Want to eliminate unplanned downtime and extend the lifespan of your critical assets?
Contact us to see how our comprehensive, AI-driven machine health platform can optimize your operations.
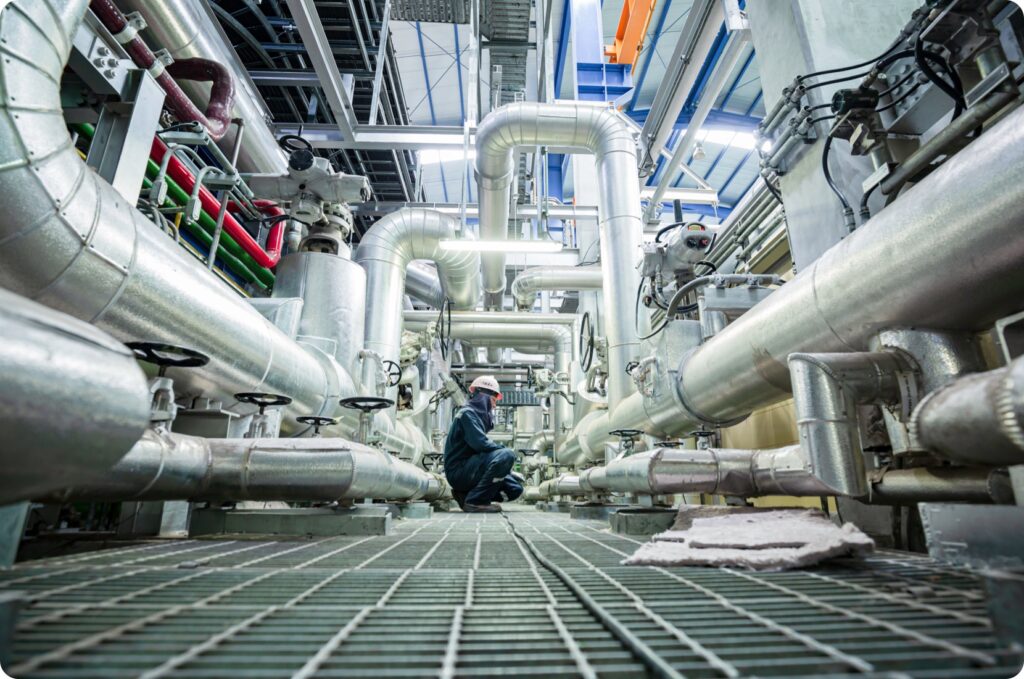
Leveraging Predictive Insights for Planned Outages
SMARTdiagnostics detected a cracked pump base, allowing repair during planned downtime and avoiding $86K in unplanned losses at BASF.