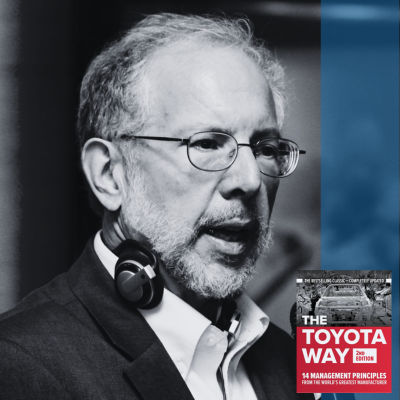
Dr. Jeffrey Liker, Universidad de Michigan, Liker Lean Advisors
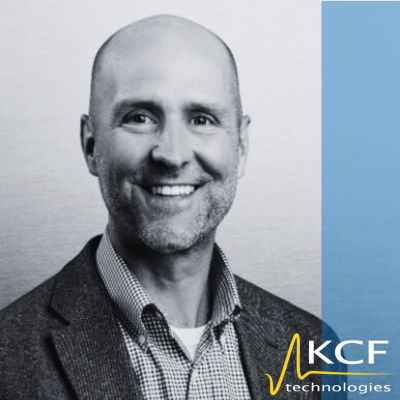
Dr. Jeremy Frank, director general y fundador de KCF Technologies, Inc.
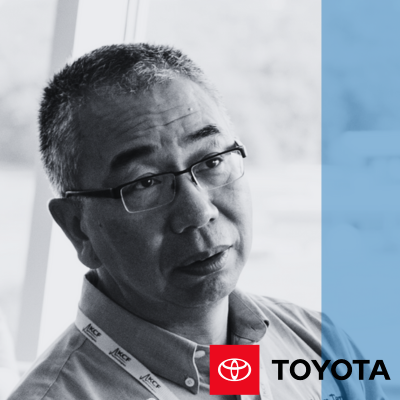
Joe Li, Director, Toyota Norteamérica
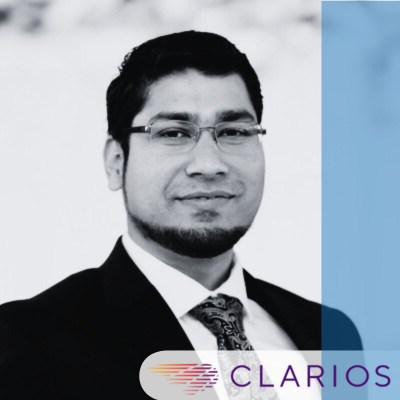
Yahya Khan, Ingeniero Superior de Fiabilidad, Clarios Corporation
Índice
Introducción
Al entrar en una planta de Toyota, la primera imagen abrumadora es la de papel en las paredes y caballetes por todas partes. Tablas codificadas por colores, gráficos, figuras con lugares para datos parecen llenar todos los rincones. Las luces de Andon no paran de sonar y los jefes de equipo vienen corriendo a responder. Los problemas más comunes o más grandes de cada turno son resueltos por equipos en primera línea mediante una disciplinada resolución de problemas.
En los procesos automatizados, los miembros del equipo de mantenimiento llevan a cabo un mantenimiento preventivo detallado para un turno completo cada día, también guiados por recordatorios visuales en tablas y gráficos. El rendimiento de cada línea se visualiza vívidamente en enormes pantallas de ordenador que se actualizan automáticamente en tiempo real, y las cifras son notables: el 96% o más de las veces se fabrica a tiempo lo previsto para el turno, sin retirar vehículos de la línea por problemas de calidad. Incluso los viejos robots que muchas empresas sustituirían funcionan más del 99% de las veces.
Lo que falta, o al menos es muy limitado, son las pantallas de ordenador que se han popularizado en la digitalización de las fábricas. Toyota cree firmemente en el poder de la gestión visual para poner de manifiesto las diferencias entre lo estándar y lo real, y en el cerebro de las personas para cerrar esas brechas. En la planta de Toyota en el Reino Unido funcionan con el lema: "Usa cerebros, no dinero".
El movimiento lean considera el Sistema de Producción Toyota como una referencia de buenas prácticas en la fabricación y, aún hoy, las grandes empresas suelen tener departamentos de expertos en mejora continua que recorren las plantas, dirigen talleres de mejora y predican las virtudes del lean. Entretanto, hay otro movimiento que está arrasando en la industria manufacturera del siglo XXI: la Industria 4.0. Se trata de un movimiento para digitalizar la producción. Se trata de un movimiento para digitalizar la fábrica que promete una revolución que dejará obsoletos los métodos manuales de ayer, y obsoletas a las empresas que no se suban a bordo.
¿Por qué Toyota persiste en utilizar métodos manuales heredados con papel? ¿Por qué este líder manufacturero no lidera la digitalización? ¿Pueden ir de la mano estos dos movimientos?
Creemos que la respuesta es sí, pero para ello es necesario alejarse de la ortodoxia del lean y de las audaces, aunque a veces arrogantes, promesas de "soluciones" que ofrece la fábrica digital. Requiere comprender la realidad de los tipos de problemas a los que se enfrentan millones de personas en los días normales de trabajo y la mejor forma de resolverlos. Requiere ser realista sobre las improbables visiones de fábricas oscuras en las que la mayoría de las personas desaparecen, dejando sólo a los ingenieros que desarrollan los sistemas automatizados. Y, lo que es más importante, requiere valorar a los seres humanos y nuestra infinita capacidad para el pensamiento creativo y la resolución innovadora de problemas. Como veremos, Toyota está entrando con cautela en el mundo del Internet de las cosas.
La naturaleza de los problemas y la resolución de problemas: Predictivo frente a adaptativo
Con demasiada frecuencia, los defensores de la tecnología lean y los informáticos no se ponen de acuerdo sobre el poder y la utilidad de las tecnologías digitales avanzadas. Los informáticos afirman que su tecnología ofrece "soluciones" que:
- Predecir dónde es probable que se produzcan problemas.
- Señale inmediatamente los problemas que se acaban de producir.
- Los sistemas de control de bucle cerrado realizan automáticamente ajustes en los equipos para solucionar el problema.
- En los casos en los que hay personas implicadas, proporcione orientación detallada, quizá mediante realidad aumentada, para guiar incluso al más novato a través de una receta para solucionar los problemas.
- Proporcionar datos en tiempo real sobre el rendimiento en relación con los objetivos, de modo que las deficiencias puedan subsanarse de forma rápida y eficaz.
Mientras tanto, los defensores del lean advierten que el mundo real es mucho más complejo que eso y las personas, con nuestra inmensa capacidad para resolver problemas, seguimos necesitando estar en el centro:
- En el mundo altamente variable e incierto de la fabricación surgen con regularidad nuevos problemas, muchos de los cuales no tienen receta conocida.
- La automatización que debe arreglar la propia máquina se avería con frecuencia y hay que arreglarla.
- Cuanto más compleja es la tecnología, más probabilidades hay de que se estropee de forma impredecible.
- Las personas, con nuestra capacidad cerebral sin parangón y nuestros sentidos afinados, podemos predecir que se va a producir un problema y encontrar formas creativas de resolverlo superando incluso a los sistemas de IA más avanzados.
- A menudo, soluciones sencillas y baratas pueden ser muy eficaces y ahorrar mucho dinero.
- Las personas son criaturas visuales y, para ser más eficaces, necesitan visualizaciones sencillas de lo real frente a lo estándar que destaquen de un vistazo lo que es verde, amarillo y rojo.
Estas visiones del mundo aparentemente contradictorias se centran en realidad en dos escenarios diferentes de resolución de problemas: predictivo y adaptativo. La resolución de problemas predictiva es aquella en la que el problema puede diagnosticarse fácilmente y las soluciones que funcionarán pueden predecirse antes de pasar a la acción. A menudo, estas soluciones se basan en conocimientos de ingeniería expresados en modelos matemáticos. Esencialmente, a través del conocimiento previo, las personas o el sistema intentan predecir el futuro.
La resolución adaptativa de problemas son casos en los que el problema es impreciso, la solución no está clara y se necesita pensamiento creativo y pruebas organizadas como experimentos para aprender el camino hacia la solución. Para este tipo de problemas, el conocimiento íntimo de las condiciones de fallo y la experiencia pasada con problemas similares pueden ser una gran baza. Este conocimiento lo tienen las personas que trabajan en primera línea y conviven con los equipos y procesos.
Resolución predictiva de problemas | Resolución adaptativa de problemas | |
Definición del problema | Claro | Requiere aprendizaje |
Solución | Bien entendido | Requiere aprendizaje |
Resolver problemas | Expertos o autoridad | Partes interesadas |
Proceso | Toma de decisiones eficaz | Actuar experimentalmente |
Cronología | Resultados lo antes posible | Tiempo necesario para seguir el proceso |
Expectativas | Solucionar el problema | Lograr objetivos y desarrollar a las personas |
Actitud | Confianza y habilidad | Curiosidad |
Figura 1: Comparación de la resolución de problemas predictiva y adaptativa
La tabla 1, adaptada de O'Malley y Cebula, contrasta estos dos escenarios de resolución de problemas. Si etiquetáramos la columna "Resolución predictiva de problemas" como la visión del mundo de los defensores de Digital y la columna "Resolución adaptativa de problemas" como la visión lean del mundo, tendríamos un ajuste bastante bueno.
¿Quién tiene razón? ¿Es posible que ambos la tengan? Hay muchos problemas que pueden ser resueltos de forma predictiva por expertos o a partir de algoritmos informáticos, aunque muchos menos de los que sugieren los pensadores digitales en sus argumentos a favor de la digitalización, y también muchos problemas que requieren pura adaptación y aprendizaje por parte de los interesados que experimentan, aunque menos de los que sugieren los defensores del lean.
Veamos un ejemplo de una clase de tecnologías que utilizan sensores para medir la vibración, la temperatura, la corriente, la carga y el tiempo y tienen las siguientes características:
- Existe una ciencia de la ingeniería bien establecida sobre el funcionamiento óptimo de los distintos equipos que puede utilizar estos indicadores para predecir, detectar y, a veces, incluso diagnosticar problemas.
- No se trata tanto de IA como de ecuaciones de ingeniería bien entendidas.
- Cuando se combina con sensores y la Internet de los objetos, el análisis proporciona información que no siempre es intuitiva para la mayoría del personal de las fábricas, y los resultados suelen ser sorprendentes.
- Si se utiliza eficazmente por personas bien formadas, puede producir grandes aumentos en el rendimiento de los equipos con gran rapidez.
- En muchos casos, tal vez en la mayoría, las conclusiones del análisis exigen que personas expertas en la resolución adaptativa de problemas encuentren las soluciones que funcionarán.
El sistema de producción Toyota para la salud de los equipos
El mantenimiento de equipos parece estar en el punto de mira de los defensores de la Industria 4.0. La Industria 4.0 prevé un mundo en el que los procesos manuales repetitivos serán sustituidos en algún momento por equipos automatizados. En cierto sentido, se trata de un paraíso de la ingeniería en el que la automatización programable, más predecible y consistente, sustituye a los operadores humanos, menos consistentes y con necesidades personales. El problema es que la mayor parte del mantenimiento corre a cargo de esos humanos impredecibles que necesitan profundos conocimientos, altos niveles de habilidad técnica y de resolución de problemas, y creatividad para identificar la causa de una avería y averiguar cómo repararla.
El Sistema de Producción Toyota se centra en las personas y suele aplicarse al trabajo manual repetitivo, como el de una cadena de montaje de automóviles. Just-in-Time consiste en trabajar para conseguir un flujo de producto de alto valor añadido hacia el cliente, sin desperdicios en el proceso. En la planta, esto requiere hacer llegar los materiales adecuados en el momento oportuno y en la cantidad adecuada a los miembros del equipo que realizan el trabajo.
[digitization] requires valuing humans and our endless capacity for creative thinking and innovative problem solving.
Dado que siempre hay variaciones en las distintas partes del sistema, incluido el ser humano, las cosas estarán invariablemente fuera de la norma, por lo que es necesaria una acción correctiva. Jidoka, el segundo pilar, aborda las condiciones fuera de norma. Comenzó con Sakichi Toyoda, fundador de la fábrica de telares que dio lugar a Toyota Motor Company. Acabó inventando un telar totalmente automatizado. Por el camino añadió sensores físicos que paraban el telar cuando se rompía un solo hilo y señalaban que había un problema mediante la aparición de una bandera. Más tarde, esto le llevó a identificar posibles modos de fallo y a diseñar sensores en los equipos para detectar condiciones fuera de lo normal y detener el equipo cuando se alcanzaran determinados umbrales. En los procesos manuales, los miembros del equipo tiraban de la cuerda "andon" cuando se detectaban condiciones fuera de norma que podían provocar paradas de la línea.
Para tener un flujo coherente del producto y sus componentes se necesitan procesos estables, lo que requiere normalización. Existen normas para el diseño de productos, normas para el diseño de procesos y trabajo normalizado para las personas que realizan tareas manuales.
La razón por la que las personas están en el centro es que no sólo realizan el trabajo, sino que se espera de ellas que mejoren continuamente el sistema, lo que incluye reaccionar ante condiciones fuera de lo normal con una resolución creativa de los problemas. La propiedad y la responsabilidad están en primera línea y los grupos de trabajo formados por miembros de equipo, jefes de equipo y jefes de grupo son responsables de alcanzar objetivos de rendimiento agresivos y de realizar parte del mantenimiento preventivo más sencillo[1].
¿Cómo se aplica esto al mantenimiento de los equipos? El objetivo es disponer de equipos sanos que estén listos y sean capaces de producir exactamente las piezas que se necesitan cuando se necesitan con una calidad perfecta.
El mantenimiento justo a tiempo (JIT) significa el mantenimiento adecuado en el momento adecuado, ni demasiado pronto ni demasiado tarde. El mantenimiento preventivo es fundamental para que los equipos de Toyota funcionen a un alto nivel, pero se podría argumentar que, sin los datos adecuados, a menudo se realiza demasiado pronto. Es decir, se realiza un amplio conjunto de procedimientos de mantenimiento tanto si el equipo lo necesita como si no, para que funcione a un alto nivel "por si acaso" que, de lo contrario, podría provocar una avería en el equipo.
Otro enfoque del mantenimiento es esperar a que falle, como el sensor original del telar cuando se rompió un hilo. Este enfoque reactivo requiere una respuesta rápida para, en primer lugar, contener el problema y poner el equipo en funcionamiento y, a continuación, resolver el problema en su raíz para que sea improbable que vuelva a ocurrir. Podría decirse que es demasiado tarde.
Toyota avanza cada vez más hacia el mundo del mantenimiento predictivo. Desean saber de antemano para una máquina concreta que va a fallar de una manera específica y tomar medidas correctivas antes de que se produzca el problema.
Existen métodos avanzados, a través del "Internet de las cosas" y la analítica por ejemplo, que están aumentando lo que podemos predecir. Por desgracia, hoy en día cualquier sistema digital solo puede medir determinadas variables, los modelos analíticos tienen límites y, dado que la mayoría de los sistemas de las fábricas son complejos, únicos y están interconectados, hay un conjunto limitado de problemas que pueden gestionarse de forma puramente predictiva. Por lo tanto, seguimos necesitando personas que encuentren la causa raíz y desarrollen una solución creativa para resolver el problema. A menudo, resolver el problema es cuestión de probar cosas, de experimentar, es decir, de resolver problemas de forma adaptativa.
Ejemplos de casos de sensores inteligentes
KCF Technologies es un proveedor tecnológico que cree en el poder de la información digital para mejorar, no sustituir, la resolución creativa de problemas por parte de las personas. Su principal tecnología son los sensores avanzados, con la potencia informática de los análisis avanzados. Muchas de las ecuaciones que utilizan para predecir los fallos de los equipos se remontan décadas atrás a la ciencia fundamental de la ingeniería. Cuando existe una ecuación analítica que predice eficazmente, no es necesario que los sistemas de inteligencia artificial rastreen grandes volúmenes de datos para encontrar patrones. Basta con introducir los números correctos en el modelo matemático adecuado. Toyota es uno de sus clientes.
Ejemplo de planta Toyota
Toyota ha tenido un gran éxito con la tecnología KCF tanto para problemas predictivos como adaptativos.
Como ejemplo predictivo, se instalaron sensores en los motores de accionamiento de las cintas transportadoras y el análisis de los patrones de vibración permitió predecir un fallo inminente. Cuando las vibraciones superan los umbrales, el software activa un mensaje de texto y un correo electrónico. Los jefes y miembros del equipo hacen un seguimiento inmediato y, por lo general, determinan que deben programar la sustitución del motor por mantenimiento. A medida que la planta fue ampliando su uso, este tipo de acción de mantenimiento predictivo se llevó a cabo cientos de veces en miles de piezas de maquinaria crítica de la planta, y generó confianza en el sistema entre los miembros del equipo.
Yendo más allá del mantenimiento predictivo, los miembros del equipo también se dieron cuenta de muchos casos en los que los datos predictivos les permitieron introducir mejoras adaptativas en las configuraciones de los sistemas y en los procedimientos operativos estándar. Un ejemplo de ello fue el taller de pintura. Los datos de KCF mostraban sistemáticamente desequilibrios en los extractores del taller de pintura, relacionados con la acumulación de pintura en las aspas del ventilador a causa del proceso. Estos datos permitieron a los miembros del equipo evaluar y actualizar la frecuencia y los métodos de limpieza proactiva de las aspas del ventilador, eliminando así el problema de desequilibrio que, de otro modo, habría provocado el fallo prematuro de los cojinetes de soporte del ventilador y del motor y la estructura. La solución no fue obvia de inmediato y requirió un proceso de resolución de problemas más profundo con algo de ensayo y error.
Incluso hay ejemplos de una combinación de predictivo y adaptativo. Un ejemplo de ello se dio en una planta de Toyota que estampa piezas de acero. Se trataba de una planta antigua con equipos anticuados. Hacia finales de 2022, se produjo un fallo debilitador en un subsistema de la prensa de estampación. El resultado fueron muchas horas de inactividad, un estrés considerable para los miembros del equipo y gastos de capital considerables. El equipo se vio sorprendido por los fallos imprevistos y, en consecuencia, comenzó a colaborar con KCF en abril de 2023 para gestionar la salud de sus activos de forma más proactiva.
Un simple ajuste de sus ya sólidas prácticas de mantenimiento no bastaría para resolver los problemas específicos que conlleva el mantenimiento de los equipos más antiguos. El equipo de Toyota decidió que necesitaba una combinación de tecnología avanzada y conocimientos técnicos. Formaron un equipo interdisciplinar de ingenieros de fabricación, personal de mantenimiento de la empresa y de la planta, y analistas de KCF para encontrar la mejor manera de prolongar la vida útil de la prensa dos años más.
El equipo desplegó una serie de "IoT HUBS", diseñados específicamente para captar y procesar datos en maquinaria compleja e intermitente como las prensas de estampación. Los sensores se instalaron en una línea de prensas para probar su eficacia y los datos indicaron un grave deterioro en varios componentes clave de la prensa, aunque las soluciones no eran evidentes. A través de un proceso de ir a ver, identificar varias causas clave de fallo y probar varias ideas, el equipo dio con una alternativa para el sistema de bomba de freno hidráulico -que estaba tan anticuado que ya no había piezas de repuesto disponibles- que resolvió varios de los problemas. La tecnología también fue capaz de anticipar la necesidad de sustituir los cojinetes del motor principal, que fallaron previsiblemente 3 meses después.
Pero descubrieron que incluso este nivel de resolución de problemas no era suficiente. El conjunto de ajuste deslizante requería un enfoque de resolución de problemas más intensivo basado en los datos básicos de corriente y vibración suministrados por los sensores. El equipo detectó un cambio en la forma de onda que parecía indicar que se estaba produciendo un fallo en la barra del rotor y, poco después, observó un pico de vibraciones en la caja de engranajes. Como suele ocurrir, no había mucho tiempo de inactividad para inspeccionar el problema, y el ajuste de la corredera era de difícil acceso. Un equipo interfuncional identificó las posibles comprobaciones y las clasificó de más fáciles a más difíciles, creando un plan de mantenimiento proactivo viable y optimizado, apoyado por una supervisión remota continua en línea hasta el tiempo de inactividad previsto y la inspección programada varios meses después.
Conclusión
El movimiento lean comenzó con su modelo, el Sistema de Producción Toyota. El núcleo del lean son las personas que se encuentran en el gemba, donde se realiza el trabajo, y que responden a las anomalías señaladas por el sistema.
La Industria 4.0 es la visión de fábricas automatizadas dirigidas en gran medida por ordenadores que planifican y deciden qué hacer y cuándo. Presumiblemente, los problemas los resuelven los sistemas informáticos, a menudo con la ayuda de IA avanzada y sistemas analíticos.
Existe otro tipo de resolución de problemas, la adaptativa, en la que el problema no puede definirse fácilmente y las soluciones no son obvias. La resolución adaptativa de problemas requiere personas en el gemba que con sus sentidos puedan encontrar la causa raíz y resolver el problema, a menudo mediante una serie de experimentos.
Hemos dado ejemplos con un tipo de tecnología, ofrecida por KCF Technologies, de sensores y sistemas basados en ecuaciones de ingeniería que pueden predecir cuándo fallarán los equipos y, a menudo, aportar soluciones de tipo predictivo. "A menudo" no es siempre. KCF analizó los datos de sus clientes y calculó que aproximadamente el 50% de los problemas eran predictivos y el otro 50% requerían una solución adaptativa. Su experiencia también sugiere que, con el tiempo, a medida que se van recogiendo los frutos maduros, cada vez son más los problemas que requieren una solución adaptativa.
Recomendamos que las empresas manufactureras que no hayan invertido mucho en las capacidades de resolución de problemas de su personal de primera línea lo hagan paralelamente a la introducción de tecnologías digitales avanzadas. Esto puede significar ir más despacio en la introducción de las tecnologías, incluyendo el pilotaje de módulos individuales antes del despliegue generalizado. Algunas empresas están asociando a profesionales lean con expertos internos en TI con grandes resultados, como vimos en la colaboración entre los expertos de planta de Toyota y los expertos en tecnología de KCF. Sospechamos que, con el tiempo, la automatización y las tecnologías digitales harán que haya menos personas en las fábricas realizando trabajos manuales. Pero habrá una necesidad aún mayor de personas pensantes en el gemba que resuelvan los problemas a medida que los identifiquen el software y las personas. De este modo, la tecnología apoya a las personas y los procesos.
[1] Jeffrey K. Liker, The Toyota Way, segunda edición, McGraw Hill, 2020.