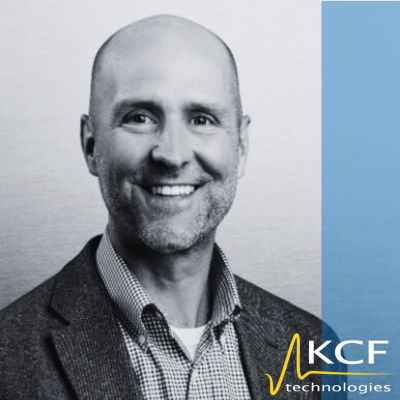
Dr. Jeremy Frank, CEO and Founder, KCF Technologies
Dr. Jeremy Frank, a distinguished figure in industrial innovation, originally from Pittsburgh, PA, where his early involvement in his father’s business analysing workplace accidents sparked a lifelong pursuit of machinery safety and efficiency. A Penn State alumnus with a PhD in Mechanical Engineering, Jeremy was deeply influenced by Dr. Gary Koopmann, leading to the co-founding of KCF Technologies in 2000. Under his leadership, KCF has pioneered advancements in wireless vibration sensing and machine health monitoring. Today, the company is a global leader in predictive maintenance, monitoring over 135,000 machines across numerous industries, driven by Jeremy’s vision of eradicating unplanned downtime and enhancing industrial safety.
Introduction
Contrary to intuition, machine health degradation is not the machine problem. From observations gleaned from over 700 manufacturing locations and over 135,000 assets, KCF Technologies found that only about 20% of machine degradation comes from normal wear and tear. This means that the other 80% is inflicted by something unexpected.
It varies by industry, and by machine application, but across industries, 15% of machine damage comes from operating conditions, 40% from imperfect maintenance, and 25% from system design.
And that is a good thing, because proactively attacking those root causes is achievable. The solution is mature and represents the largest actionable
opportunity to reduce downtime and eliminate waste.
As studied by the U.S. Department of Energy and OHSA, machine health and reactive maintenance practices are responsible for trillions of dollars of lost productivity in the U.S., the greatest percentage of industrial injuries, and energy and emissions waste even larger than that of vehicles.
To solve the industrial machine health problem, there are three key requirements:

Right Data
The right data starts by gathering all the necessary information for that application. It needs to be comprehensive in terms of sensor types, and it needs to be high-fidelity and frequent enough to discern the root cause.
Right Analysis
The right analysis needs to organise and simplify data into actionable insights. This starts with physics and engineering, and
transitions to include AI to make the analysis as easy and automatic as possible.
Right Action
The right acton requires that the insights must be served to the right person, at the right time, in the right place and in a way they can understand, to elevate workers to act on the data and solve problems.
THE RIGHT DATA
To dive a little deeper, the Right Data requires collecting large sets of data to provide sufficient evidence for action. In the context of diagnostics and vibration analysis specifically, we have learned with our customers that two key things are required: full spectrum data, which paint the full picture of machine behavior and that the collected data is analysed ofen enough to match behavioral changes on each machine application. Many applications require data once a minute, which puts a challenge on wireless sensor systems in particular. But the solution exists.
For example, conditions like cavitation, resonance, and hard stops and starts, come and go based on operations. Although they are short in duration, these conditions cause excessive damage over time and lead to premature failures on bearings, couplings, and seals. Because they happen for short durations, sampling full spectrum data frequently down to once per minute is required to observe and diagnose these types of conditions.
THE RIGHT ANALYSIS
The next pillar “The Right Analysis” is all about reducing and simplifying data. There is clearly a global shortage of skilled workers. It is more challenging than ever to get all the work done, to get the right people trained & prepared, and to validate the work. And it is only going to get harder, at least in the next 5-10 years.
That means it’s time to replace the traditional approach, which required trained analysts to methodically sift through data, looking for anomalies or problems. And even that was an order of magnitude better than analysts performing quarterly or monthly PdM routes, manually walking the plant for data acquisition or, in some cases, being reactive and blind, with essential machine uninstrumented. But there is a better way.
New workflows begin when the AI/ML models automatically identify and diagnose the issue. For example, rotating looseness and cavitation on a critical pump is identified with high-definition vibration sensors, a ticket with all relevant information is created, and only then, is the plant team deployed to investigate and eliminating the root cause of the problem.
THE RIGHT ACTION
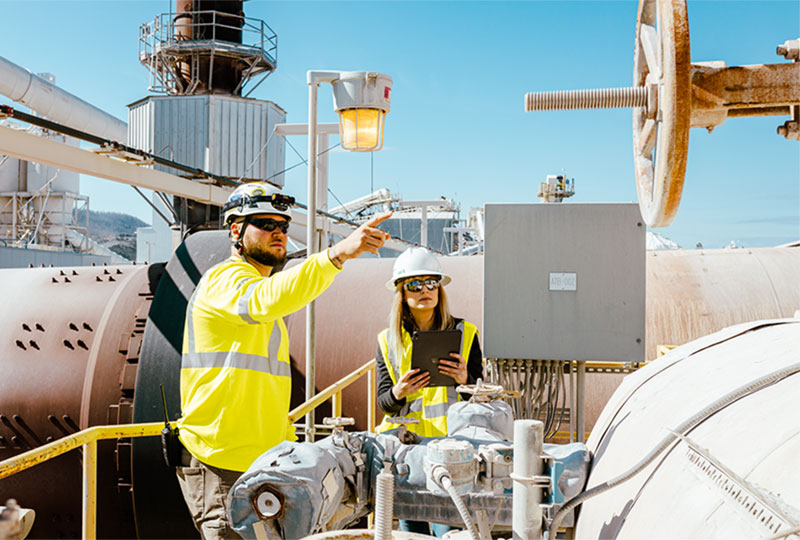
With the Right Acton, workers are elevated to understand root causes and eradicate them proactively. They can assess and improve the quality of maintenance, optimize machine health, and eliminate unplanned events. It’s all about getting the right data, doing the right analysis, and getting it into the hands of the worker who can take the right action.
Stemming from the right analysis, the right person can be deployed to the right place, at the right time. Commonly, companies using remote monitoring will follow this workflow:
- The maintenance team leader sees a prioritized list of issues and sets the plan of action for each issue.
- The analyst understands the AI/ML model diagnosis and communicates the recommendation to the team with supporting evidence.
- The millwright, electrician, or maintainer sees the alert with supporting evidence and enough detail to understand and confirm the issue.
- The supporting data and root-cause evidence are readily available – no need to search through raw data, but simply reference the most important information necessary to adjust the action plan, confirm maintenance, and document the solution.
It’s all about getting the right data, doing the right analysis, and getting into the hands of the worker who can take the right action.
The Right Data, Right Analysis, and Right Action leads to four surprising benefits of predictive maintenance.
INCREASED SAFETY: A HIDDEN GEM OF PREDICTIVE MAINTENANCE
Safety is paramount in a manufacturing or industrial setting. However, the most common time for injuries to occur in the workforce is during times of unexpected maintenance. Additionally, those that are using route-based maintenance routinely put themselves in dangerous areas necessary to take readings. Both scenarios can be eliminated with a properly implemented PdM program. Predictive maintenance (PdM) elevates safety standards by proactively identifying potential equipment failures before they occur. This foresight prevents accidents and ensures a safer working environment, contributing to employee well-being and compliance with safety regulations.
REDUCTION IN ENERGY CONSUMPTION: ECO-FRIENDLY OPERATIONS
One often-overlooked benefit of PdM is its role in reducing energy consumption. Without proper monitoring techniques, equipment can be using significantly more energy than needed. In some instances, companies that have invested in predictive maintenance have seen savings as much as $1M in just one year from the insights they received by continuously monitoring their energy consumption. By optimizing equipment performance and preventing over-exertion or underutilization of machinery, predictive maintenance ensures energy-efficient operations. This not only cuts down costs but also supports eco-friendly practices, aligning with the growing emphasis on sustainability in the industry.
UNDERSTANDING PROCESS ANOMALIES AND CHANGES
Process changes can create strange anomalies in vibration data. In fact, over 40% of machine failures are directly caused by improper operating conditions and system configuration. Without having streaming data of operating parameters, it can be difficult to correlate where spikes in vibration or other health indicators are coming from. Predictive maintenance offers a deep dive into the intricacies of industrial processes. When pairing nearly continuous machine health data with process data, clear correlations can be made. By monitoring equipment performance and analyzing data trends, PdM helps in understanding process anomalies and changes, allowing for timely adjustments. This insight is crucial for developing new standard operating practices that prioritize machine health without sacrificing throughput.
IDENTIFYING IMPROPER MAINTENANCE: A STEP TOWARDS OPTIMIZATION
The uncomfortable truth is nearly 40% of machine failures are due to improper maintenance. While this is almost never malicious, anytime human intervention is introduced, it opens room for human error. Simple errors like over or under lubricating or improper alignment can cause major issues down the road. With real-time data, the health of the equipment after maintenance can be seen almost instantly. By simply studying if the trend line goes up or down, it can be easy to identify when maintenance has helped or if it has hurt – in some cases actually introducing new problems. PdM helps in identifying instances of improper maintenance, ensuring that all interventions are effective and contribute positively to equipment health. This aspect of PdM is crucial for maintaining a high standard of equipment care and prolonging the life of machinery.
Gain an Unbeatable Competitive Edge
Gain access to our experienced team of certified vibration analysts and engineers and amplify the value of your SMARTdiagnostics investment to solve the problems that are most important to your business.
Our partnership starts with a conversation. Contact us today to learn more about how SmartDiagnostics Sentry Services™ can solve your manufacturing problems.