Un mejor enfoque de la salud de los activos
Los enfoques tradicionales para gestionar la salud de las máquinas ya no son suficientes para conseguir y mantener la competitividad en el panorama actual de la fabricación. La optimización de la salud de las máquinas representa una nueva forma de pensar y operar que puede desbloquear el potencial de generación de ingresos de su negocio y proporcionar 10 veces el ROI de sus inversiones en salud de las máquinas.
Esta página contiene una hoja de ruta para guiarle en su viaje hacia la optimización del estado de las máquinas. En primer lugar, debe comprender por qué el camino que sigue actualmente puede estar creando las condiciones de funcionamiento subóptimas que le están frenando.
Hay una forma mejor de gestionar la salud de sus activos, su planta y su empresa en su conjunto.
El mayor reto que hay que superar cuando se avanza hacia la optimización del estado de las máquinas es rechazar la forma en que siempre se han hecho las cosas. Si se realiza una evaluación honesta, los enfoques tradicionales para la gestión de la salud de la máquina probablemente han dado lugar a:
- "Salvar el día" pero sin abordar la causa raíz del fallo del equipo
- Mantenimiento incorrecto
- Trabajar de forma reactiva después de que se haya producido un problema
- Análisis de datos ajenos a la realidad cotidiana de su planta
- Los operarios desconocen el impacto de sus consignas en la vida útil de los equipos
- El conocimiento institucional que impulsa el mantenimiento, cada vez más peligroso a medida que los gurús del mantenimiento se marchan o se jubilan.
- Prácticas incoherentes de una planta a otra, o incluso entre divisiones de producción de una misma planta.
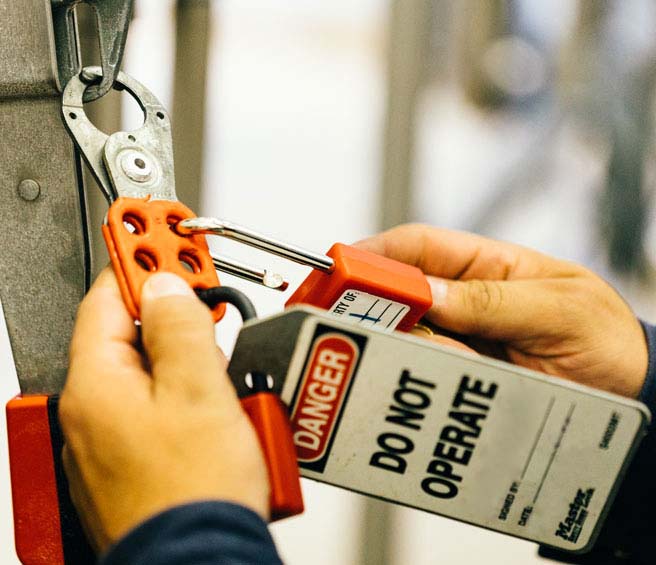
El mantenimiento reactivo es una estrategia excelente... si estás esperando a cambiar una bombilla.
En las últimas décadas, el enfoque convencional de la gestión del estado de las máquinas ha evolucionado más allá del simple mantenimiento reactivo: esperar a que se produzca un fallo para hacer algo al respecto. El mantenimiento reactivo es una estrategia excelente si se está esperando a cambiar una bombilla, pero lo es mucho menos cuando se trata de equipos de fabricación complejos y de los costosos efectos de las paradas imprevistas.
La mayoría de los fabricantes practican hoy en día el mantenimiento preventivo, el predictivo o una combinación de ambos. Ninguno de los dos enfoques logra una verdadera optimización de los activos de la planta, pero cada uno es un buen punto de partida.
Mantenimiento preventivo
El mantenimiento preventivo (MP) fue la primera iteración de un enfoque mejor para gestionar la salud de las máquinas y todavía se practica ampliamente en la actualidad. La teoría en la que se basa el MP es que las máquinas están sanas cuando se ponen en marcha y funcionan por primera vez, y luego se desgastan de forma bastante predecible a lo largo del tiempo. Para evitar averías, el mantenimiento se programa a intervalos regulares -normalmente en función de las horas de funcionamiento o de los días naturales- antes de que se prevea que se va a producir un fallo.
Este enfoque funciona... en teoría.
Si se sabe aproximadamente cuánto tiempo se espera que duren una máquina y sus componentes, se debería poder intervenir antes de que se produzca un desgaste excesivo y evitar los fallos indefinidamente. Pero cualquiera que haya practicado el mantenimiento preventivo sabe que esto no es así: los fallos siguen produciéndose, y con regularidad. Esto hace que, por regla general, el mantenimiento preventivo resulte caro. A menudo se realiza el servicio cuando no es necesario, y aproximadamente el 80% de las actividades de PM tienen un efecto neutro o incluso negativo en la salud de la máquina.
El fracaso es casi siempre aleatorio
Cualquier factor puede provocar un fallo de los equipos: los productos de sus líneas cambian, el mantenimiento programado se realiza de forma incorrecta o alguien deja caer una herramienta sobre una máquina. En este caso, la degradación de la salud de la máquina no sigue una pendiente recta hacia el fallo. Incluso podría parecer una línea recta, con la misma probabilidad de fallo en todo momento.
Décadas de investigación demuestran que los modelos de fallo aleatorio son más precisos que los modelos dedesgaste predecible en más del 80% de las ocasiones. Sólo una pequeña minoría de equipos muestra un comportamiento de desgaste predecible.
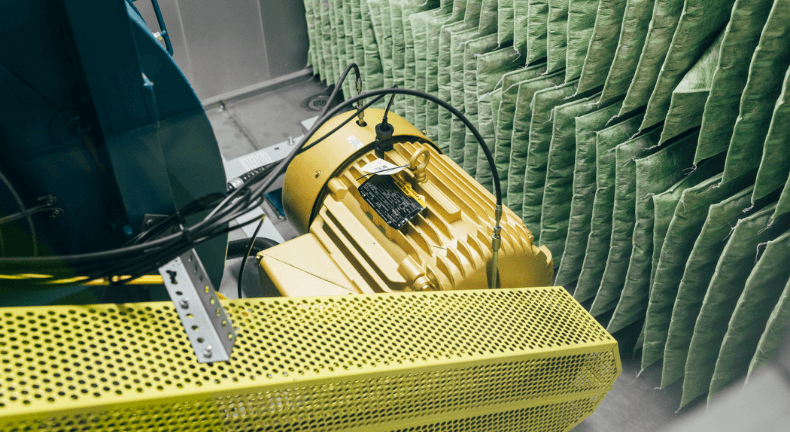
Mantenimiento predictivo
Una vez que los fabricantes se dieron cuenta de que los llamados fallos aleatorios eran al menos tan probables como los fallos predecibles, el mantenimiento predictivo (PdM) se convirtió en la siguiente evolución de la gestión del estado de las máquinas. La premisa del mantenimiento predictivo es que las condiciones de salud de las máquinas pueden cambiar rápidamente y la degradación no siempre es predecible sin datos adicionales, por lo que las máquinas deben ser monitorizadas para determinar si están sanas o a punto de fallar.
La supervisión del estado de la máquina, o Condition Monitoring, recopila datos sobre el rendimiento de la máquina a través de sensores, que suelen medir la vibración general. Si se detecta una firma de vibración anormal, el equipo de mantenimiento sabe que algo va mal y puede investigar el activo. Cuando la gente piensa en PdM, suele centrarse en qué tipo de tecnología puede detectar posibles fallos lo antes posible, para poder realizar el mantenimiento entre la detección y el fallo de forma segura y planificada.
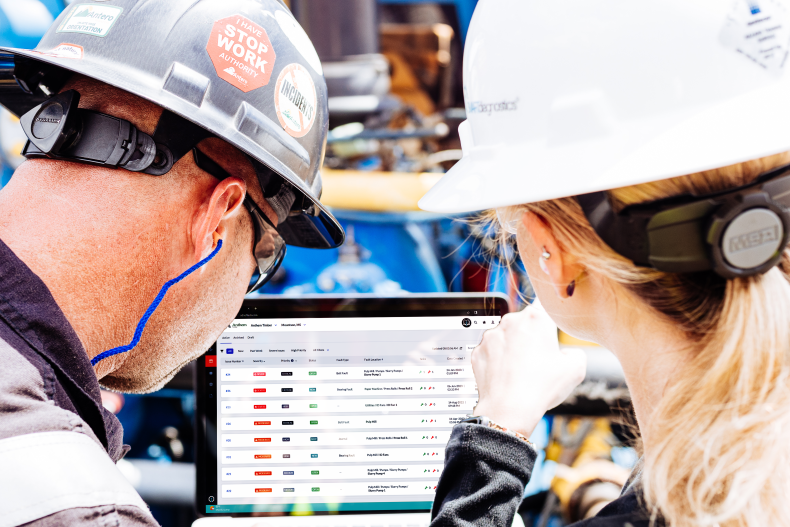
La monitorización de estado basada en rutas sigue siendo habitual, por lo que los jefes de mantenimiento trabajan con un esbozo aproximado del estado de la máquina, dibujado con sólo unos pocos puntos de datos como material de referencia. Si la recopilación de datos basada en rutas solo se realiza mensual o trimestralmente, pueden surgir tendencias falsas que lleven a los equipos de mantenimiento en la dirección equivocada.
Uno de los principales problemas de la PdM es que a menudo se basa en datos erróneos o incompletos.
Medición de la salud de las máquinas mediante OEE
Independientemente del enfoque que adopte el fabricante en materia de mantenimiento, la mayoría de las empresas utilizan la eficacia general de los equipos (OEE) como principal referencia para evaluar el estado de los activos y, por extensión, el estado general de la planta.
Esto no es del todo erróneo, pero tampoco es del todo correcto.
La OEE mide el rendimiento mecánico, pero en cierto modo es una medida autolimitante. En general, la OEE indica el rendimiento de la planta en las condiciones de funcionamiento actuales. Se pueden conseguir mejoras en el tiempo de actividad de los activos, el rendimiento y la calidad de la producción, pero a menudo una mejora en una de estas áreas se consigue a expensas de otra.
Esto no tiene por qué ser así -la OEE puede mejorarse de forma real y efectiva más allá de las capacidades actuales de su planta, y puede respaldar la mejora de otros KPI operativos-, pero los enfoques tradicionales de la gestión del estado de las máquinas no permitirán que su planta alcance todo su potencial ni le diferenciarán de la competencia.
Centrarse únicamente en la OEE también ignora otros factores operativos críticos.
¿Qué falla en los enfoques tradicionales de la gestión de la salud de las máquinas?
El mantenimiento preventivo se basa en la idea de que las máquinas se desgastan de forma previsible durante largos periodos de tiempo. El mantenimiento predictivo sostiene que las máquinas pueden fallar en cualquier momento, por lo que debemos estar constantemente alerta.
Ambas teorías son erróneas.
Los fallos de los equipos no son siempre predecibles, pero los acontecimientos que los provocan no son aleatorios, sino sistémicos. Y como son sistémicos, pueden evitarse casi por completo.
En comparación con el mantenimiento reactivo...
- El mantenimiento preventivo cuesta un 28% menos
- El mantenimiento predictivo cuesta un 50% menos
El camino hacia la optimización de la salud de las máquinas
Los fabricantes sienten la presión de subirse al tren de la Industria 4.0 y la tecnología del Internet Industrial de las Cosas (IIoT), pero la implantación práctica de esta tecnología aún no se ha producido en la mayoría de los casos. Hay un gran número de retos que se interponen en el camino: encajar soluciones que se solapan o compiten entre sí, negociar el equilibrio entre las iniciativas de la planta y las de la empresa, conciliar los procesos probados con las tecnologías innovadoras y calcular los plazos y los gastos de actualización de la infraestructura existente.
Una fabricación más inteligente comienza con la optimización del estado de las máquinas.
Optimización de la salud de las máquinas: ¿Por dónde empezar?
Los fabricantes que estén listos para adoptar la transformación digital deben comenzar con una iniciativa que ofrezca la mayor probabilidad de mejora del rendimiento y un retorno de la inversión a corto plazo. Por ello, la salud de las máquinas es una de las principales candidatas debido a su impacto en los KPI de toda la empresa.
Recuerde: los fallos de los equipos no son predecibles ni aleatorios. En la gran mayoría de los casos, es sistémico, causado por condiciones y comportamientos evitables que provocan daños innecesarios en la máquina y un rendimiento inferior al óptimo en su planta. Los errores de instalación, las intervenciones incoherentes de los operarios y el mantenimiento inadecuado son cosas que puede controlar si es capaz de rastrearlas, identificarlas y eliminarlas.
El camino hacia la optimización de la salud de las máquinas incluye algunos hitos importantes:
- Recopilación de datos críticos
- Resolver los primeros problemas mediante la correlación
- Introducción al análisis predictivo
- Establecimiento de procedimientos operativos normalizados para un rendimiento óptimo
- Utilizar el aprendizaje automático para acelerar el rendimiento
- Automatizar la intervención manual
Recopilación de datos para optimizar el estado de las máquinas
La supervisión de las vibraciones suele ser el punto de partida y de llegada de la recopilación de datos de PdM, pero es sólo el principio de un enfoque centrado en la optimización de la salud de las máquinas. De alguna manera, hay que medir la salud de las máquinas, y los sensores son la forma ideal de hacerlo.
Cuando la gente habla de monitorización de estado, a menudo sigue pensando en la recogida de datos basada en rutas. Antes pagábamos a personas para que fueran de un lado a otro recogiendo mensualmente datos de sensores de vibración. Gracias a los avances tecnológicos, ahora tiene mucho más sentido equipar las máquinas con sensores inalámbricos de bajo coste que puedan transmitir datos continuamente a una ubicación centralizada.
Un sistema distribuido de supervisión continua del estado de los activos que proporcione cientos de puntos de datos por hora es fundamental para poder detectar las condiciones sistémicas que causan daños. El tipo de datos que proporciona también es una consideración clave. Es una excelente idea supervisar valores individuales como la aceleración máxima, la vibración general y la temperatura, pero las tendencias de valores individuales sólo mostrarán que hay un problema sin proporcionar información sobre cuál podría ser ese problema.
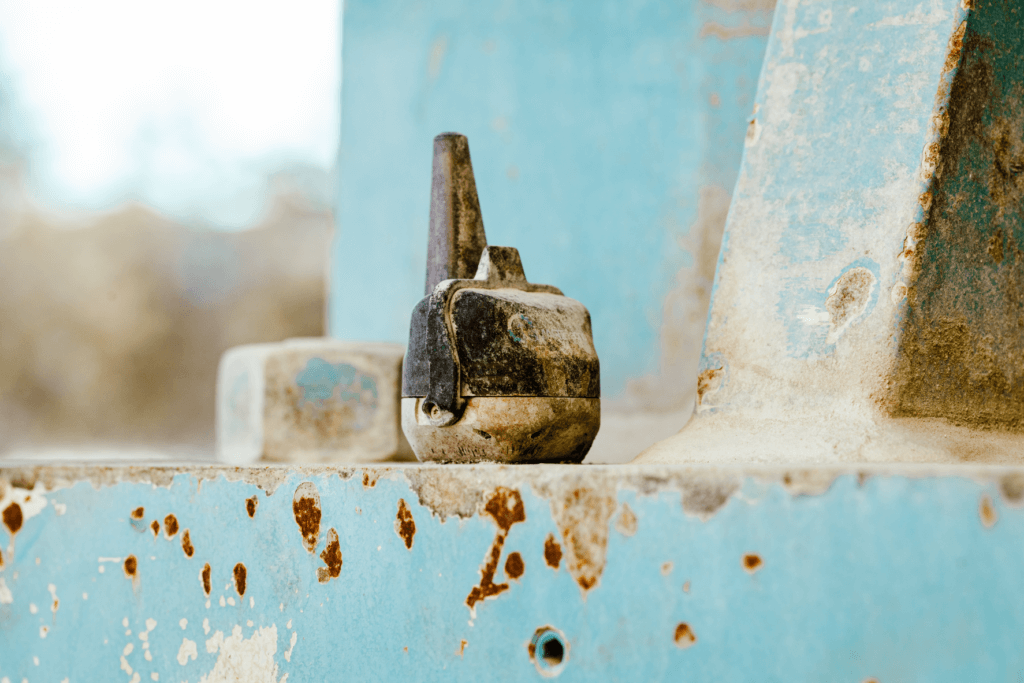
Es posible que invierta mucho tiempo y dinero en una sola máquina antes de poder identificar la raíz del problema.
Hay más datos. Los sensores SMARTdiagnostics envían una forma de onda temporal, no un pico ni una media. A continuación, el software muestra esos datos en un espectro de frecuencias. Los distintos tipos de fallos mecánicos se ven completamente diferentes en el espectro de frecuencias, pero se verían casi idénticos en el gráfico general de vibraciones.
A medida que este campo ha ido madurando, ahora se utilizan muchas otras herramientas para caracterizar de forma exhaustiva el estado de las máquinas. No se trata sólo de simples máquinas rotativas, sino de muchos otros tipos de equipos, desde los que funcionan de forma intermitente, como las líneas de transformación de las plantas de envasado, hasta los robots y ascensores del montaje de automóviles.
Algunos fabricantes han improvisado varios sistemas de sensores para intentar comprender mejor el estado general de la máquina, pero el mejor enfoque es el que aprovecha una infraestructura de red común para conectar todos los sensores bajo un mismo paraguas, lo que simplifica enormemente el mantenimiento de los sensores y la red, los gastos generales y la gestión de los datos.
La recopilación de datos mediante la tecnología adecuada es un primer paso importante, pero los sensores y los datos no hacen aflorar por sí solos un plan de acción.
Resolver problemas con la optimización del estado de las máquinas
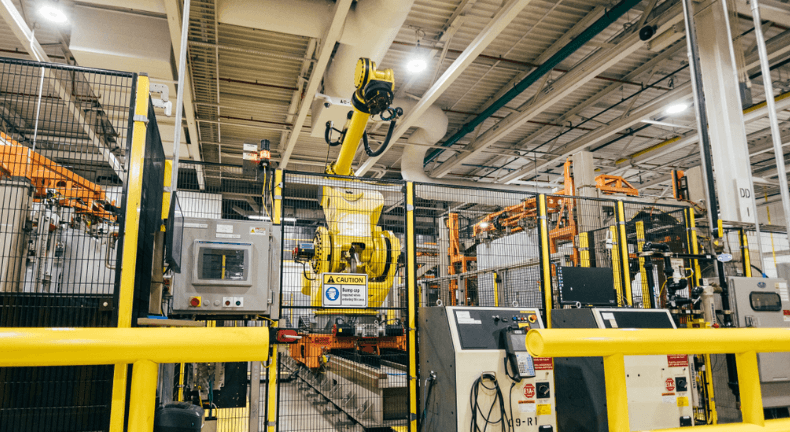
Con el fin de crear un plan de acción para optimizar la salud de la máquina, los datos recogidos de su red de sensores inteligentes deben correlacionarse con los datos sobre las condiciones de la planta y las personas que interactúan con su equipo. De este modo, sabremos qué condiciones provocan daños y qué componentes de la máquina contribuyen a ellos. A continuación, podemos diseñar esas condiciones perjudiciales fuera del proceso. Esto prolonga la vida útil de la máquina, aumenta el tiempo de funcionamiento, reduce los costes y mejora la eficiencia energética.
Este es el punto en el que otros proveedores de soluciones para la salud de las máquinas podrían empezar a hablar de aplicar la inteligencia artificial a los problemas de los activos. La IA es apasionante y está llena de posibilidades, pero al principio resulta mucho más práctico captar los conocimientos de los empleados de la planta y adaptarlos a la lógica y los flujos de trabajo digitales.
Muchos fabricantes piensan que podrían necesitarse semanas, meses o incluso años de monitorización para establecer una línea de base útil. Con la tecnología de sensores de SMARTdiagnostics, podemos recopilar miles de puntos de datos en cuestión de horas y ponernos manos a la obra. Identificar los fallos se convierte en una tarea fácil muy rápidamente, y detectar los fallos equivale a un rápido retorno de la inversión y a una historia de éxito en torno a la que todo el mundo puede unirse.
Las optimizaciones tempranas de la salud de la máquina son posibles.
Cuando se empiezan a colocar sensores en cada pieza de un equipo importante, la avalancha de datos resultante puede resultar abrumadora muy rápidamente. No es raro tener decenas de miles de indicadores en una sola planta. Para que este tipo de sistema sea escalable, el primer paso es la autoalarma, de modo que se pueda notificar a las personas adecuadas cuando algo está fuera de especificaciones.
Cuando llegue a este punto, enhorabuena: ha empezado a utilizar con éxito un sistema IIoT para facilitar los objetivos de un programa de mantenimiento predictivo. El viaje hacia la optimización de la salud de la máquina no termina aquí. Podemos hacer mucho más para ser aún más inteligentes.
Análisis predictivo y salud de las máquinas
La implantación de herramientas de análisis predictivo es el punto en el que los fabricantes con visión de futuro empiezan a dejar atrás la PdM tradicional y a avanzar hacia una verdadera optimización del estado de las máquinas.
Los datos sobre la salud de las máquinas llevan décadas recopilándose y estudiándose, por lo que muchos fenómenos ya se conocen bien. También disponemos de billones de nuestros propios datos sobre decenas de miles de activos para complementar este conocimiento global. Con toda esta información, hemos creado algoritmos que pueden analizar los datos procedentes de una máquina, compararlos con miles de firmas de fallos conocidas y predecir rápidamente qué condiciones de fallo pueden estar presentes en esa máquina.
En esta fase del viaje, uno de los objetivos principales es profundizar en el conocimiento de la salud de sus equipos mediante la comprensión de la física de cada máquina y el análisis de la causa raíz. Por ejemplo, puede aprender cómo el cambio de presión en la entrada de una bomba influye en otras variables como la vibración y la temperatura. El modelado y la optimización en esta fase se centran en encontrar las condiciones de funcionamiento que consuman menos energía y minimicen el desgaste de la máquina y los componentes sin dejar de cumplir los objetivos de producción.
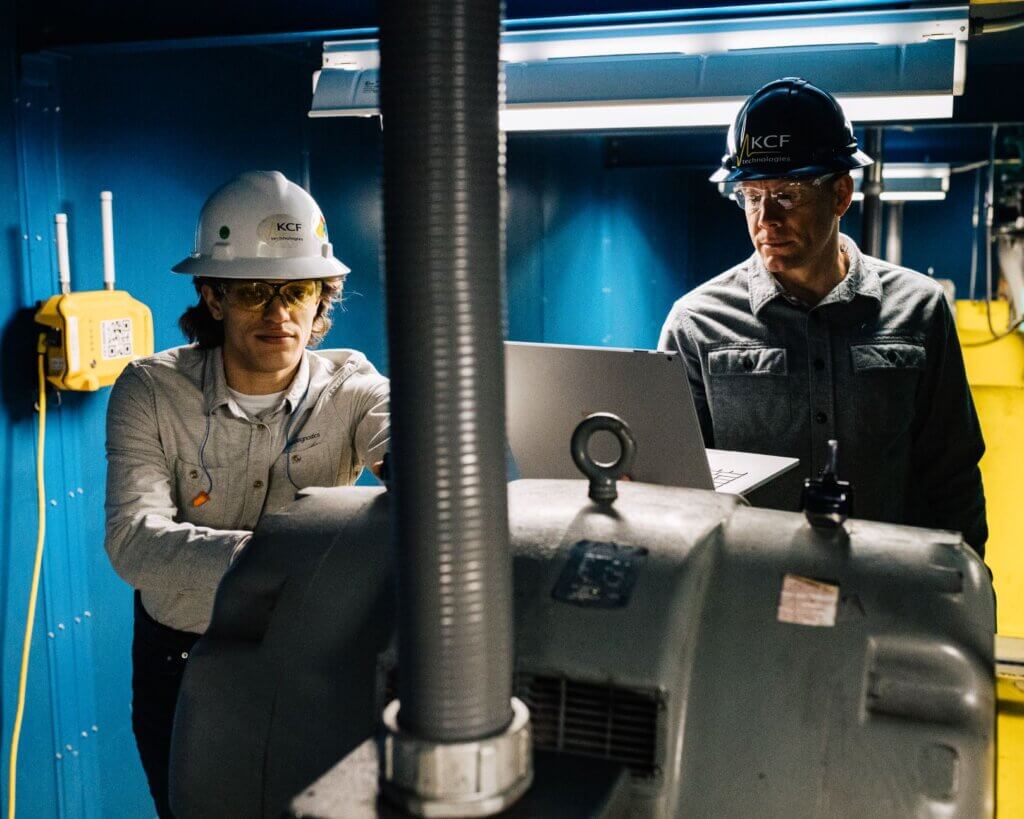
Optimización de la salud de la máquina
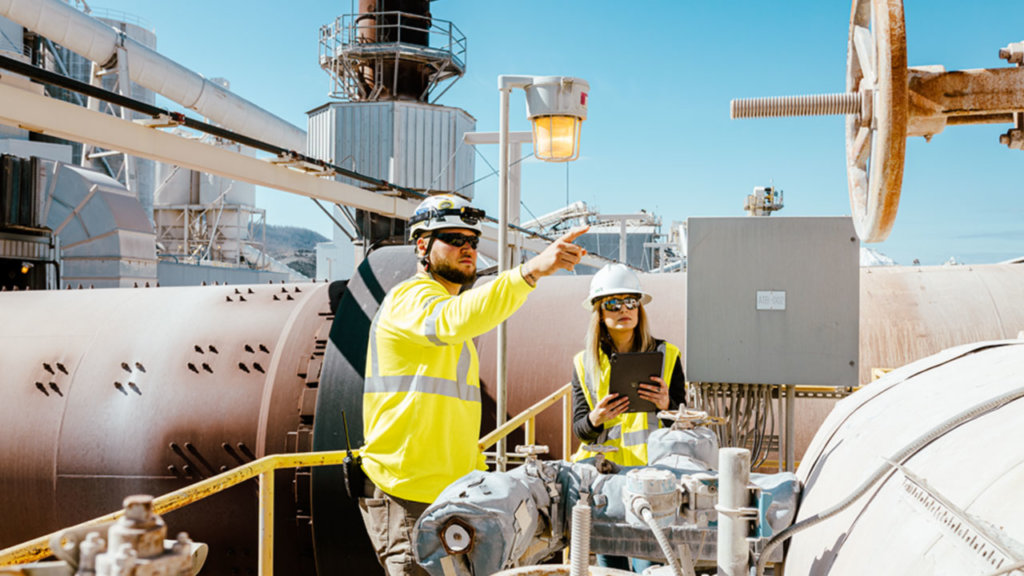
Las etapas finales del proceso de optimización del estado de las máquinas son las que aportarán más valor a sus inversiones y le situarán por delante de sus competidores. Una vez que se han identificado las condiciones perjudiciales y se han encontrado las condiciones de funcionamiento ideales, el siguiente paso es establecer procedimientos operativos normalizados para garantizar que las máquinas funcionen siempre de la mejor manera posible. Esto implica una serie de factores que no son sólo OEE: la salud de la máquina, los costes de energía, los costes de inactividad, la calidad, la mano de obra, y así sucesivamente. La definición de éxito incluye tanto factores mecánicos como empresariales.
¿Qué acciones harán que la empresa sea más rentable?
Una vez conocidas las condiciones de la planta, podemos utilizar el aprendizaje automático para aplicar métodos computacionales avanzados que determinen la mejor forma de hacer funcionar una máquina. Esto parece una optimización continua sobre la marcha -basada en las condiciones actuales- para maximizar el valor.
El último paso es la automatización, eliminando en la medida de lo posible el elemento humano de los ajustes operativos. Cuando esto se aplica de forma completa y precisa, los algoritmos inteligentes producidos por el proceso de aprendizaje automático pueden controlar directamente su equipo, por ejemplo, ajustando sobre la marcha la velocidad de varias bombas paralelas en un sistema para minimizar el consumo total de energía, maximizar la producción o minimizar los daños en la máquina.
El impacto de la optimización del estado de las máquinas
Dependiendo de su enfoque actual del mantenimiento, su planta podría ahorrar hasta un 67% de los costes de salud de las máquinas adoptando un enfoque centrado en la optimización de la gestión de la salud de las máquinas.
Cuanto más avance en la optimización del estado de sus máquinas, mayor será el retorno de la inversión en IIoT y más se diferenciará de sus competidores.
Mediante la convergencia de personas y tecnología, podemos resolver problemas de activos de forma permanente y transformar la industria.
Los socios de KCF suelen multiplicar por 10 el retorno de la inversión en optimización del estado de las máquinas.
Cómo empezar a optimizar la salud de las máquinas
Una solución eficaz para optimizar el estado de las máquinas tiene una serie de componentes críticos. Estos componentes deben estar estrechamente integrados, por lo que se recomienda una solución completa que favorezca el rendimiento del sistema, la facilidad de uso y la rentabilidad. La integración personalizada, la limpieza de datos y la interoperabilidad pueden llevar años. Las soluciones de pila completa reducen drásticamente el tiempo de obtención de valor.
Para empezar, necesitarás:
- Una plataforma de IoT que incluye una gama de sensores, permite conexiones con los PLC existentes y ofrece soluciones específicas para cada aplicación.
- Análisis avanzados para la gestión estratégica de activos. De un vistazo, debería ser capaz de conocer el coste actual neto de un determinado estado operativo.
- Software empresarial que proporciona diagnósticos automatizados y el estado de salud de las máquinas en tiempo real. Debe ofrecer personalización basada en roles, eliminando la necesidad de múltiples soluciones de análisis.
- Un socio de implantación que pueda ofrecer una serie de servicios, como formación y educación, para ayudar a superar la razón número uno por la que fracasan las implantaciones de la Industria 4.0: la falta de adopción.
KCF existe para elevar a las personas y resolver los problemas de la Industria 4.0. Imaginamos un mundo en el que nuestros clientes tengan cero lesiones, cero residuos y cero fallos de activos. Conectamos eficazmente tecnologías de vanguardia con soluciones reales que mejoran las instalaciones industriales y las comunidades a las que sirven para un futuro sostenible.
"KCF no se limita a vender un producto y marcharse. Trabajan con usted para supervisar su maquinaria".
- Responsable de fiabilidad
Póngase en contacto con nosotros
El camino hacia la verdadera salud de las máquinas comienza con una conversación. Póngase en contacto con nosotros hoy mismo para obtener más información sobre cómo eliminar la causa principal de los fallos de sus activos.