan aquí
reserve su demostración de smartdiagnostics
Nuestra misión es transformar la industria resolviendo permanentemente los problemas críticos de salud de las máquinas. Desarrollamos soluciones inteligentes y valientes para afrontar los retos más difíciles de los activos de fabricación.
¿Le impiden los retos relacionados con la salud de las máquinas obtener una ventaja competitiva y alcanzar todo su potencial de ingresos? Nosotros podemos ayudarle.