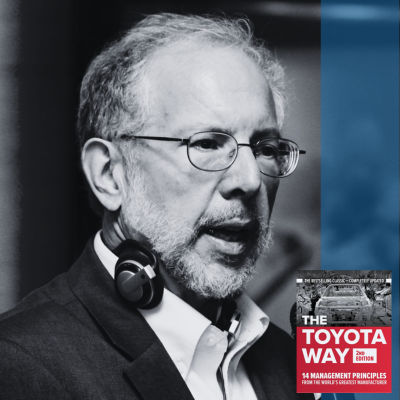
Dr. Jeffrey Liker, University of Michigan, Liker Lean Advisors
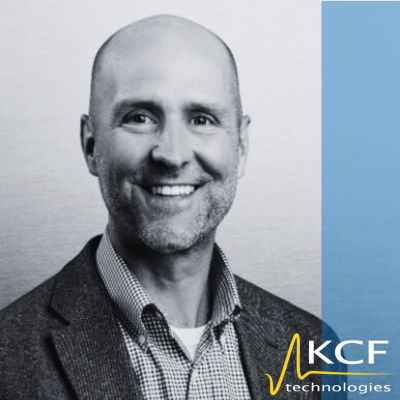
Dr. Jeremy Frank, CEO and Founder, KCF Technologies, Inc.
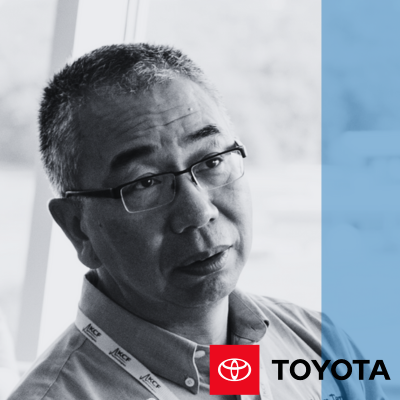
Joe Li, Manager, Toyota North America
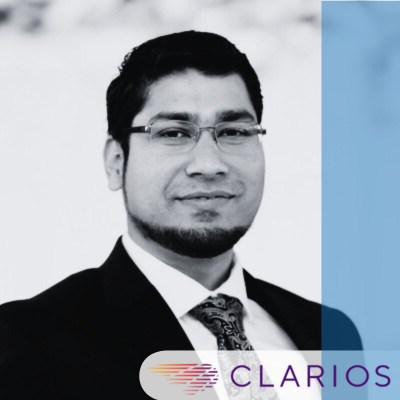
Yahya Khan, Senior Reliability Engineer, Clarios Corporation
Table of Contents
Introduction
Walk into a Toyota plant and the first overwhelming image is paper on walls and easels everywhere. Color coded charts, graphs, figures with places for data seem to fill every nook and cranny. Andon lights are firing off constantly playing music and team leaders come running to respond. The most common or biggest problems of each shift are worked on by teams at the front line using disciplined problem solving.
For automated processes, skilled maintenance team members perform detailed preventative maintenance for one full shift everyday, also guided by visual reminders on charts and graphs. The performance of each line is vividly displayed on huge computer screens updated automatically in real time and the numbers are remarkable—making what was planned for the shift on time, without vehicles pulled off line for quality problems, 96% or more of the time. Even old robots that many companies would replace are running over 99% of the time.
What is missing, or at least very limited, are the computer displays that have become popular in the digitization of the factories. Toyota believes strongly in the power of visual management to highlight gaps between standard and actual and people’s brains to close those gaps. In the Toyota plant in the United Kingdom they operate with the motto: “Use brains not money.”
The lean movement views the Toyota Production System as a benchmark for best practice in manufacturing and even today large companies typically have departments of continuous improvement experts roaming the plants, leading improvement workshops, and preaching the virtues of lean. In the meantime, we have another movement sweeping manufacturing in the 21st century—Industry 4.0. This is a movement to digitize the factory promising a revolution that will make yesterday’s manual methods obsolete, and companies that do not get on board also obsolete.
Why does Toyota persist in using legacy manual methods with paper? Why isn’t this manufacturing leader leading the way with digitization? And can these movements work together—lean and digitization?
We think the answer is yes they can, but it requires stepping away from the orthodoxy of lean and the bold, if sometimes arrogant, promises of “solutions” provided by the digital factory. It requires understanding the reality of the types of problems that millions face in typical days on the shop floor and how those problems can best be solved. It requires being realistic about the unlikely visions of dark factories with most people gone, leaving only engineers who develop the automated systems. Most important, it requires valuing humans and our endless capacity for creative thinking and innovative problem solving. As we will see, Toyota is indeed cautiously stepping into the world of the Internet of Things.
The Nature of Problems and Problem Solving: Predictive versus Adaptive
We see too often lean advocates and IT people talking past each other about the power and usefulness of advanced digital technologies. The IT people claim their technology offers “solutions” that:
- Predict where problems are likely to occur.
- Immediately flag problems that have just occurred.
- Closed-loop control systems automatically make adjustments to equipment to fix the problem.
- In cases where people are involved provide detailed guidance, perhaps through augmented reality, to walk even the novice through a recipe to fix the problems.
- Provide real-time data on performance relative to targets so gaps can be quickly and efficiently closed.
Meanwhile, lean advocates caution that the real world is far more complex than that and people, with our immense problem-solving capability, still need to be in the center:
- In the highly variable and uncertain world of manufacturing novel problems occur regularly, many of which have no known recipe.
- The automation that is supposed to fix the machine itself breaks down frequently and needs to be fixed.
- The more complex the technology the more likely it will break down in unpredictable ways.
- People with our unparalleled brain capacity and finely tuned senses can predict that a problem will occur and find creative ways to solve the problems outperforming even the most advanced AI systems.
- Often simple, inexpensive solutions can be very effective and save a lot of money.
- People are visual creatures and to be most effective need simple displays of actual versus standard highlighting what is green, yellow and red at a glance.
These seemingly conflicting world views are actually focusing on two different problem solving scenarios—predictive versus adaptive. Predictive problem solving are cases where the problem can be easily diagnosed and the solutions that will work predicted in advance of actually taking action. Often these solutions are based on engineering knowledge expressed in mathematical models. Essentially through prior knowledge the people or system are trying to predict the future.
Adaptive problem solving are cases where the problem is vague, the solution is not clear, and it takes creative thinking and trials organized as experiments to learn our way to the solution. For these types of problems intimate knowledge of the conditions of failure, and past experience with similar problems, can be a great asset. People on the front-line who live with the equipment and processes have this knowledge.
Predictive Problem Solving | Adaptive Problem Solving | |
Problem Definition | Clear | Requires Learning |
Solution | Well Understood | Requires Learning |
Problem Solvers | Experts or Authority | Stakeholders |
Process | Efficient Decision Making | Act Experimentally |
Timeline | Results ASAP | Time Needed to Follow Process |
Expectations | Fix the Problem | Achieve Targets and Develop People |
Attitude | Confidence and Skill | Curiosity |
Figure 1: Comparing Predictive and Adaptive Problem Solving
Table 1, adapted from O’Malley and Cebula, contrasts these two problem solving scenarios. If we labeled the “Predictive Problem Solving” column as the Digital advocates view of the world and the “Adaptive Problem Solving” column as the lean view of the world we would have a pretty good fit.
Who is right? Is it possible both are? There are many problems that can be solved predictively by those with expert knowledge, or from computer algorithms, though far fewer than the digital thinkers suggest in their pitches for digitalization, and also many problems that require pure adaptation and learning by stakeholders experimenting, though fewer than the lean advocates suggest.
Let’s consider a case example of a class of technologies that use sensors to measure vibration, temperature, current, load, and time and have the following characteristics:
- There is well established engineering science on how different pieces of equipment function optimally that can use these indicators to predict, detect and sometimes even diagnose problems.
- It is not so much AI as well understood engineering equations.
- When coupled with sensors and the Internet of Things, the analysis provides information that is not always intuitive to most operating personnel in factories and the insights are often surprising.
- If used effectively by well-trained people it can lead to large increases in equipment performance very quickly.
- In many, maybe most cases, the insights from the analysis require people skilled in adaptive problem solving to find the solutions that will work.
The Toyota Production System for Equipment Health
Equipment maintenance appears to be right in the wheelhouse of the Industry 4.0 advocates. Industry 4.0 forecasts a world where repetitive manual processes are at some point fully replaced by automated equipment. In a sense this is an engineering paradise where the more predictable and consistent programmable automation takes over for less consistent human operators who have personal needs. The catch is that most of maintenance is done by those unpredictable humans who need deep knowledge, high levels of technical and problem-solving skill, and creativity to identify the cause of a breakdown and figure out how to do the repair.
The Toyota Production System is centered on people and usually applied to repetitive manual work, like that on an auto assembly line. Just-in-Time is about working toward a high value-added flow of product to the customer, without waste in the process. In the plant this requires getting the right materials at the right time in the right amount to the team members who do the work.
[digitization] requires valuing humans and our endless capacity for creative thinking and innovative problem solving.
Since there is always variation in various parts of the system, including the human, things will invariably be out of standard so corrective action is needed. Jidoka, the second pillar, addresses out of standard conditions. It began with Sakichi Toyoda who founded the original loom works that led to Toyota Motor Company. He ultimately invented a fully automated loom. Along the way he added physical sensors that stopped the loom when a single thread broke and signaled there was a problem by a flag popping up. Later this led to identifying potential failure modes and designing into equipment sensors to detect out of standard conditions and stop the equipment when certain thresholds were reached. For manual processes team members pulled the “andon” cord when out of standard condition were noticed which could lead to line stops.
To have a consistent flow of the product and its constituent parts you need stable processes which requires Standardization. There are standards for product design, standards for process design, and standardized work for people performing manual tasks.
The reason People are in the center is they not only perform the work, but are expected to continuously improve the system, including reacting to out of standard conditions with creative problem solving. The ownership and responsibility is at the front-line and work groups comprised of team members, team leaders, and group leaders are responsible for achieving aggressive performance targets and perform some of the simpler preventative maintenance.[1]
So how does this apply to equipment maintenance? The goal is to have healthy equipment that is ready and able to produce exactly the parts needed when they are needed with perfect quality.
Just-in-time (JIT) maintenance means the right maintenance at the right time, neither too early or too late. Preventative maintenance is critical to Toyota’s high level of operational availability of equipment, but one could argue that, without the right data, it is often performed too early. That is, a broad set of maintenance procedures are done whether the equipment needs it or not to run at a high level Just-In-Case it might otherwise lead to equipment breakdown.
Another approach to maintenance is to wait for it to fail, like the original sensor on the loom when a thread broke. This reactive approach requires quick response to first contain the problem and get the equipment running and then solve the problem at the root cause so it is unlikely to happen again. Arguably this is too late.
Toyota is increasingly moving toward the world of predictive maintenance. They wish to know in advance for a particular machine that it was going to fail in a specific way and take corrective action before the problem occurs.
There are advanced methods, through the “Internet of Things” and analytics for example, that are increasing what we can predict. Unfortunately, any digital system today can only measure certain variables, there are limits to the analytical models, and because most factory systems are complex, unique and interconnected, there are a limited set of problems that can be managed purely on a predictive basis. Therefore, we still need people to find the root cause and develop a creative solution to solve the problem. Often solving the problem is a matter of trying things, experimenting, that is, adaptive problem solving.
Intelligent Sensors Case Examples
KCF Technologies is one technology supplier that believes in the power of digital information to enhance, not replace creative problem solving by people. Their core technology is advanced sensors, with the computer power of advanced analytics. Many of the equations that they use to predict equipment failure can be traced back decades to fundamental engineering science. When there is an analytical equation that effectively predicts it is not necessary to have AI systems scouring big data to find patterns. You simply plug the right numbers into the right mathematical model. Toyota is one of their clients.
Toyota Plant Example
Toyota has had great success with KCF technology for both predictive and adaptive problems.
As a predictive example, sensors were installed on the drive motors of conveyors and analysis of vibration patterns was able to predict impending failure. When the vibrations exceed thresholds, the software triggers a text and email. Team leaders and members follow up immediately and generally determine they need to schedule replacement of the motor by maintenance. As the plant expanded it use, this type of predictive maintenance action played out hundreds of times over thousands of pieces of critical plant machinery, and built confidence in the system with the team members.
Going beyond predictive maintenance, the team members also realized many cases where the predictive data enabled them to make adaptive improvements to system configurations and standard operating procedures. One example of this was in the paint shop. The KCF data consistently showed imbalance on the paint shop exhaust fans, related to build-up of paint on the fan blades from the process. This data enabled the team members to assess and update the frequency and methods for proactively cleaning the fan blades, thus eliminating the imbalance problem that would have otherwise led to premature failure of the fan support bearings and the motor and structure. The solution was not obvious immediately and took a more in-depth problem solving process with some trial and error.
There are even examples of a combination of predictive and adaptive. An example of this was at a Toyota facility that stamps out steel parts. This was an older plant with aging equipment. Toward the end of 2022, they had a debilitating equipment failure on a sub-system of the stamping press. This resulted in significant hours of downtime, substantial stress on the team members, and considerable capital expenditures. The team was caught off guard by unplanned failures and consequently began a collaboration with KCF in April 2023 to manage the health of their assets more proactively.
Simply adjusting their already robust maintenance practices would not be sufficient to address the particular problems that come with maintaining older equipment. Toyota’s team determined they needed a combination of advanced technology and technical expertise. They formed an interdisciplinary team of manufacturing engineers, corporate and site maintenance staff, and KCF’s analysts to figure out the best way to extend the press’s operational life by an additional two years.
The team deployed a series of “IoT HUBS”, which are specifically designed to capture and process data on complex, intermittent machinery like stamping presses. The sensors were installed on a press line to test its efficacy and data indicated severe deterioration in several key components of the press, though the solutions were not obvious. Through a process of going to see, identifying several key causes of failure, and testing various ideas the team came up with an alternative for the hydraulic brake pump system—which was so out of date that replacement parts were no longer available—that resolved a number of the issues. The technology also was also able to anticipate the need to replace the main motor bearings, which predictably failed 3 months later.
But they found even this level of problem solving was not enough. The slide adjust assembly required a more intensive problem solving approach that built upon the foundational current and vibration data supplied by the sensors. The team noticed a change in the waveform that looked like it could be a rotor bar fault in the making and shortly after observed a spike in vibration on the gearbox. As is often the case, there was not much downtime to inspect the issue, and the slide adjust was hard to access. A cross-functional team identified possible checks and ranked them from easiest to hardest, creating a feasible and optimized proactive maintenance plan, supported by remote continuous online monitoring until the planned downtime and scheduled inspection several months later.
Conclusion
The lean movement started with its model, the Toyota Production System. At the core of lean are people at the gemba, where the work is done, who respond to abnormalities highlighted by the system.
Industry 4.0 is a vision for automated factories run largely by computers that plan and decide what to do and when. Presumably problems are solved by the computer systems, often with the help of advanced AI and analytical systems.
There is a different type of problem solving, adaptive, in which the problem cannot be easily defined and solutions are not obvious. Adaptive problem solving requires people at the gemba who with their senses can find the root cause and solve the problem, often through a series of experiments.
We have given examples with one type of technology, offered by KCF Technologies, of sensors and systems based on engineering equations that can predict when equipment will fail and often provide solutions of the predictive variety. “Often” is not always. KCF looked at data from customers and estimated that roughly 50 percent of problems were predictive and 50 required adaptive problem solving. Their experience also suggests that over time, as the low-hanging fruit is picked, an increasing number of the problems require adaptive problem solving.
We recommend that manufacturing companies that have not invested heavily in the problem-solving capabilities of their front-line staff should do so in parallel with introducing advanced digital technologies. This may mean going slower in introducing the technologies, including piloting individual modules before widespread deployment. Some companies are partnering lean practitioners with internal IT experts with great results, much as we saw in the collaboration between Toyota plant experts and KCF technology experts. We suspect that over time automation and digital technologies will lead to fewer people in the factories doing manual work. But there will be an even greater need for thinking people at the gemba solving problems as they are identified by software and people. In this way the technology supports the people and process.
[1] Jeffrey K. Liker, The Toyota Way, second edition, McGraw Hill, 2020.