Want to eliminate unplanned downtime and extend the lifespan of your critical assets?
Contact us to see how our comprehensive, AI-driven machine health platform can optimize your operations.
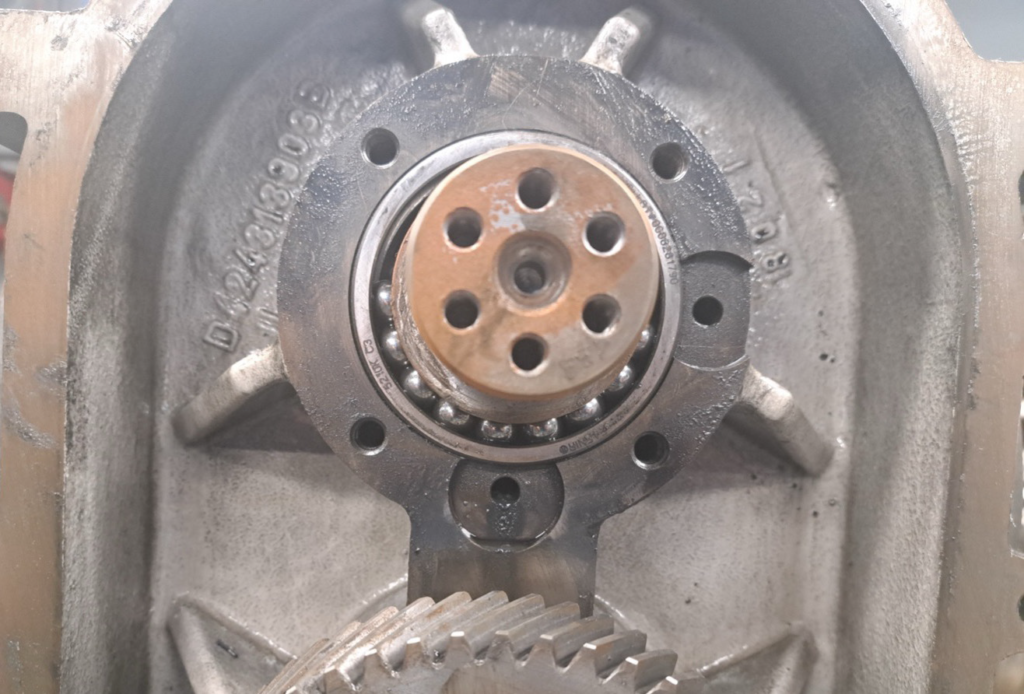
Vacuum Pumps
Vacuum pumps are critical in many manufacturing processes. KCF's comprehensive machine health monitoring empowers you with the data and insights needed to minimizing unplanned downtime.